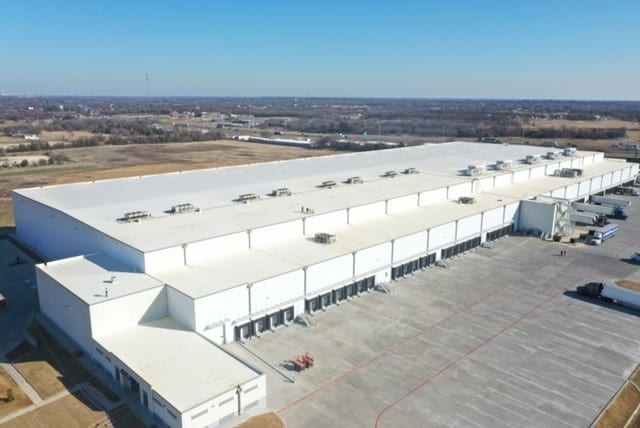
High-Performance Cold Storage Roof Design
Cold storage facilities are exceptional structures that experience exceptional extremes. Due to their distinctive nature, cold storage buildings require unique construction assemblies, including roof assemblies. All images courtesy of GAF, unless otherwise noted.
CE ARTICLE

By Kristin M. Westover, PE, LEED AP O+M
AIA Course: #BE2023GAF1
Earn: 1 AIA LU/HSW; 1 IIBEC CEH; 0.1 IACET CEU
To complete the quiz and receive a certificate of completion, follow this link: ce.buildingenclosureonline.com/BE2023GAF1
Sponsored by:
Learning Objectives:
After reading this article, you should be able to:
- Review the importance of air, vapor, and thermal control layer continuity.
- Evaluate how cold storage roof design can impact building energy use and operations.
- Assess typical cold storage details to appraise control layer continuity.
- Examine common installation and detailing errors during construction and how they impact roof functionality.

Section 1: Defining Cold Storage Buildings
Cold storage refers to a building or portion of a building designed to promote extended shelf life for products or commodities. Cold storage buildings can house various industries including food processing plants, pharmaceutical manufacturing facilities, and holding facilities for dry, refrigerated, and frozen goods. Typically, these structures have year-round temperatures below 50 degrees Fahrenheit (10 degrees Celsius). There are varying levels of cold storage, such as coolers, chill coolers, holding freezers, and blast freezers. Coolers range from approximately 32–55F (0–13C), while, at the other extreme, blast freezers can have interior temperatures from minus 20–50F (minus 29–46C)
Cold storage buildings are exceptional structures because they experience extremes in both internal temperature and humidity compared to typical buildings. Due to their distinctive nature, cold storage buildings require unique construction assemblies, including roof assemblies.
The marked difference in vapor pressure between the building interior and the exterior can cause a pronounced vapor drive through the roof assembly. When warm humid air that infiltrates into the roof assembly there can be extreme consequences including significant build-up of condensation within the roof assembly, or even inside the building, if the roofing system is not properly designed and installed. These factors can lead to severe deterioration of both the roof assembly itself and interior components, as well as damage to stored goods and health and safety concerns for employees.
It is both the challenge and the responsibility of the design professional to correctly specify the cold storage building type and its roofing system. Careful selection of primary control layers of water, air, thermal, and vapor, and design of their continuity will aid the roof in its role of reducing the risk of condensation. High-performance roof design is essential to operations efficiency and decreased energy use of the cold storage facility.
Section 2: Cold Storage and Building & Roofing Science
Temperature and thermodynamics. Relative moisture risks. Vapor control materials. Air transport and air leakage. All of these elements are inputs into the equation of a high performance roof. Failing to plan for even one of these, or planning incorrectly, frequently results in energy loss and inefficient operations. This is especially true for a cold storage facility.
Why is a cold storage building so different? Cold storage is not a typical building simply because of its temperature, but due to the temperature differential between the interior and the exterior, and the resulting vapor drive from the exterior to the interior is significant. Because cold storage buildings are maintained at temperatures that are often much lower than the exterior temperature, the warm, moist, outside air wants to move to the interior of the building to achieve equilibrium. The direction of the vapor drive is predominantly from the exterior to the interior for most times of the year since in most climates the interior will be colder than the exterior.
While a concern is the vapor drive that occurs from the warmer exterior toward the colder interior, air infiltration into the interior of the cold storage building is a greater concern and can have detrimental effects to the roof assembly. Combating this requires two critical measures in the roof design: first, proper placement of a vapor retarding material to manage the vapor drive and second, proper detailing to prevent air infiltration at enclosure transitions and penetrations.
