AIA Course: #BE2022F
Earn: 1 AIA LU/HSW; 1 IIBEC CEH; 0.1 IACET CEU
To complete the quiz and receive a certificate of completion, follow this link: ce.buildingenclosureonline.com/BE2022F
Sponsored by:
Learning Objectives:
After reading this article, you should be able to:
- Assess the purpose of a tapered insulation system and how it works.
- Develop a basic comprehension of tapered polyisocyanurate insulation panels and how they affect roof performance: design options, crickets.
- Identify design intent and what key questions to answer when designing a tapered polyiso roof design.
- Recognize how IECC codes affect tapered polyiso insulation systems.

Why is Drainage Necessary?
When someone learns that ‘tapered designer’ is an occupation, their usual reaction is asking “what does that mean?” A simple response is that a tapered designer’s role is to ensure that a roof does not become a swimming pool when it rains. A roof should not become a water feature! Architect Magazine reported that almost half of all building-related issues are due to water intrusion.1 Furthermore, 75 percent of construction defect disputes are related to roof failure.2 This is magnified in commercial roofing where a majority of buildings incorporate low-slope roofs, some completely flat. We are all familiar with the steep slopes seen in residential roofing that use gravity to handle rainwater, but when the roof decks do not provide adequate slope to the drain such as in low-slope or flat roofs, a special consideration needs to be taken to eliminate standing water by adding positive drainage with tapered insulation panels. This visual article will outline tapered design fundamentals to help architects and building designers achieve positive drainage in their low slope applications.
Image of an industrialized area of Secaucus, N.J.
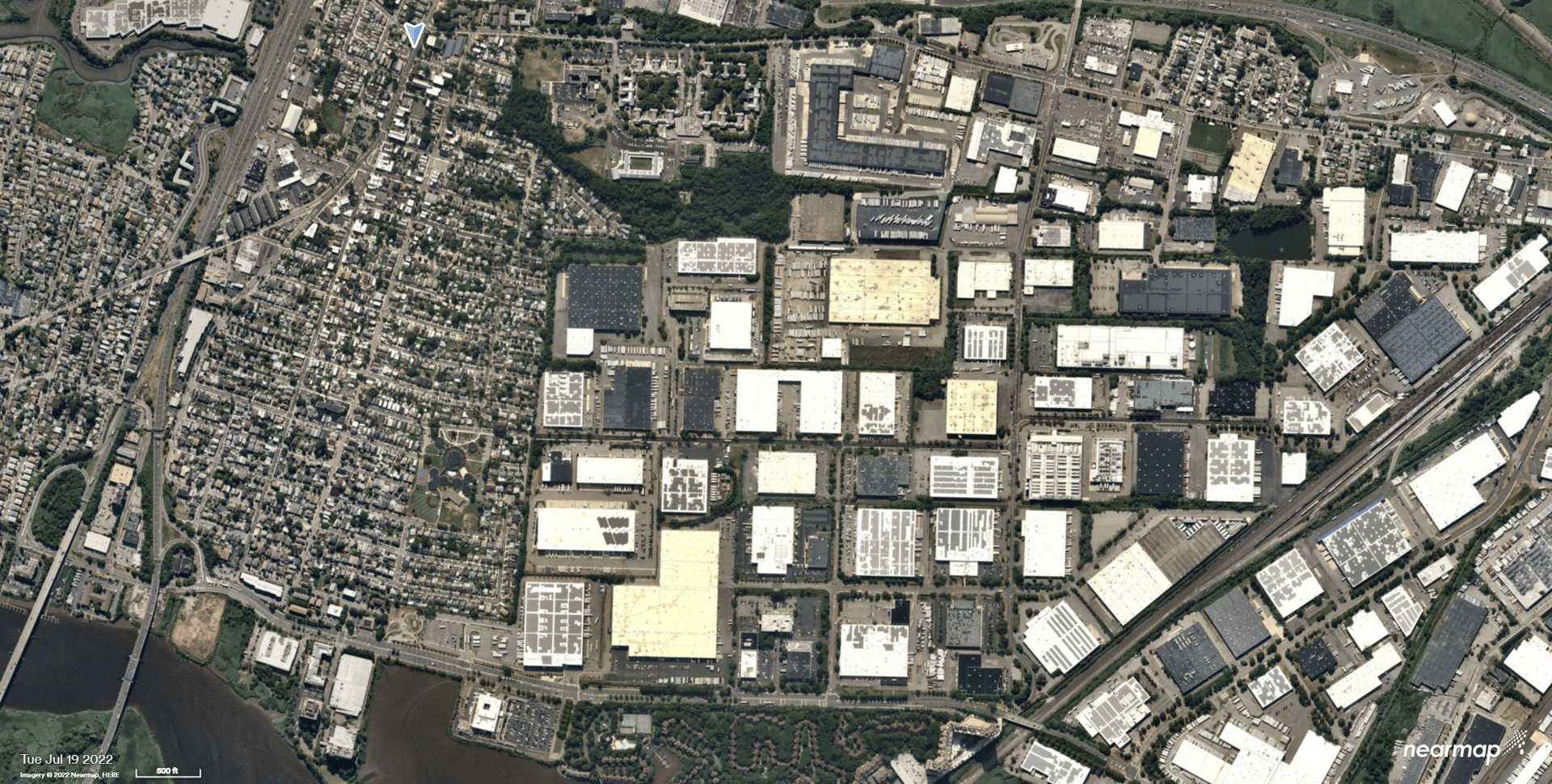
Figure 1
Ensuring your building is watertight at the roof level and preventing water infiltration is only one benefit of a tapered insulation system. Other performance aspects such as R-value and compressive strengths will later be analyzed. Focus on the concentration of commercial roofs in the heavily industrialized area pictured. Whether those are storage or manufacturing facilities, office and retail spaces, even large residential apartment or condo complexes, their roofs cover significant square footage. Given the large footprint of commercial buildings, managing rainwater is the key component of tapered insulation design.
