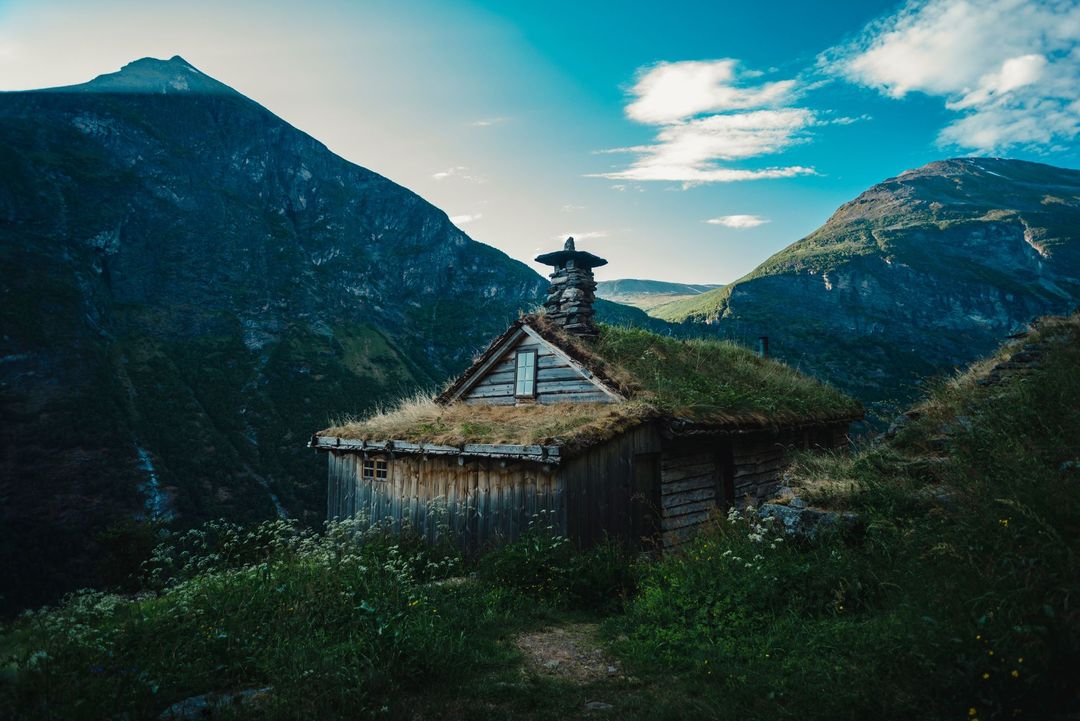
At Aquabella, most of the suites have balconies but several on the upper levels have terraces. All photos courtesy of Schöck North America; Michael Muraz.
Rising above Toronto’s Bayside community, a mixed-use neighbourhood on the shore of Lake Ontario, stands the 14-story Aquabella condominium development. The 290,626-square-foot, 174-suite concrete building is the third of four planned Bayside condominiums developed by real-estate firms Hines and Tridel.
The developers are aiming for LEED Platinum Certification, as well as compliance with Toronto Green Standard (TGS) requirements. In effect since 2010, the TGS sets tiered energy, emissions, and sustainability benchmarks for new buildings to support Toronto’s goal of reducing greenhouse gas emissions to net zero by 2050.
EQ Building Performance conducted energy modeling studies of the design, verifying that the building meets its Energy Use Intensity (EUI) efficiency target of 17 ekWh/square-foot per year (equivalent kilowatt hours per square meter), and thus meets the requirements of TGS Version 2 and the 2017 Ontario Building Code.
Hines and Tridel state that Aquabella was designed to be at least 35 percent more energy-efficient than a similar structure designed to the National Energy Code for Buildings (NECB), a Canadian government standard.
The Toronto Green Standard
The Toronto Green Standard (TGS) first came into effect in 2010. Version 3, which was initiated May 1, 2018, introduced thermal bridging criteria. Developers were told to calculate heat loss from balcony slabs and other building envelope penetrations to meet targets set by TGS. Version 4 of the TGS was approved by Toronto City Council on July 15, 2021 and applies to new building applications as of May 2022.
“The City of Toronto, with the Toronto Green Standard, lays out a good road map for minimum performance requirements for developments,” says Graeme Armster, P.Eng., Director of Innovation and Sustainability at Deltera, the construction management division of Tridel. “Balcony thermal breaks are starting to pick up steam because developers are starting to see the value. We’re projecting that thermal breaks will soon become a minimum requirement in newer iterations of the Toronto Green Standard.”