Condensation control
A common way to control or minimize condensation problems in a roofing assembly is to use a vapor retarder. Vapor retarders help reduce vapor diffusion into a roof system. The most common uses of vapor retarders occur in buildings located in colder climates, over concrete decks, and for buildings with high interior humidity levels, such as swimming pools, museums, and data centers. In these scenarios, the most effective location for a vapor retarder is directly above the roof deck and below the roof insulation layer, or in some cases, directly above a rigid board, like gypsum board, that is secured to the roof deck. The vapor retarder restricts moisture from the building interior into the roof assembly. This location of the vapor retarder is installed on the warm side (in winter) of the insulation.
Although the same principle applies for cold storage buildings, because the vapor drive is generally from the warm to cold, the vapor retarder is located on the exterior side of the insulation. This is generally true for most geographical locations in the U.S. for most months of the year; the interior is most often colder than the exterior of the building. Most commonly, the roof membrane serves as the vapor retarder; using the roof membrane as the vapor retarder places unique needs on any membrane selected.
In a typical cold storage configuration, the roofing membrane will act as both the vapor retarder and air barrier, keeping both vapor and air from getting into the roof system. However, successful installation and detailing are key to prevent air and vapor intrusion into the building interior and roof assembly. If heat and moisture reach a cold surface, this can create condensation. When condensation reaches the insulation, the insulation’s performance is reduced, which includes a reduction of R-value and equates to energy loss within the building. Condensation can also occur at building interiors such as at the underside of roof decks or on storage floors, which can impede interior operations.
Ice formation on the underside of the roof deck.
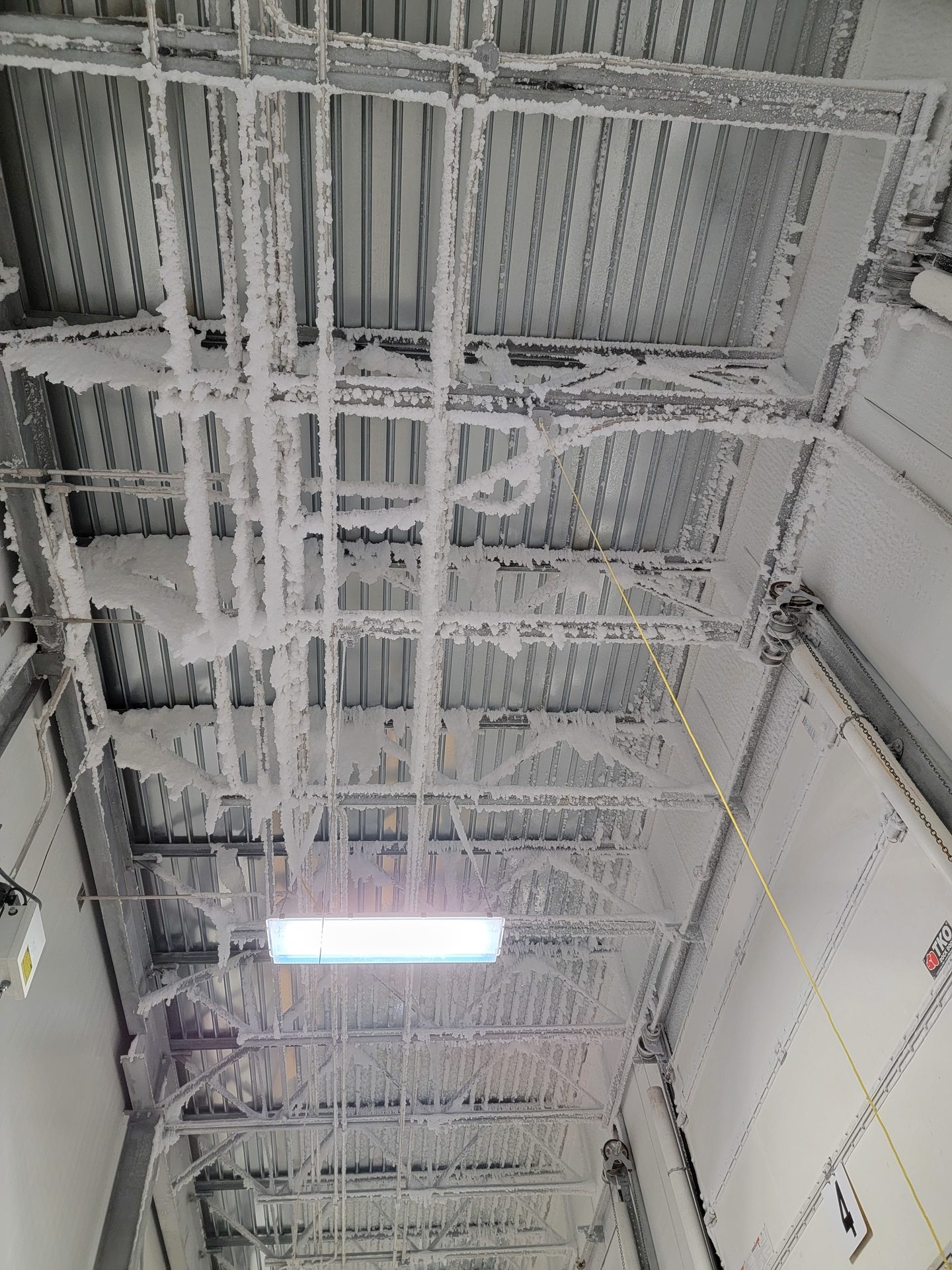
Photo 1
Fundamentals of moisture control
One of the primary purposes of a building envelope is to keep moisture out of a building. What makes this seemingly simple goal a challenge is that moisture comes in many forms and can take many paths into a building. Building designers need to account for bulk water, air-transported moisture, and water vapor, and defend against each of these in different ways.
Bulk water