Standing water on a roof is a clear indicator that there isn’t positive drainage present to allow for water to evacuate the roof in a timely manner. The term “positive roof drainage” is defined in the 2018 International Building Code as “the drainage condition in which consideration has been made for all loading deflection of the roof deck, and additional slope has been provided to ensure drainage of the roof within 48 hours of precipitation.”3 Even though a flat roof could be considered watertight, the potential for problems still may arise. Standing water promotes vegetation growth, and issues such as seam separation from material degradation or freezing damage increase the potential for that water to make its way into the system. A dangerous problem slow moving or ponding water also creates is added weight to the structure. To put it into perspective, one gallon of water weighs just over 8 pounds. If an inch of standing water is present on a roof, it can add thousands of pounds to the building structure and lead to life-safety concerns due to a roof collapse. Tapered insulation panels help evacuate rainwater by pointing it to drains or scuppers and creating positive drainage.
Tapered insulation systems work the same way as steep-slope shingle roofs—just with a much more gradual slope. Instead of inches per foot, the 2018 IBC requires a minimum slope of 1/4-inch per foot for membrane roof systems, and a minimum slope of 1/8-inch per foot for coal tar pitch roofs. New construction must comply with the minimum slope requirements in IBC Section 1507, which outlines specifications for roof assemblies and rooftop structures. Recovers or roof replacements of existing low slope roofs are exempt from the minimum 1/4-inch per foot slope requirement. Understanding these constraints can allow for a more fine-tuned tapered design that achieves project-specific goals.
Tapered Polyisocyanurate
Polyisocyanurate, referred to as polyiso in short, makes up over 80 percent of the commercial roofing market share. It has the highest thermal efficiency in terms of R-value at 5.7 per inch. R-value is the capacity for an insulating material to resist heat flow. The higher the R-value, the greater the insulating value. Expanded polystyrene, or EPS, is a popular alternative, but since it has less thermal efficiency, you have to use more of it to compensate for energy losses. Polyiso has very low ozone depleting potential as well as very low global warming potential. It can use recycled content in the facer. It is free of hydrofluorocarbon, an ozone depleting chemical, and can even contribute towards Leadership in Energy and Environmental Design, or LEED, a global green building rating. With 20 polyiso manufacturing facilities nationwide, material is readily available and allows for a great variation of design flexibility to meet job requirements. There are different panel facers available such as felt or recycled and coated glass. Felt or recycled content facers are standard but do not have the reinforced strength of coated glass. Coated glass facers are made by mixing fiberglass in a slurry and gives polyiso panels added strength against job-site damage and greater resistance to moisture intrusion, all leading to longer assembly life cycles. There are also different formulations like non-halogenated which eliminate halogenated flame retardants in its chemical makeup. Halogenated flame retardants are on the Red List, a list of worst-in class chemicals and materials identified for their risk to the environment.4 This allows the range of non-halogenated polyisocyanurate panels to be categorized as Red List free and meet even greater ecological initiatives. Polyiso is a versatile material successfully used to meet code approval requirements for FM (Factory Mutual) and UL (Underwriter’s Laboratory), among others.
Tapered polyisocyanurate is available in thicknesses from 1/2 to 4.5 inches, however, smoothing the transition to a height of 0 inches cannot be reached with these panels. There are other products on the market like tapered edge strips that can be utilized to aid the transition to the roof deck. Tapered panel systems are available in slopes from 1/16-inch per foot to 1/2-inch per foot. The standard panel size is 4 feet by 4 feet, and a panel size of 4 feet by 8 feet is available if specified (and may require longer lead times to fulfill). There are also different compressive strengths that can be catered for specific applications such as amenity spaces with paver systems. Tapered polyiso is compatible with all roofing systems including built-up roofing, ballasted, and modified bitumen. It can be used with coverboards and also can be directly installed to the deck since it is the only foam plastic to pass UL 1256, a fire abatement standard for fire testing of a roof deck construction and FM 4450, qualifying tapered polyiso as a Class I assembly component when part of an insulated steel deck.5 This is because it has “low fire spread below the deck, adequate simulated wind uplift resistance, minimum heat damage potential and adequate strength” at the conclusion of FM’s fire testing.6
A collection of tapered panel system profiles.