Visually Striking, Environmentally Friendly
The northwest corner of the L-shaped structure marks the tallest portion of the residence, which slopes downward toward its center, and then rises in height on the eastern flank. The condo tower offers stepped, upper-level garden terraces with scenic views of Toronto and Lake Ontario, a fitness studio, movie theatre, underground parking, and ground-level retail.
To achieve the required energy targets, the Aquabella project team pursued active strategies in the form of efficient mechanical systems, and passive strategies that impact building performance such as building orientation, building envelope materials, windows and daylighting, and natural ventilation.
Aquabella employs an electric-powered Variable Refrigerant Flow (VRF) heating/cooling system with built-in heat recovery. Each suite includes an Energy Recovery Ventilator (ERV), high-efficiency appliances and pumps, and low-flow water fixtures, among other LEED Platinum and TGS approved features.
A high-performance building envelope was desired to passively reduce cooling and heating energy use and resulting utility costs. The project team aimed for one-third of the insulation on the exterior and two-thirds on the interior, states Carlos Antunes, Partner at Kirkor Architects and Planners. Wall assemblies are comprised of 2 inches of semi-rigid insulation and 6 inches of thermal batt insulation. Window wall systems are comprised of double-glazing and have low-e (emissivity) coating to improve the insulating properties of the glass.
