The design team found the perfect solution to meet the needs for B-Line Condominiums in Toronto: a continuous insulation solution; the need to accommodate a complex design with multiple finishes; and the tight, constricted jobsite. All photos courtesy of Sto Corp.
Whether it is designing for a residential property, a multifamily development, or commercial projects, architects and designers must consider several major factors. How will the building stand out from the rest? How will the design fulfill the performance criteria for the structure? How can the design plan deliver multiple, coordinated aesthetics without compromising the integrity of the building envelope?
Ultimately, the choices and product selections made by an architect have a cascading effect that impacts the entire project team—from the installer to the contractor, to the building’s owner and its eventual inhabitants.
Today, there is an increasing appetite for the building envelope to display a more complex, dynamic look created by multiple claddings. This, in turn, creates a new set of challenges for architects: ensuring that multiple cladding types work flawlessly together once installed. What is the most foolproof method to ensure this happens?
The answer: select a single manufacturer, one that can deliver multiple materials to meet the structure’s required aesthetic and performance mandates.
What’s Trending?
Mixing cladding materials on building exteriors has been a popular trend for the last 10 years, one that has gained added momentum in the last five years. In fact, multiple claddings are a mandate in some cities, especially for multifamily residential construction where two or three exterior styles are being combined to create more visual interest. This trend can be seen driving through many cities throughout North America.
The B-Line Condominiums in Toronto are a perfect example of a multifamily development taking full advantage of multiple aesthetics, combining the look of brick, wood, stone, and metal panels all on a single system.
Regionality and vertical segment each play a role in design as well. For example, stucco finishes remain in widespread use throughout the Southwest, but are not specified nearly as much in the northern United States. In addition, the use of tilt-up construction continues to rise, particularly for large warehouses and distribution centers, a segment that continues to grow to fulfill the ongoing demand for storage and shipping for ecommerce businesses.