Figure 2
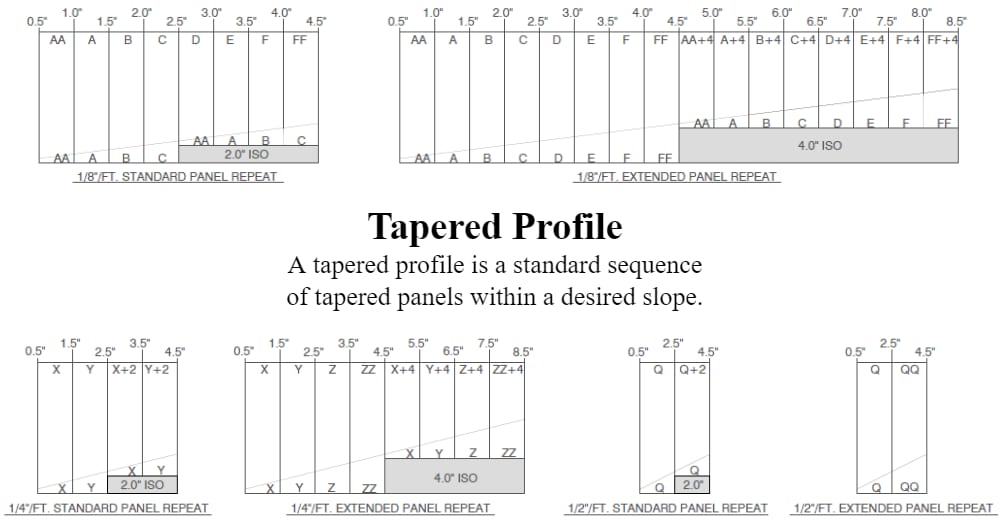
Slope is the angle at which the ends of the tapered panel differ, in inches per foot. There is a thinner leading edge and a thicker back edge. A Q-panel, for example, is part of the 1/2-inch per foot tapered slope system with a 1/2-inch leading edge and ends at 2.5 inches. Remembering that 4 feet by 4 feet is the standard panel size, it gains 2 inches in height across the length of the panel. It is possible to solve and confirm the slope at hand by dividing the rise over the run, or 2 inches divided by 4 feet, equaling and confirming 1/2-inch per foot slope. A tapered insulation system includes flat fill insulation used under the tapered panels to build the sequence. This is called a tapered panel repeat- the amount of tapered panels installed before a flat fill panel is required. Base layers are flat insulation panels installed in conjunction with the tapered system that help the system reach a certain insulating property.
Tapered panel profiles are a sequence map for the contractor and roofing installer that shows what order the tapered insulation panels will be installed. Most of the panel systems use a combination of single and double letters to distinguish slope and repeat, while 1/16-inch per foot is labeled numerically and is mainly used to enhance existing slope and should not be used as the sole field slope. 1/8-inch per foot is a common slope used for reroof applications with profiles from AA - FF. We have the National Roofing Contractors Association, or NRCA standard of 1/4-inch per foot which is available in two different profiles (X-ZZ, or G-I panels) depending on the minimum thickness requirements. Three-eighths of an inch per foot (SS, TT panels) is a slope that is favored in the west and mountain regions for swift drainage, as areas have to manage sudden, large quantities of rain. Half of an inch per foot (Q, QQ panels) is commonly used for crickets and drain sumps. Sumps are an area of exaggerated slope within a certain distance of the drain or scupper and can be designed with tapered panels, or field-fabricated as needed. A system at 1/2-inch per foot can quickly accumulate tall material heights in short distances so it is also not typically used as the field slope. There are other manufactured slopes which are uncommon such as 3/16-inch per foot, and overall slopes that can be fabricated on-site by stacking panels together to achieve a desired total slope.
The amount of panels applied before flat fill insulation is required is a repeat. The system repeat can go anywhere from one to eight panels depending on the slope being used and whether it is a standard or extended system. A lower repeat, typically a standard system, equals a lower material cost but also means more squares of material to be handled and applied to the roof. A higher system repeat is associated with extended panel systems and leads to an overall higher material cost, because the system comprises thicker panels. However, extended panel systems can reduce squares handled and applied up to forty percent. These savings are directly related to labor costs as well as adhesive costs in adhered applications, which far exceed the nominal material upcharge of the extended panels.
Examples of tapered design solutions.