Bulk water, such as rain and snow, is kept out of buildings with roof membranes and wall cladding systems. Roofs were first created for this purpose, and keeping out bulk water consists of watertight detailing that is typical for any roof assembly. Cold storage detailing requires augmenting of typical roof details to include air tightness in conjunction with water tightness.
Air-transported moisture
Air-transported moisture, as the name implies, is carried into or out of a building by air that infiltrates or passes through the building envelope. In a warm climate, air transports up to 10 times more water than diffusion, and in a cold climate, air transports up to 100 times more water than diffusion. To complicate this, there are several types of air transportation that can occur through the building envelope. Air infiltration is where exterior air enters into the building through gaps in the exterior enclosure. In cold storage, this can be problematic since most often the exterior air is warmer and more humid than the interior, which can lead to condensation when the warm air meets a cold surface.
Exfiltration is where interior air exits from the building, also through gaps and inconsistencies in the building exterior. Exfiltration can lead to the cooling systems having to work harder to maintain interior temperatures, which ultimately leads to higher energy bills. Intrusion is air that enters a roof or wall system but does not exit to the exterior; an air barrier prevents the passage of air through the entire building enclosure. Since air that enters from the exterior often contains moisture, condensation is likely to form as a result, often forming within the roof assembly. Condensation within the roofing assembly is not likely to evaporate, and instead this can lead to frozen insulation and roofing components. This is why air-transported moisture is much more critical to prevent than water vapor that enters a building by diffusion; condensation is likely to occur at any time there is uncontrolled air movement.
Air transportation.
Figure 1
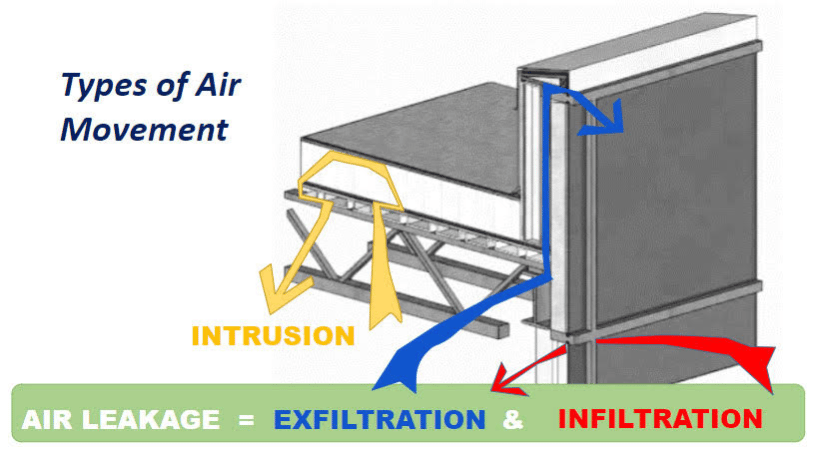
Vapor drive
Cold storage buildings are commonly maintained year-round at temperatures that are, in most geographical areas and for most of the year, considerably lower than the exterior temperature. For cold storage buildings, the warm, moist outside air wants to move inward. This means the direction of the vapor drive experienced by a cold storage structure is opposite that of a conventional building—from the exterior to the interior. Therefore, the importance of a continuous vapor retarder from on the exterior of the building, such as the roof membrane, is critical to inhibit vapor diffusion.