Exterior of the completed Aquabella condominiums depict layered architectural design and extensive balconies which are insulated with Isokorb® structural thermal breaks.
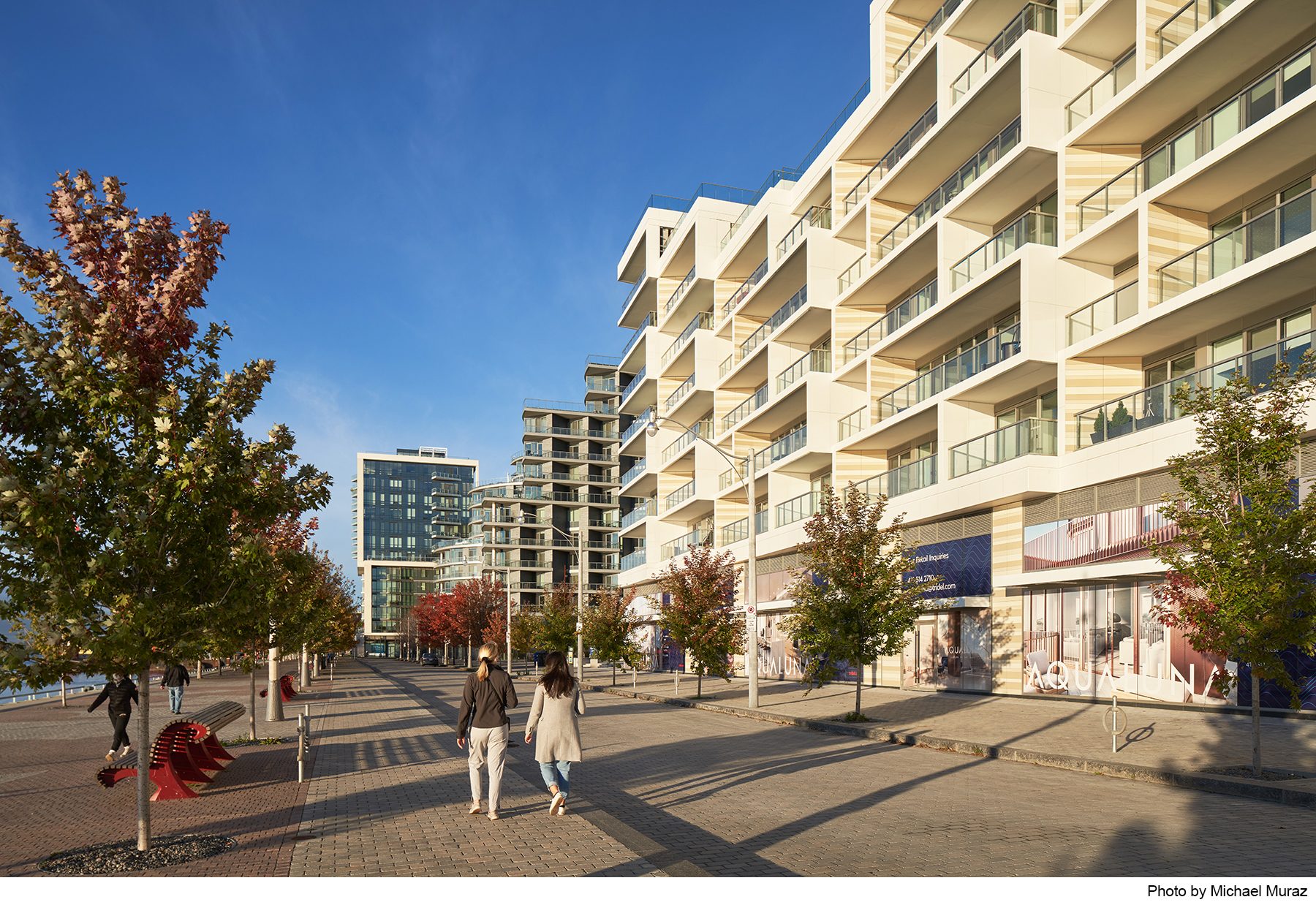
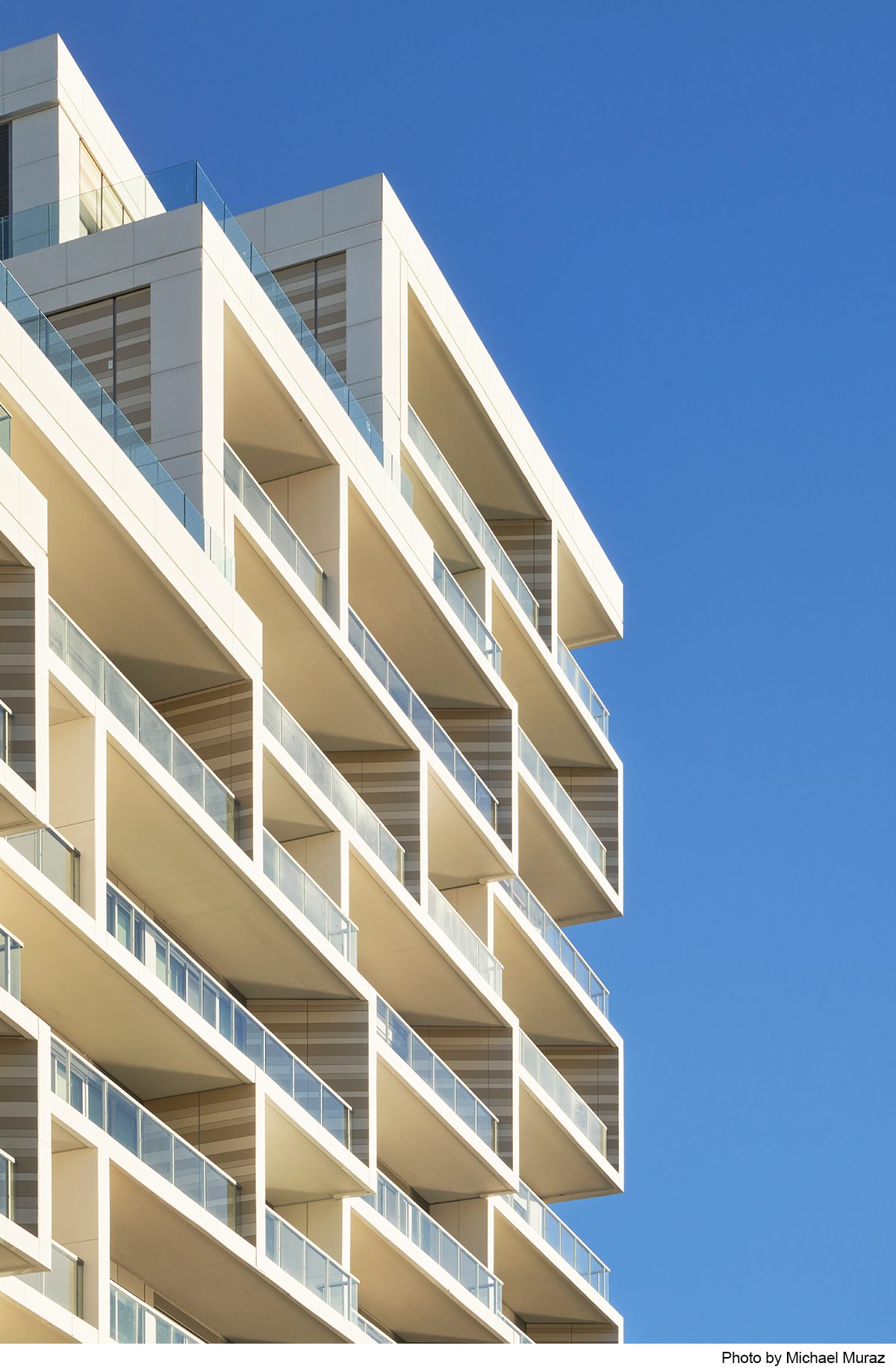
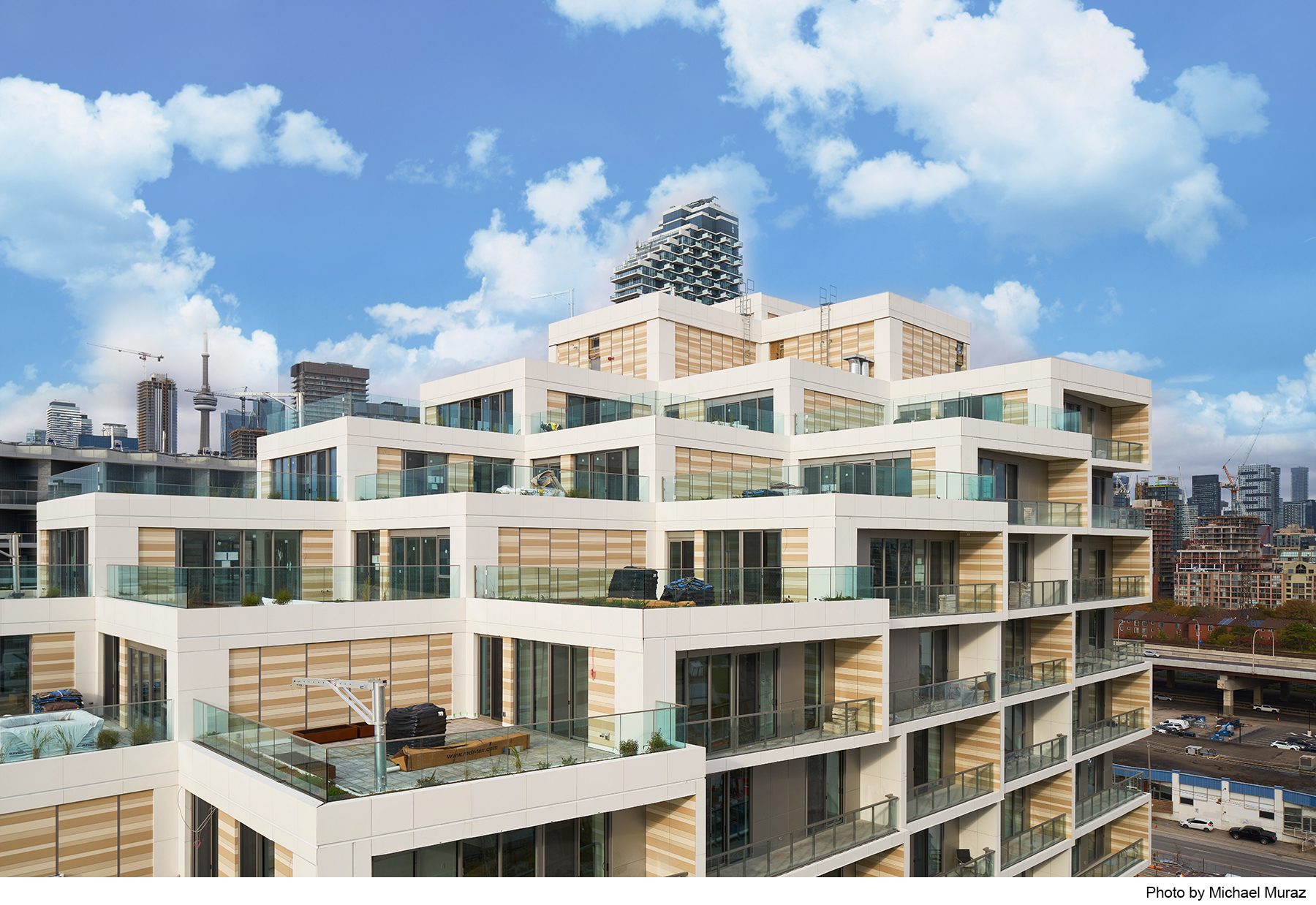
Thermal Bridging Mitigated at More Than a Mile of Balconies
Eighty percent of Aquabella's 174 suites have balconies, creating the potential for heat energy loss through thermal bridging. Thermal bridges also allow cold surfaces in the interior space, negatively impacting occupant comfort and often resulting in condensation and mold issues.