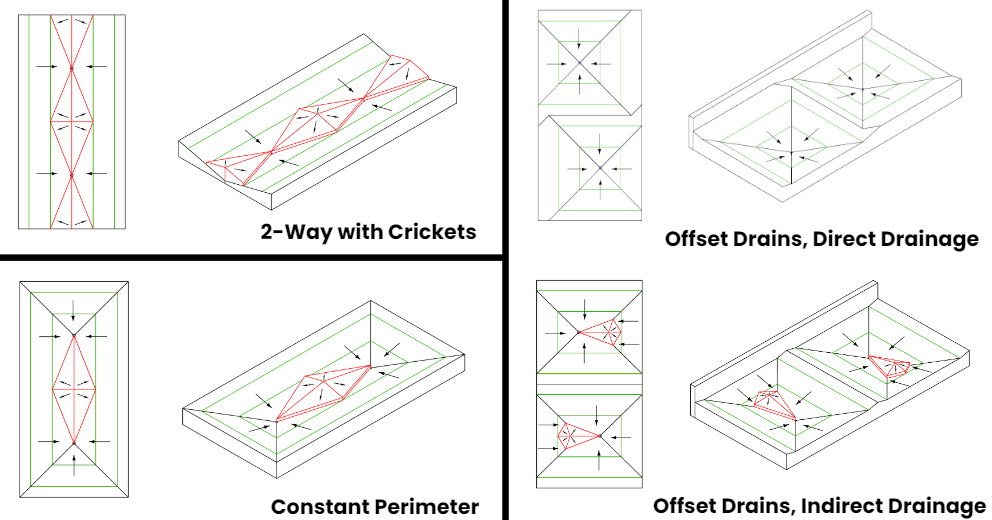
Figure 3
As unique as humans are, the same can be said for the built environment we work in. Each building has its own story, shape, function, and there is no one-size-fits-all solution when designing with tapered panels. A possible design for a roof with internal drains is to point the tapered panels in a way to create a single valley between the drains, connecting them. A two-way slope is straightforward to install and preferred by contractors for its minimal cutting waste as more full panels can be utilized and laid out in straight lines. However, this design can allow for water to sit in the valley and against the roof perimeter without being able to evacuate in a timely manner. There is a design element that can be added to increase drainage: crickets. Crickets are built with cut tapered panels and are an overlay to the tapered system. Their purpose is to help divert water to the drain by stretching out the flat valley they cover into separate, smaller valleys at the cricket’s edges.
While there is direct flow to the drains from the tapered system, there is indirect flow from the crickets. Crickets are necessary to aid in rainwater mitigation but can also introduce issues like standing water at their edges if utilized incorrectly. In the case of offset drains seen in Figure 4, the upper design solution is direct but requires more miter cut ridges and valleys. By stretching out the valleys and lining up the drains, the lower solution simplifies the amount of cutting. Crickets are added because they are needed to help push water around the expanded valley. The perimeter shape of the roof and drain placement dictate the outcome of the tapered design, especially when designing for a constant perimeter height. This is when the tapered system has the same max height around the entire roof perimeter, but this cannot always be achieved if the drains are not centrally located and aligned. It is important to remember the performance expectations when considering a tapered insulation system design. The application method, drainage expectation, and budget are critical when finding the right balance for clients.
The following animation helps to visualize how tapered panels are arranged in a few simple designs to point rainwater towards drains and evacuate water off of a roof, including the aforementioned designs above.
Tapered panel designs with animated rainwater simulating water evacuation. Video courtesy of GAF; credit: Tapered Design Group.
The Necessity of Crickets
Crickets, or saddles, are a necessary design feature and can work efficiently—if they are designed correctly. Crickets, or saddles, are an overlay to a tapered insulation system or to a flat-insulated structurally sloped system by diverting water to the drains.
Diagram of a cricket and common terminology.
Figure 4
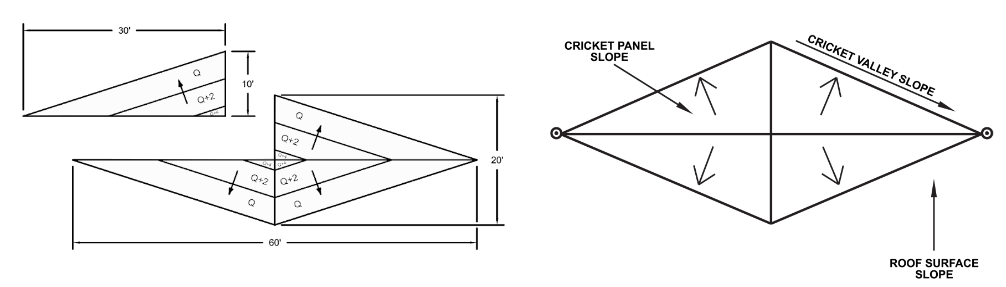
Crickets are a design feature that can work efficiently if they are designed correctly. Crickets are assembled from cut tapered panels, so they have their own panel slope to refer to. The unwritten rule is that the cricket panel slope should be twice of the roof field or tapered slope. If the tapered system is 1/4-inch per foot then the crickets would need to be 1/2-inch per foot. Cricket valley slope is the critical aspect that determines how effective a cricket will be. If the cricket design does not create enough of a slope along the outer edges it can introduce standing water. In most cases, the wider the cricket, the greater the cricket valley slope will be, aiding in moving water off of the roof.