Air leakage versus vapor diffusion
Because of the comparative amount of moisture transported during each process, air-transported moisture is a larger issue than vapor diffusion. The National Research Council Canada collected research data that illustrated how even small openings can dramatically affect overall air leakage performance.1 For example, air can transport up to 100 times more moisture than the process of diffusion. This illustrates the greater impact that air leakage can have over moisture accumulation from vapor diffusion, which can have a significant negative impact on cold storage facilities. Air leakage can form ice or icicles on the underside of roof decks or within the roofing assembly, all of which impact the energy use and operations within the cold storage facility.
Relative moisture risks.
Figure 2
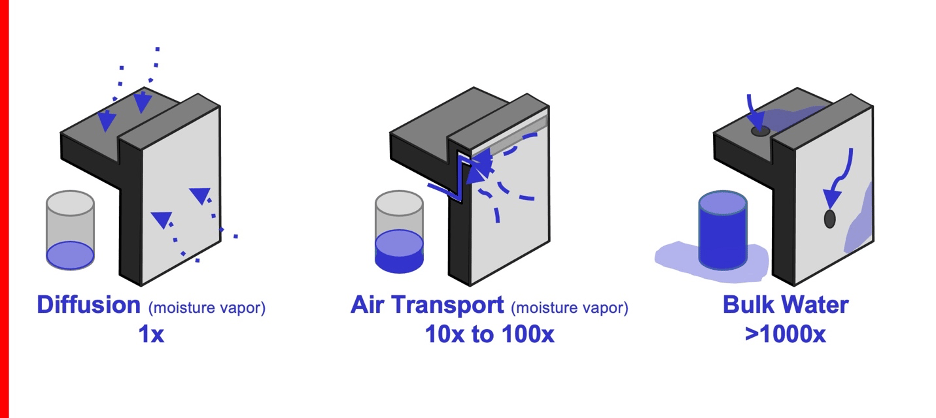
Most commonly in cold storage structures, the roof membrane serves as the vapor retarder and the air barrier. Accordingly, it is critical that the membrane be continuous, with no gaps or holes. The membrane should be designed and installed to block the passage of air by detailing all laps, penetrations, and the roof-to-wall interfaces. Any discontinuities within the assembly will lead to condensation within the roof assembly or at the interior of the cold storage facility.
Section 3: Cold Storage Design
There are many factors that may affect roof design, including specific jobsite conditions, local building codes, and building use, all of which must be taken into account to achieve desired energy savings and efficient operations. Due to the nature of cold storage buildings and the need to maintain specific interior temperatures, designing the best roofing system for the building becomes more than material selection. Proper design and installation will impact the functionality of the roof assembly for the life of the roof, which could be 20 years or more.
Cold Storage—General design considerations
Proper roofing system design and selection involves careful consideration of factors specific to cold storage. These help to provide a fundamentally sound basis for design and selection. First, verify during design that proposed materials are compatible with each other and that they will achieve the end goals of the project, such as energy efficiency and mitigation of air movement.
Diagram of a cricket and common terminology.
Figure 4
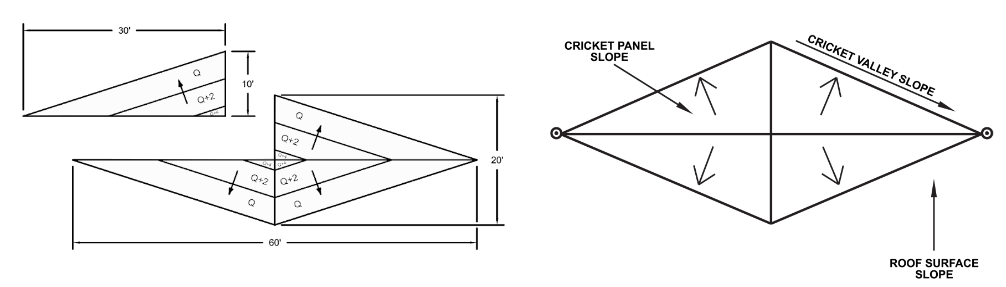
Undersized crickets that leave standing water and accumulated dirt because they are inefficient for their application.