To minimize thermal bridging at balconies and maintain a continuous insulated building envelope, structural thermal breaks are installed at the building envelope between balconies and the interior floor slabs.
Structural thermal breaks consist of an insulation module with stainless steel rebar running through the insulation for structural strength. The module's expanded foam is approximately 98 percent less conductive than concrete, while its stainless steel rebar is approximately one-third as conductive as carbon steel rebar, reducing heat loss at balcony penetrations by up to 90 percent, while preventing interior condensation and mould growth.
Isokorb® concrete-to-concrete structural thermal breaks provide structural support and insulation to minimize heat transfer through thermal bridges penetrating the building envelope. Tension and shear bars running through the insulation block tie into the steel reinforcement bars of the building’s interior slab and cantilevered exterior penetrations.
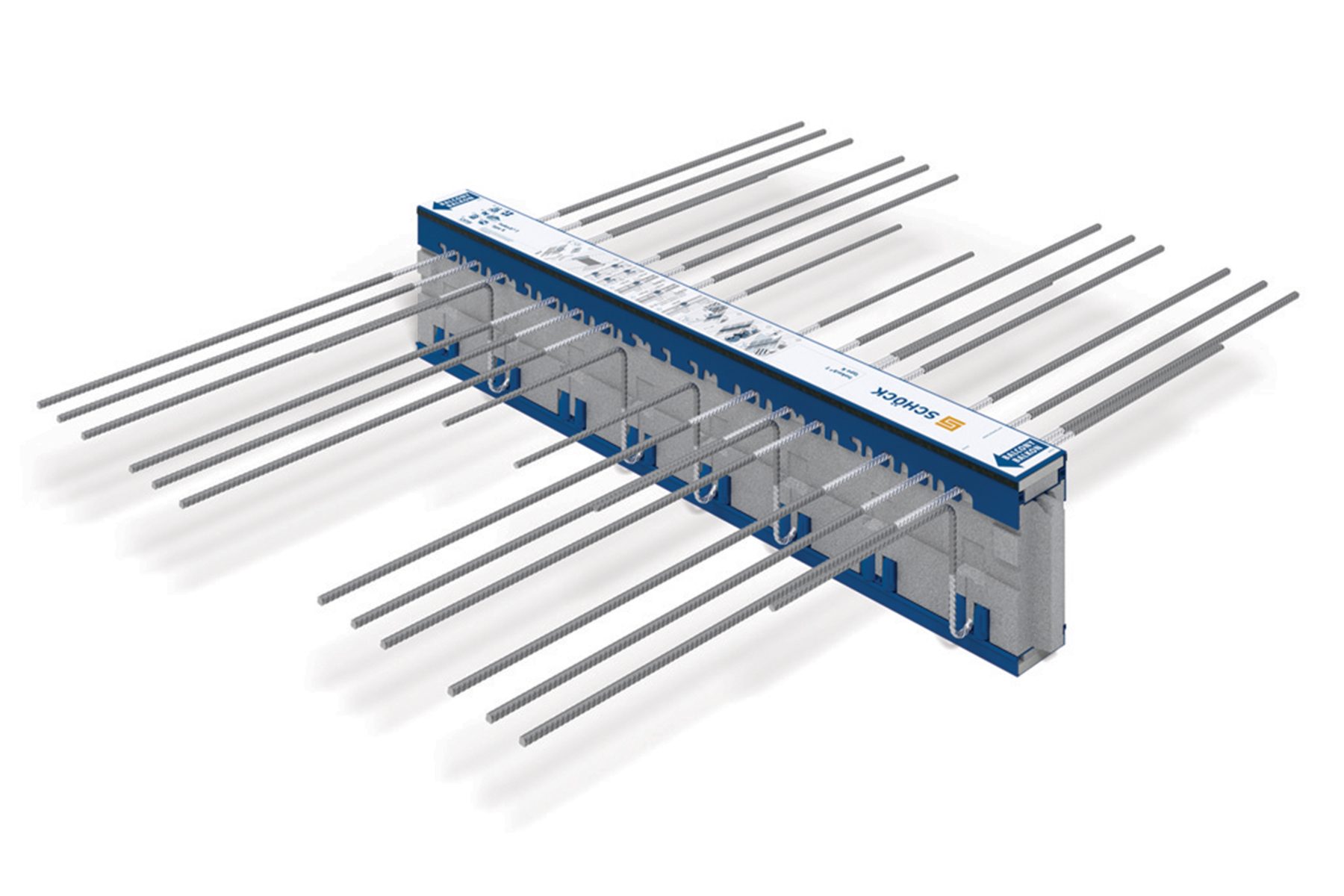
Installing Structural Thermal Breaks at Balconies
A total of 3,500 linear feet of concrete-to-concrete thermal breaks were fitted on Aquabella balconies.