The NRCA states that the total cricket width should be between one-quarter and one-third of the overall length, erring on the wider side to ensure proper water diversion. This works for a majority of cricket applications, but it is still possible for crickets to be inefficient if the designer does not consider the cricket valley slope in regards to the tapered or roof field slope. Wider is always better if the space permits. Working with a professional tapered designer ensures that crickets are adequately sized. Panel designers are also the first people who can offer design recommendations and alternatives.
Building owners can protect their investment even if the roof only requires crickets to push water to drains, with the roof field slope built into the deck. Slope can be already designed into the roof structure using sloped wooden trusses or metal beams installed at a specific angle to achieve a desired roof slope. These projects see the most on-site changes decided by the roofing installer at the time of installation, whether their decision is to save on labor or minimize cutting by reducing the size of the crickets. These field reductions are problematic when the provided plan is ignored because planning cannot be done in advance to prevent the potential of standing water due to undersized crickets. Changes to the design such as reducing cricket width should be communicated with the tapered insulation designer to confirm if the reduction in size will still yield an efficient cricket that drains rainwater off of the roof.
Undersized crickets that leave standing water and accumulated dirt because they are inefficient for their application.
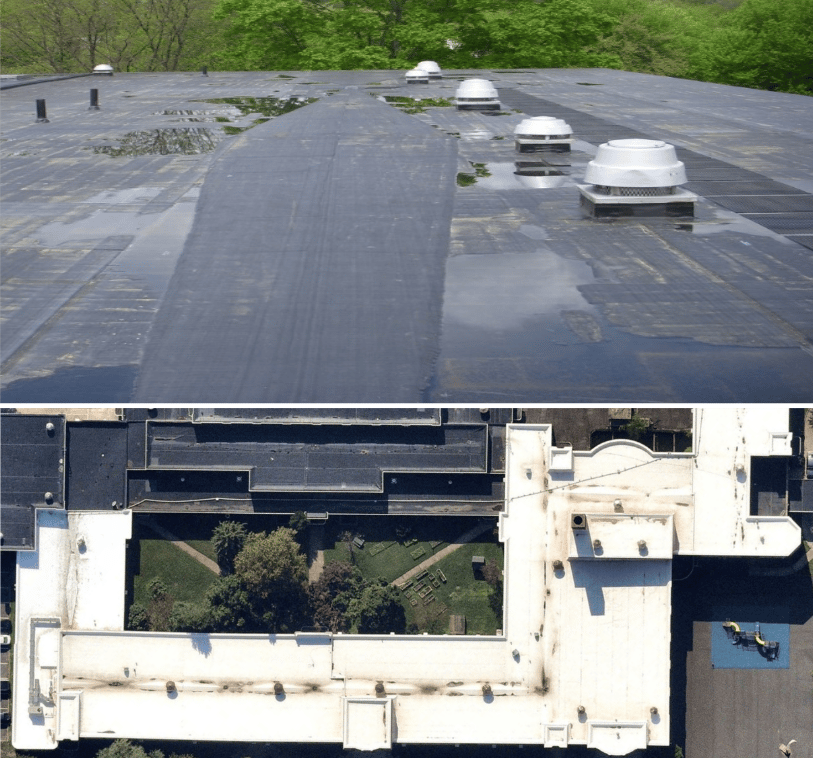
Figure 5
To help visualize these cricket issues, an image of a cricket is provided that has been reduced in size so drastically that it does not resemble a cricket nor function as it needs to. The cricket valley slope in this example is close to 0 inches per foot, evident by the standing water seen on the roof. Undersized crickets do not divert water quick enough to the drains and allow dirt to gather, encouraging algae and bacteria growth. While membrane manufacturers may allow for a ponding exclusion in their material warranties because they believe the membrane will stand the test of time, allowing for undersized crickets can prematurely shorten the service life of the membrane and not only cause performance issues, but aesthetic issues as well if lower levels with collected dirt can be seen from above.
References
1. Seward, Aaron. Architect Magazine, “When It Leaks It Pours,” June 2011. http://www.architectmagazine.com/roofing/when-it-leaks-it-pours.aspx
2. McCloskey, Christopher L., Bricker Construction Law, “Defective Work: What to do when the roof leaks?,” Summer 2011 Newsletter. https://www.bricker.com/insights-resources/publications/defective-work-what-to-do-when-the-roof-leaks
3. 2018 International Building Code (IBC). https://codes.iccsafe.org/content/IBC2018/chapter-4-special-detailed-requirements-based-on-occupancy-and-use
4. International Living Future Institute, LBC Red List.
https://living-future.org/lbc/red-list/
5. UL 1256, 4th Edition, January 12, 2007—UL Standard for Safety Fire Test of Roof Deck Constructions.
https://global.ihs.com/doc_detail.cfm?document_name=UL 1256&item_s_key=00096863
6. FM Approval 4450, Class I Insulated Steel Roof Decks, February 1, 1989.
https://standards.globalspec.com/std/20782/FMAPPROVAL 4450
End Notes
1Architecture 2030. “Accelerating to Zero by 2040!” Oct. 2019. Web. 22 Feb. 2022. <https://architecture2030.org/accelerating-to-zero-by-2040/ >
2https://www.un.org/en/academic-impact/sustainability Accessed 2/4/2022 at 9:33am.