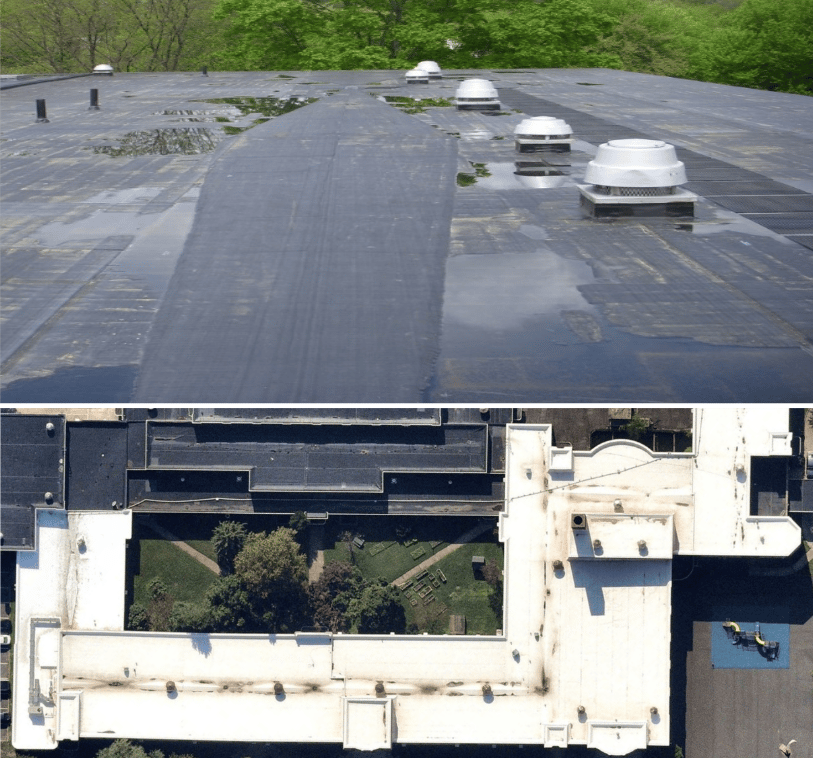
Figure 5
To help visualize these cricket issues, an image of a cricket is provided that has been reduced in size so drastically that it does not resemble a cricket nor function as it needs to. The cricket valley slope in this example is close to 0 inches per foot, evident by the standing water seen on the roof. Undersized crickets do not divert water quick enough to the drains and allow dirt to gather, encouraging algae and bacteria growth. While membrane manufacturers may allow for a ponding exclusion in their material warranties because they believe the membrane will stand the test of time, allowing for undersized crickets can prematurely shorten the service life of the membrane and not only cause performance issues, but aesthetic issues as well if lower levels with collected dirt can be seen from above.
References
1. May 2011. Impact of Air Leakage on Hygrothermal and Energy Performance of Buildings in North America. National Research Council of Canada. NRC Institute for Research in Construction. 13th Canadian Conference on Building Science and Technology. 1-2. NRC-IRC-21657. https://nrc-publications.canada.ca/eng/view/object/?id=4669310e-0f32-45ed-b393-21318c023789.
End Notes
1Architecture 2030. “Accelerating to Zero by 2040!” Oct. 2019. Web. 22 Feb. 2022. <https://architecture2030.org/accelerating-to-zero-by-2040/ >
2https://www.un.org/en/academic-impact/sustainability Accessed 2/4/2022 at 9:33am.
3Intergovernmental Panel on Climate Change. “Climate Change 2021: The Physical Science Basis Working Group I: Contribution to the Sixth Assessment Report of the Intergovernmental Panel on Climate Change.” Oct. 2021. Web. 4 Feb. 2022. <https://www.ipcc.ch/report/ar6/wg1/downloads/report/IPCC_AR6_WGI_SPM_final.pdf>
4National Oceanic and Atmospheric Administration (NOAA). “2021 U.S. billion-dollar weather and climate disasters in historical context.” 24 Jan. 2022. Web. 6 Feb 2022.