Isokorb® concrete-to-concrete structural thermal breaks are manufactured in 3.3-foot lengths and can be cut on-site to fit design conditions, ensuring easy handling and placement during installation. For installation in cast-in-place concrete, the thermal breaks are positioned between the rebar cages of the exterior balcony and the interior floor slab. Then, the steel reinforcement of the structural thermal break is tied off to the rebar cages to secure the thermal break in place. Finally, both the interior and exterior slabs are poured through.
Installation “went very smoothly,” reported Babak Baradaran-Seyed, Structural Engineer at Stephenson Engineering. The building itself was completed in mid-2021, with occupancy soon following.
Most balconies feature sliding glass doors, which “posed no issues” in terms of installing the structural thermal breaks, says Howard Tuchman, Architect/Senior Associate at Kirkor Architects and Planners, adding that the developers do not anticipate thermal bridging issues at balconies. “By putting in the thermal breaks, we reduce thermal bridging and almost eliminate cold floors near the balconies, which is a common complaint.”
Underside of structural thermal breaks (blue) shown between the balcony and interior slabs.
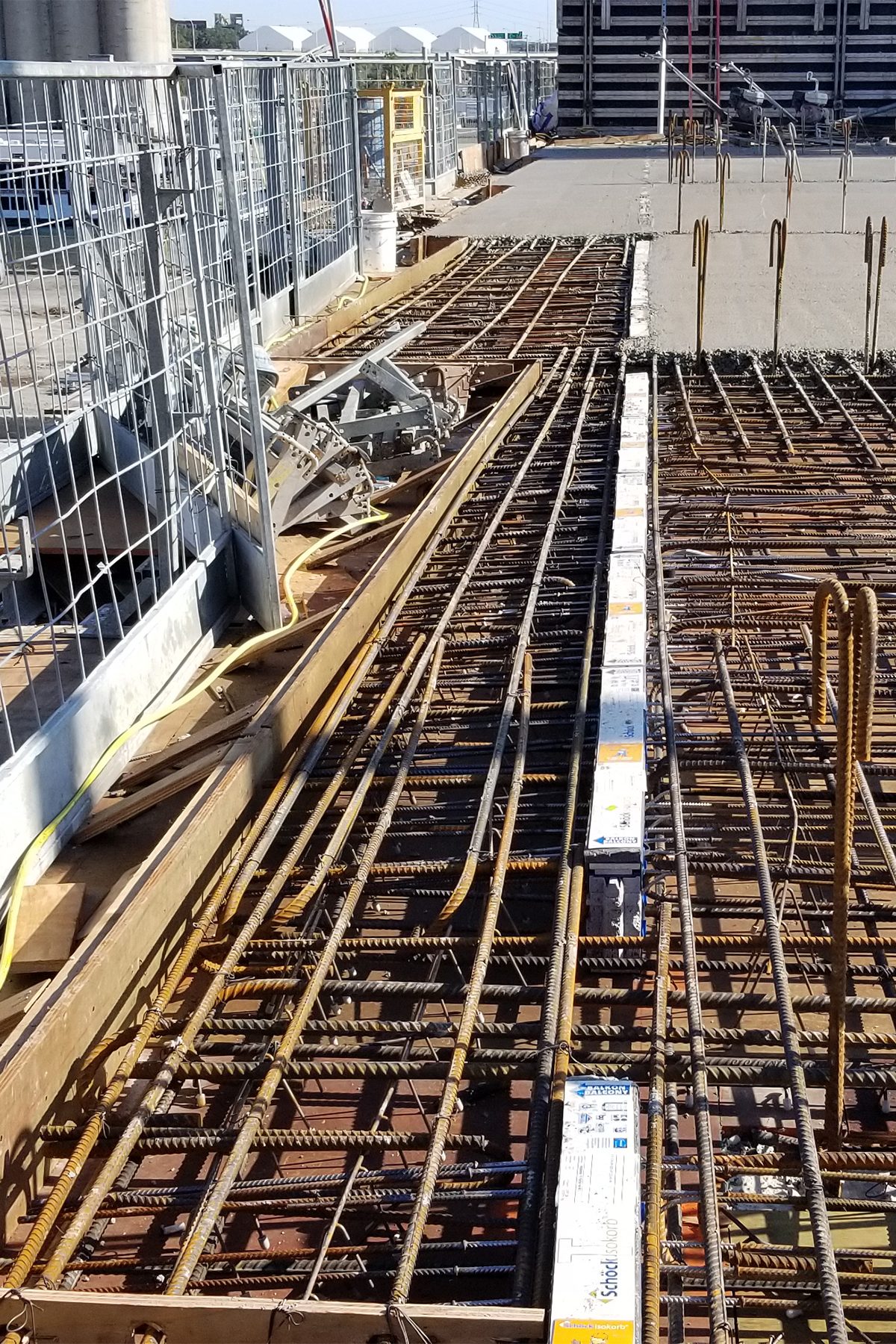
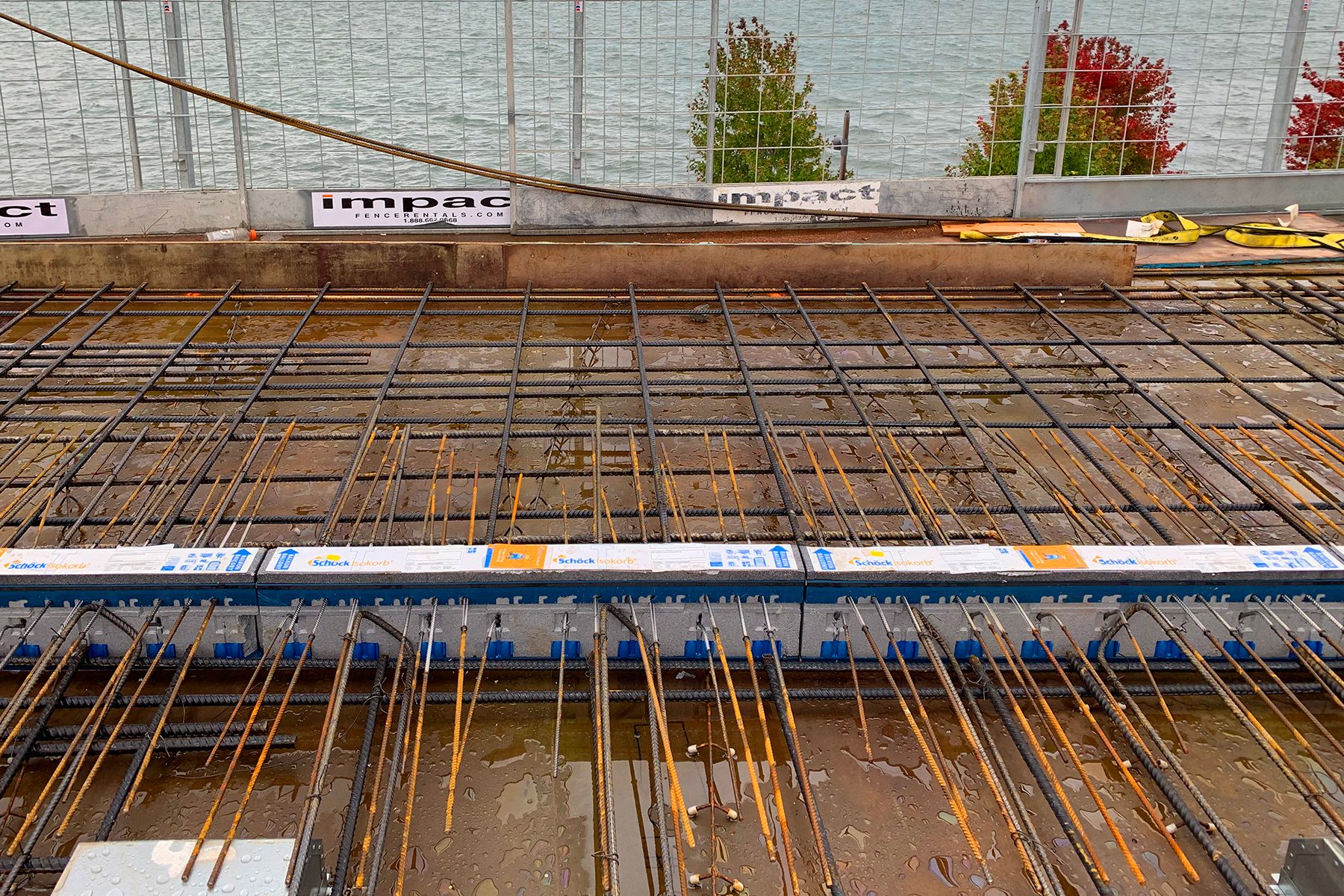
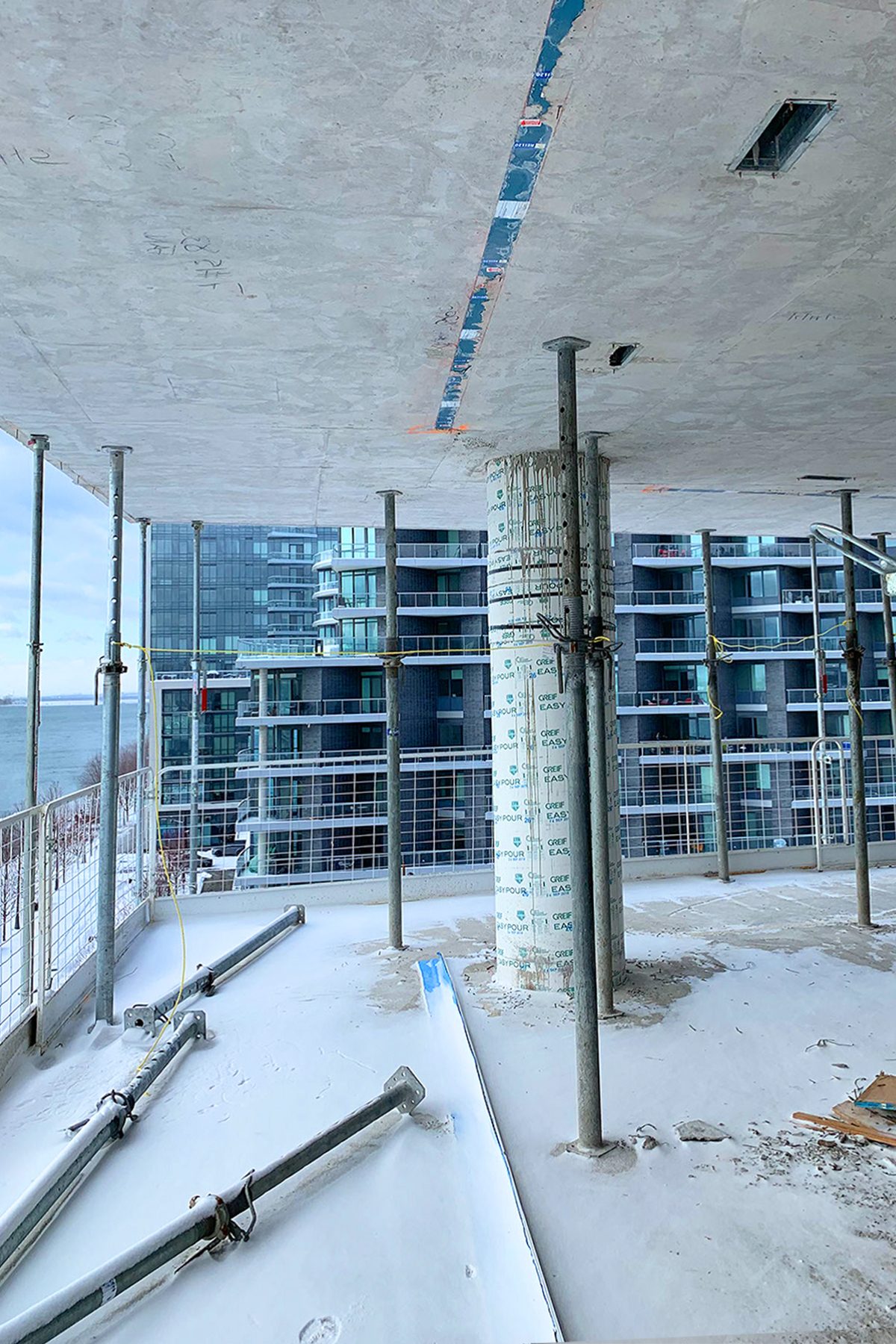