3Intergovernmental Panel on Climate Change. “Climate Change 2021: The Physical Science Basis Working Group I: Contribution to the Sixth Assessment Report of the Intergovernmental Panel on Climate Change.” Oct. 2021. Web. 4 Feb. 2022. <https://www.ipcc.ch/report/ar6/wg1/downloads/report/IPCC_AR6_WGI_SPM_final.pdf>
4National Oceanic and Atmospheric Administration (NOAA). “2021 U.S. billion-dollar weather and climate disasters in historical context.” 24 Jan. 2022. Web. 6 Feb 2022.
5Intergovernmental Panel on Climate Change. “Climate Change 2021: The Physical Science Basis Working Group I: Contribution to the Sixth Assessment Report of the Intergovernmental Panel on Climate Change.” Oct. 2021. Web. 4 Feb. 2022. <https://www.ipcc.ch/report/ar6/wg1/downloads/report/IPCC_AR6_WGI_SPM_final.pdf>
6Headline Statements. Intergovernmental Panel on Climate Change. Web. 8 Feb. 2022. <https://www.ipcc.ch/sr15/resources/headline-statements/>
7Architect Magazine Staff and Mazria, Edward. “Architecture 2030's Open Letter to the UN Framework Convention on Climate Change Calls for Revised Carbon Emission Reduction Targets.” Architect Magazine, 6 Nov. 2020. Web. 18 Feb. 2022. <https://www.architectmagazine.com/technology/architecture-2030s-open-letter-to-the-un-framework-convention-on-climate-change-calls-for-revised-carbon-emission-reduction-targets_o>
8Pedersen, Martin C. “Edward Mazria With Some Good News About Combating Climate Change.” “Common Edge,” 27 July 2020. Web. 9 Feb. 2022. <https://commonedge.org/edward-mazria-with-some-good-news-about-combating-climate-change/>
9Carbon Leadership Forum. “Embodied Carbon 101.” 17 Dec. 2020. Web. 8 Feb. 2022. <https://carbonleadershipforum.org/embodied-carbon-101>
10NYC Mayor’s Office of Climate & Environmental Justice. “Energy Benchmarking:
Energy map.” New York City Energy & Water Performance Map.” Web. 8 Feb. 2022. <https://www1.nyc.gov/site/sustainability/codes/energy-benchmarking.page#:~:text=Over 70 percent of New,on energy and water management>
11Center for Sustainable Systems, University of Michigan. 2021. "U.S. Cities Factsheet." Pub. No. CSS09-06. Web. 8 Feb 2022. <https://css.umich.edu/factsheets/us-cities-factsheet#:~:text=It is estimated that 83,to live in urban areas>
12Saulsbery, Gabrielle. “Peak Demand: Parsippany-based GAF addresses a serious labor shortage by training new roofers.” NJBiz. 17 May 2021. Web. 17 Feb. 2022. <https://njbiz.com/peak-demand-gaf-roofer-training/>
13La Rocca, Melanie E. “Service Notice: Local Law 92 of 2019 and Local Law 94 of 2019: Green and Solar Roof Requirements for New Buildings and Complete Roof Replacements.” NYC.gov. Oct. 2019. Web. Feb 9 2022. <https://www1.nyc.gov/assets/buildings/pdf/green_roof_solar_ll92-n-94of2019_sn.pdf>
14Urban Green Council and The Nature Conservancy. “NYC’S SUSTAINABLE
ROOF LAWS.” Urban Green Council. Dec. 2019. Web. 10 Feb. 2022. <https://www.urbangreencouncil.org/sites/default/files/sustainable_roof_laws_brief_final_12.11.19.pdf>
15Torgelson, Nathan. “Seattle Green Factor.” Seattle.gov. Web. 18 Feb. 2022. <https://www.seattle.gov/sdci/codes/codes-we-enforce-(a-z)/seattle-green-factor#:~:text=You can choose from a,or create a food garden>
16Seattle Department of Construction & Inspections. “Renewable Energy and Solar-Ready Roofs for Commercial Buildings.” Seattle.gov. 18 Oct 2021. Web. 14 Feb 2022. <http://www.seattle.gov/DPD/Publications/CAM/Tip422.pdf>
17Washington, D.C. Department of Energy & Environment. “Green Roofs in the District of Columbia.” Web. 22 Feb. 2022. <https://doee.dc.gov/greenroofs>
18Washington, D.C. Department of Energy & Environment. “Solar Initiatives.” Web. 22 Feb. 2022.