5Intergovernmental Panel on Climate Change. “Climate Change 2021: The Physical Science Basis Working Group I: Contribution to the Sixth Assessment Report of the Intergovernmental Panel on Climate Change.” Oct. 2021. Web. 4 Feb. 2022. <https://www.ipcc.ch/report/ar6/wg1/downloads/report/IPCC_AR6_WGI_SPM_final.pdf>
6Headline Statements. Intergovernmental Panel on Climate Change. Web. 8 Feb. 2022. <https://www.ipcc.ch/sr15/resources/headline-statements/>
7Architect Magazine Staff and Mazria, Edward. “Architecture 2030's Open Letter to the UN Framework Convention on Climate Change Calls for Revised Carbon Emission Reduction Targets.” Architect Magazine, 6 Nov. 2020. Web. 18 Feb. 2022. <https://www.architectmagazine.com/technology/architecture-2030s-open-letter-to-the-un-framework-convention-on-climate-change-calls-for-revised-carbon-emission-reduction-targets_o>
8Pedersen, Martin C. “Edward Mazria With Some Good News About Combating Climate Change.” “Common Edge,” 27 July 2020. Web. 9 Feb. 2022. <https://commonedge.org/edward-mazria-with-some-good-news-about-combating-climate-change/>
9Carbon Leadership Forum. “Embodied Carbon 101.” 17 Dec. 2020. Web. 8 Feb. 2022. <https://carbonleadershipforum.org/embodied-carbon-101>
10NYC Mayor’s Office of Climate & Environmental Justice. “Energy Benchmarking:
Energy map.” New York City Energy & Water Performance Map.” Web. 8 Feb. 2022. <https://www1.nyc.gov/site/sustainability/codes/energy-benchmarking.page#:~:text=Over 70 percent of New,on energy and water management>
11Center for Sustainable Systems, University of Michigan. 2021. "U.S. Cities Factsheet." Pub. No. CSS09-06. Web. 8 Feb 2022. <https://css.umich.edu/factsheets/us-cities-factsheet#:~:text=It is estimated that 83,to live in urban areas>
12Saulsbery, Gabrielle. “Peak Demand: Parsippany-based GAF addresses a serious labor shortage by training new roofers.” NJBiz. 17 May 2021. Web. 17 Feb. 2022. <https://njbiz.com/peak-demand-gaf-roofer-training/>
13La Rocca, Melanie E. “Service Notice: Local Law 92 of 2019 and Local Law 94 of 2019: Green and Solar Roof Requirements for New Buildings and Complete Roof Replacements.” NYC.gov. Oct. 2019. Web. Feb 9 2022. <https://www1.nyc.gov/assets/buildings/pdf/green_roof_solar_ll92-n-94of2019_sn.pdf>
14Urban Green Council and The Nature Conservancy. “NYC’S SUSTAINABLE
ROOF LAWS.” Urban Green Council. Dec. 2019. Web. 10 Feb. 2022. <https://www.urbangreencouncil.org/sites/default/files/sustainable_roof_laws_brief_final_12.11.19.pdf>
15Torgelson, Nathan. “Seattle Green Factor.” Seattle.gov. Web. 18 Feb. 2022. <https://www.seattle.gov/sdci/codes/codes-we-enforce-(a-z)/seattle-green-factor#:~:text=You can choose from a,or create a food garden>
16Seattle Department of Construction & Inspections. “Renewable Energy and Solar-Ready Roofs for Commercial Buildings.” Seattle.gov. 18 Oct 2021. Web. 14 Feb 2022. <http://www.seattle.gov/DPD/Publications/CAM/Tip422.pdf>
17Washington, D.C. Department of Energy & Environment. “Green Roofs in the District of Columbia.” Web. 22 Feb. 2022. <https://doee.dc.gov/greenroofs>
18Washington, D.C. Department of Energy & Environment. “Solar Initiatives.” Web. 22 Feb. 2022.
19World Green Building Council. “Whole Life Carbon Vision.” WorldGBC.org. Web. 4 Feb. 2022. <https://www.worldgbc.org/advancing-net-zero/whole-life-carbon-vision>
20Tobias, Michael. “Green Building Trends: Pros & Cons of Passive House Construction.” NewYork Engineers. 12 October 2021. Web. 17 Feb. 2022. <https://www.ny-engineers.com/blog/green-building-trends-pros-cons-of-passive-house-construction>
21Taylor, T.J. “Eliminating Fastener Thermal Bridging in Low Slope Roofs: Energy Efficiency Savings versus Installation Costs.” Open Journal of Energy Efficiency. 9, 94-110. June 2022. Web. 20 Feb. 2022. < https://doi.org/10.4236/ojee.2020.92007>
22Ibid.
23World Green Building Council. “Whole Life Carbon Vision.” WorldGBC.org. Web. 4 Feb. 2022. <https://www.worldgbc.org/advancing-net-zero/whole-life-carbon-vision>
24Ellen MacArthur Foundation. “What is a circular economy?” Web. 17 Feb 2022. <https://ellenmacarthurfoundation.org/topics/circular-economy-introduction/overview>
25Reuters. “U.S. corn-based ethanol worse for the climate than gasoline, study finds.” Autoblog. 21 Feb. 2022. Web. 2 Feb 2022.