19World Green Building Council. “Whole Life Carbon Vision.” WorldGBC.org. Web. 4 Feb. 2022. <https://www.worldgbc.org/advancing-net-zero/whole-life-carbon-vision>
20Tobias, Michael. “Green Building Trends: Pros & Cons of Passive House Construction.” NewYork Engineers. 12 October 2021. Web. 17 Feb. 2022. <https://www.ny-engineers.com/blog/green-building-trends-pros-cons-of-passive-house-construction>
21Taylor, T.J. “Eliminating Fastener Thermal Bridging in Low Slope Roofs: Energy Efficiency Savings versus Installation Costs.” Open Journal of Energy Efficiency. 9, 94-110. June 2022. Web. 20 Feb. 2022. < https://doi.org/10.4236/ojee.2020.92007>
22Ibid.
23World Green Building Council. “Whole Life Carbon Vision.” WorldGBC.org. Web. 4 Feb. 2022. <https://www.worldgbc.org/advancing-net-zero/whole-life-carbon-vision>
24Ellen MacArthur Foundation. “What is a circular economy?” Web. 17 Feb 2022. <https://ellenmacarthurfoundation.org/topics/circular-economy-introduction/overview>
25Reuters. “U.S. corn-based ethanol worse for the climate than gasoline, study finds.” Autoblog. 21 Feb. 2022. Web. 2 Feb 2022.
26GAF Roof Views. “Welcome to the Future of Asphalt Recycling.” GAF.com. 21 April 2021. Web. 17 Feb 2022. <https://www.gaf.com/en-us/blog/welcome-to-the-future-of-asphalt-recycling-281474980090173>
27MYCOCYCLE. Web. 22 Feb 2022. <https://mycocycle.com/>
28Acaroglu, Leyla. “The Trap of Wishcycling.” Disruptive Design. 8 Sep. 2021. Web. 22 Feb. 2022. <https://medium.com/disruptive-design/the-trap-of-wishcycling-6ea083646876>
29Siegel, Henry and Strain, Larry. “Embodied Carbon: What you Can Do Right Now.” AIA California. 5 March 2020. Web. 8 Feb. 2022. <https://aiacalifornia.org/embodied-carbon-definitions-and-facts/>
30Nadeeshani, Malka et al. “Carbon Footprint of Green Roofing: A Case Study from Sri Lankan Construction Industry.” Sustainability 2021, 13, 6745. 15 June 2021.
31Clancy, Heather. “Carbon-sucking concrete is capturing attention and funding.” GreenBiz. 6 May 2021. Web. 17 Feb. 2022. <https://www.greenbiz.com/article/carbon-sucking-concrete-capturing-attention-and-funding>
32PLC-Portland Limestone Cement. “Portland-Limestone Cement U.S. Fact Sheet.” Greener Cement. Web. 17 Feb. 2022. <https://www.greenercement.com/_files/ugd/f3d485_bf593dd744f049d98cbd293109fc42ce.pdf>
33Tosti, Lorenzo et al. “Technical and environmental performance of lower carbon footprint cement mortars containing biomass fly ash as a secondary cementitious material.” Resources, Conservation and Recycling. Volume 134. July 2018.<https://doi.org/10.1016/j.resconrec.2018.03.004>
34.Overbey, Daniel. “Defining a Whole-Building Embodied Carbon Workflow.” Building Enclosure. 30 June 2021. Web. 9 Feb. 2022. <https://www.buildingenclosureonline.com/blogs/14-the-be-blog/post/89961-defining-a-whole-building-embodied-carbon-workflow>
35Alter, Lloyd. “New Tool Calculates Full Life Cycle Carbon Emissions for Passive House.” Treehugger. 25 Jan 2022. Web. 9 Feb 2022. <https://www.treehugger.com/tool-lifecycle-carbon-emissions-passive-house-5216866>
36International Living Future Institute and Passive House Institute. “Zero Energy &
Passive House Certifications.” 2019. Web 22 Feb. 2022. <https://living-future.org/wp-content/uploads/2019/07/Zero_Energy_PassiveHouse_Crosswalk-1.pdf>
37Ibid.
38Resilient Design Institute. “What is Resilience?” Resilient Design. Web. 4 Feb. 2022. <https://www.resilientdesign.org/defining-resilient-design/>
39Roofing Contractors Association of British Columbia. “Template: ROOFTOP EQUIPMENT & WALKWAYS (BUR).” Web. 4 Feb. 2022. <https://rpm.rcabc.org/index.php/Template:ROOFTOP_EQUIPMENT_&_WALKWAYS_(BUR>
40Green Roofs for Healthy Cities. “About Green Roofs.” Greenroofs.org. Web 10 Feb. 2022. <https://greenroofs.org/about-green-roofs>
41Simon, Matt. “Your Rooftop Garden Could Be a Solar-Powered Working Farm.” “Wired,” 3 Dec. 2021. Web. 17 Feb. 2022. <https://www.wired.com/story/your-rooftop-garden-could-be-a-solar-powered-working-farm/>
42Urban Green Council and The Nature Conservancy. “NYC’S SUSTAINABLE
ROOF LAWS.” Urban Green Council. Dec. 2019. Web. 10 Feb. 2022. <https://www.urbangreencouncil.org/sites/default/files/sustainable_roof_laws_brief_final_12.11.19.pdf>
43Ibid.
44Javits Center. “Green Roof Tours.” Javits Center. Web 7 Feb. 2022. <https://javitscenter.com/sustainability/green-roof-tours/>
45Sokol, David. “Rooftop Farm Soars Above the City.” Architectural Record. 15 Dec. 2021. Web. 7 Feb. 2022. <https://www.architecturalrecord.com/articles/15429-rooftop-farm-soars-above-the-city>
46Designing Buildings. “Blue Roof.” 15 Dec. 2021. Web. 22 Feb. 2022. <https://www.designingbuildings.co.uk/wiki/Blue_roof>
47Livingroofs.org. “The blue green roof—helping cities cope with stormwater.” Web. 22 Feb. 2022. <https://livingroofs.org/introduction-types-green-roof/blue-green-roof-cities-stormwater/>
48SemperGreen USA. “Purple-Roof Case Study.” 12 Oct. 2021. Web. 22 Feb. 2022. <https://www.sempergreen.com/en/sempergreen-academy/webinar-innovation-for-future-proof-cities>
Veronika Chwieroth, a Senior Sales Design Specialist for GAF with expert regional insight for tapered insulation systems, and an alumna of Parsons School of Design.
Quiz
1. Sustainability is:
- A marketing strategy used by businesses to increase profits.
- A holistic strategy to meet the needs of the present without compromising the ability of future generations to meet their own needs.
- A political wedge used by politicians to get re-elected.
- A financial strategy to de-risk investments.
2. What does the International Panel on Climate Change conclude about climate change?
- Local weather is the same thing as global climate systems.
- The global warming data can be explained by an array of variables including technological advancements in modeling and monitoring, population growth, and natural phenomenon such as solar storms and volcanoes.
- There is plenty of time to debate whether climate change is happening or not.
- It is unequivocal that human influence has warmed the atmosphere, ocean and land. Widespread and rapid changes in the atmosphere, ocean, cryosphere and biosphere have occurred.
3. In U.S. cities, approximately what percentage of emissions come from buildings?
- 20 percent
- 50 percent
- 70 percent
- 100 percent
4. Net-zero operational carbon is:
- A highly energy-efficient building with all remaining energy from onsite and/or offsite renewable sources.
- A code-built building whose owner has purchased enough carbon offsets through tree plantings to claim net-zero energy status.
- A unicorn. There’s no such thing as net-zero energy buildings.
- A building that is highly efficient with upfront carbon minimized to the greatest extent possible and all remaining embodied carbon is reduced or, as a last resort, offset.
5. Net-zero embodied carbon is:
- A highly energy-efficient building with all remaining energy from onsite and/or offsite renewable sources.
- A building that is highly efficient with upfront carbon minimized to the greatest extent possible and all remaining embodied carbon is reduced or, as a last resort, offset.
- A unicorn. There’s no such thing as net-zero embodied carbon buildings.
- A building that is built only from natural materials that have been sourced locally using only manual labor or beasts of burden for transportation and construction.
6. Whole life carbon is:
- The total amount of carbon emissions released by disposing of a roof in a landfill.
- The total amount of carbon captured by planting trees to offset building material embodied carbon.
- An ancient industrial process that uses highly pressurized gases inside solidified carbonite to preserve biological organisms for intergalactic travel.
- The sum of operational carbon and embodied carbon.
7. Overburden is:
- Any manner of additional load on a roof from snow, severe hail, or wind.
- Any manner of material, equipment or installation that is situated on top of, and covering all or a portion of, a roof or waterproofing membrane assembly.
- Any manner of severe storm or “bomb cyclone” that floods sewer systems and impervious surfaces with rainwater.
- None of the above.
8. Roofs can significantly reduce the operational carbon of buildings by including:
- A thermal-bridge free roof assembly with the roof assembly seamlessly integrated into the vertical wall air barrier.
- Robust climate-specific levels of continuous insulation.
- Rooftop solar.
- All of the above
9. A purple roof refers to:
- The color of the roof membrane.
- The color of the cover board used on flat/low-slope roof.
- A roof that incorporates rainwater retention and detention with a sponge-like layer made of hydrophilic mineral wool to increase the volume of rainwater that can be retained or detained and reduces peak outflow by up to 95 percent.
- All of the above
10. In tropical climates, the lifecycle carbon emissions of a concrete roof can be reduced nearly 85 percent by:
- Adding fly ash to the concrete mix.
- Recycling the concrete at the end of its useful life.
- It can’t be done. Concrete and steel have too much embodied energy from their heavy manufacturing processes.
- A vegetated roof.