26GAF Roof Views. “Welcome to the Future of Asphalt Recycling.” GAF.com. 21 April 2021. Web. 17 Feb 2022. <https://www.gaf.com/en-us/blog/welcome-to-the-future-of-asphalt-recycling-281474980090173>
27MYCOCYCLE. Web. 22 Feb 2022. <https://mycocycle.com/>
28Acaroglu, Leyla. “The Trap of Wishcycling.” Disruptive Design. 8 Sep. 2021. Web. 22 Feb. 2022. <https://medium.com/disruptive-design/the-trap-of-wishcycling-6ea083646876>
29Siegel, Henry and Strain, Larry. “Embodied Carbon: What you Can Do Right Now.” AIA California. 5 March 2020. Web. 8 Feb. 2022. <https://aiacalifornia.org/embodied-carbon-definitions-and-facts/>
30Nadeeshani, Malka et al. “Carbon Footprint of Green Roofing: A Case Study from Sri Lankan Construction Industry.” Sustainability 2021, 13, 6745. 15 June 2021.
31Clancy, Heather. “Carbon-sucking concrete is capturing attention and funding.” GreenBiz. 6 May 2021. Web. 17 Feb. 2022. <https://www.greenbiz.com/article/carbon-sucking-concrete-capturing-attention-and-funding>
32PLC-Portland Limestone Cement. “Portland-Limestone Cement U.S. Fact Sheet.” Greener Cement. Web. 17 Feb. 2022. <https://www.greenercement.com/_files/ugd/f3d485_bf593dd744f049d98cbd293109fc42ce.pdf>
33Tosti, Lorenzo et al. “Technical and environmental performance of lower carbon footprint cement mortars containing biomass fly ash as a secondary cementitious material.” Resources, Conservation and Recycling. Volume 134. July 2018.<https://doi.org/10.1016/j.resconrec.2018.03.004>
34.Overbey, Daniel. “Defining a Whole-Building Embodied Carbon Workflow.” Building Enclosure. 30 June 2021. Web. 9 Feb. 2022. <https://www.buildingenclosureonline.com/blogs/14-the-be-blog/post/89961-defining-a-whole-building-embodied-carbon-workflow>
35Alter, Lloyd. “New Tool Calculates Full Life Cycle Carbon Emissions for Passive House.” Treehugger. 25 Jan 2022. Web. 9 Feb 2022. <https://www.treehugger.com/tool-lifecycle-carbon-emissions-passive-house-5216866>
36International Living Future Institute and Passive House Institute. “Zero Energy &
Passive House Certifications.” 2019. Web 22 Feb. 2022. <https://living-future.org/wp-content/uploads/2019/07/Zero_Energy_PassiveHouse_Crosswalk-1.pdf>
37Ibid.
38Resilient Design Institute. “What is Resilience?” Resilient Design. Web. 4 Feb. 2022. <https://www.resilientdesign.org/defining-resilient-design/>
39Roofing Contractors Association of British Columbia. “Template: ROOFTOP EQUIPMENT & WALKWAYS (BUR).” Web. 4 Feb. 2022. <https://rpm.rcabc.org/index.php/Template:ROOFTOP_EQUIPMENT_&_WALKWAYS_(BUR>
40Green Roofs for Healthy Cities. “About Green Roofs.” Greenroofs.org. Web 10 Feb. 2022. <https://greenroofs.org/about-green-roofs>
41Simon, Matt. “Your Rooftop Garden Could Be a Solar-Powered Working Farm.” “Wired,” 3 Dec. 2021. Web. 17 Feb. 2022. <https://www.wired.com/story/your-rooftop-garden-could-be-a-solar-powered-working-farm/>
42Urban Green Council and The Nature Conservancy. “NYC’S SUSTAINABLE
ROOF LAWS.” Urban Green Council. Dec. 2019. Web. 10 Feb. 2022. <https://www.urbangreencouncil.org/sites/default/files/sustainable_roof_laws_brief_final_12.11.19.pdf>
43Ibid.
44Javits Center. “Green Roof Tours.” Javits Center. Web 7 Feb. 2022. <https://javitscenter.com/sustainability/green-roof-tours/>
45Sokol, David. “Rooftop Farm Soars Above the City.” Architectural Record. 15 Dec. 2021. Web. 7 Feb. 2022. <https://www.architecturalrecord.com/articles/15429-rooftop-farm-soars-above-the-city>
46Designing Buildings. “Blue Roof.” 15 Dec. 2021. Web. 22 Feb. 2022. <https://www.designingbuildings.co.uk/wiki/Blue_roof>
47Livingroofs.org. “The blue green roof—helping cities cope with stormwater.” Web. 22 Feb. 2022. <https://livingroofs.org/introduction-types-green-roof/blue-green-roof-cities-stormwater/>
48SemperGreen USA. “Purple-Roof Case Study.” 12 Oct. 2021. Web. 22 Feb. 2022. <https://www.sempergreen.com/en/sempergreen-academy/webinar-innovation-for-future-proof-cities>
Kristin M. Westover, PE, LEED AP O+M, is a Technical Manager of Specialty Installations for low-slope commercial roofing systems at GAF. She specializes in cold storage roofing assemblies where she provides insight, education, and best practices as it relates to cold storage roofing. Kristin is part of the Building and Roofing Science Team where she works with designers on all types of low-slope roofing projects to review project design considerations so designers can make informed roof assembly decisions..
Quiz
1. Sustainability is:
- A marketing strategy used by businesses to increase profits.
- A holistic strategy to meet the needs of the present without compromising the ability of future generations to meet their own needs.
- A political wedge used by politicians to get re-elected.
- A financial strategy to de-risk investments.
2. What does the International Panel on Climate Change conclude about climate change?
- Local weather is the same thing as global climate systems.
- The global warming data can be explained by an array of variables including technological advancements in modeling and monitoring, population growth, and natural phenomenon such as solar storms and volcanoes.
- There is plenty of time to debate whether climate change is happening or not.
- It is unequivocal that human influence has warmed the atmosphere, ocean and land. Widespread and rapid changes in the atmosphere, ocean, cryosphere and biosphere have occurred.
3. In U.S. cities, approximately what percentage of emissions come from buildings?
- 20 percent
- 50 percent
- 70 percent
- 100 percent
4. Net-zero operational carbon is:
- A highly energy-efficient building with all remaining energy from onsite and/or offsite renewable sources.
- A code-built building whose owner has purchased enough carbon offsets through tree plantings to claim net-zero energy status.
- A unicorn. There’s no such thing as net-zero energy buildings.
- A building that is highly efficient with upfront carbon minimized to the greatest extent possible and all remaining embodied carbon is reduced or, as a last resort, offset.
5. Net-zero embodied carbon is:
- A highly energy-efficient building with all remaining energy from onsite and/or offsite renewable sources.
- A building that is highly efficient with upfront carbon minimized to the greatest extent possible and all remaining embodied carbon is reduced or, as a last resort, offset.
- A unicorn. There’s no such thing as net-zero embodied carbon buildings.
- A building that is built only from natural materials that have been sourced locally using only manual labor or beasts of burden for transportation and construction.
6. Whole life carbon is:
- The total amount of carbon emissions released by disposing of a roof in a landfill.
- The total amount of carbon captured by planting trees to offset building material embodied carbon.
- An ancient industrial process that uses highly pressurized gases inside solidified carbonite to preserve biological organisms for intergalactic travel.
- The sum of operational carbon and embodied carbon.
7. Overburden is:
- Any manner of additional load on a roof from snow, severe hail, or wind.
- Any manner of material, equipment or installation that is situated on top of, and covering all or a portion of, a roof or waterproofing membrane assembly.
- Any manner of severe storm or “bomb cyclone” that floods sewer systems and impervious surfaces with rainwater.
- None of the above.
8. Roofs can significantly reduce the operational carbon of buildings by including:
- A thermal-bridge free roof assembly with the roof assembly seamlessly integrated into the vertical wall air barrier.
- Robust climate-specific levels of continuous insulation.
- Rooftop solar.
- All of the above
9. A purple roof refers to:
- The color of the roof membrane.
- The color of the cover board used on flat/low-slope roof.
- A roof that incorporates rainwater retention and detention with a sponge-like layer made of hydrophilic mineral wool to increase the volume of rainwater that can be retained or detained and reduces peak outflow by up to 95 percent.
- All of the above
10. In tropical climates, the lifecycle carbon emissions of a concrete roof can be reduced nearly 85 percent by:
- Adding fly ash to the concrete mix.
- Recycling the concrete at the end of its useful life.
- It can’t be done. Concrete and steel have too much embodied energy from their heavy manufacturing processes.
- A vegetated roof.