Metallics are in high use as well, but as mentioned, exterior trends depend on regional market and construction segment. Metal cladding is used in a variety of segments and areas of the country for myriad construction types, including office, hospitality, healthcare, education, recreation, transportation, and multifamily buildings. Ultimately, there is no denying that multiple aesthetics are in high demand.
Why One Vendor?
For large-scale building envelopes—particularly ones that incorporate multiple claddings—consider how many different components must work together to produce a code-compliant, well-built, high-performance exterior. As architects consider the eventual look of the building, they must first ensure that the building envelope will protect its inhabitants and secure the structure for its entire lifespan. The control layers of the building must guard against rain, wind, snow, UV rays, temperature changes, and more. Those control layers include:
- A vapor retarder to minimize condensation by controlling the flow of water vapor as it shifts from high- to low-pressure areas.
- An air and water-resistive barrier that reduces energy and condensation loss by limiting the uncontrolled flow of air through the wall assembly.
- A water penetration barrier that prevents water from entering the wall cavity and is flashed to the cladding’s exterior.
- A thermal barrier to mitigate energy loss and prevent thermal bridging.
- A durable and water-shedding facade to protect against environmental elements, impacts, UV exposure, pollutants, and more.
What if the building design could remove the majority of complexities when it comes to installing the facade, while also condensing the project schedule, and minimizing the number of trades and manufacturers required to complete it?
To achieve this, architects today can select a single manufacturer that can provide the highly sought-after multi-aesthetic exteriors that are in demand. Moreover, these systems from a single provider deliver consistent control layers that allow the entire building envelope to operate as a unified system, all while helping to eliminate installation difficulties along the way.
B-Line Condominiums in Toronto.
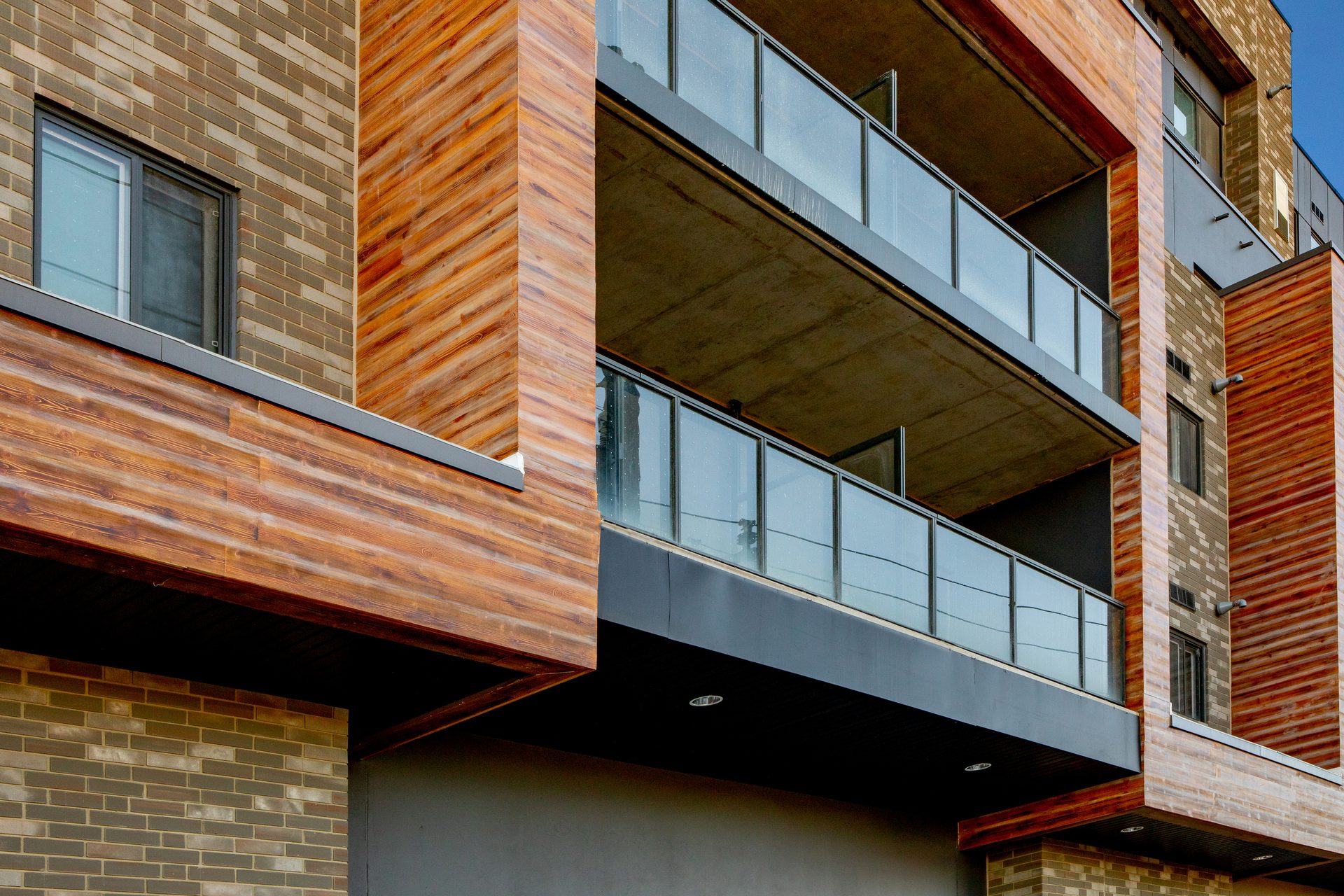
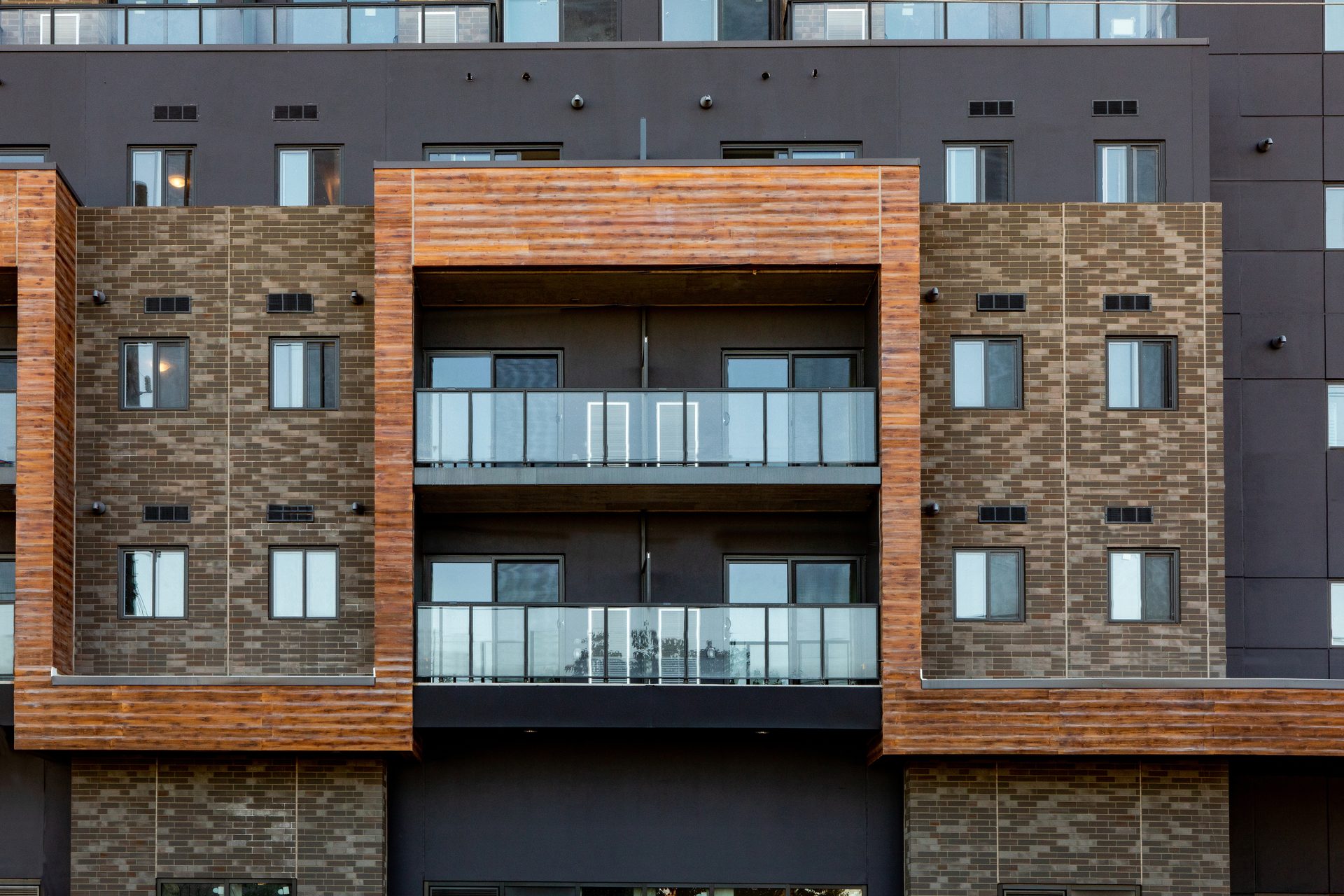
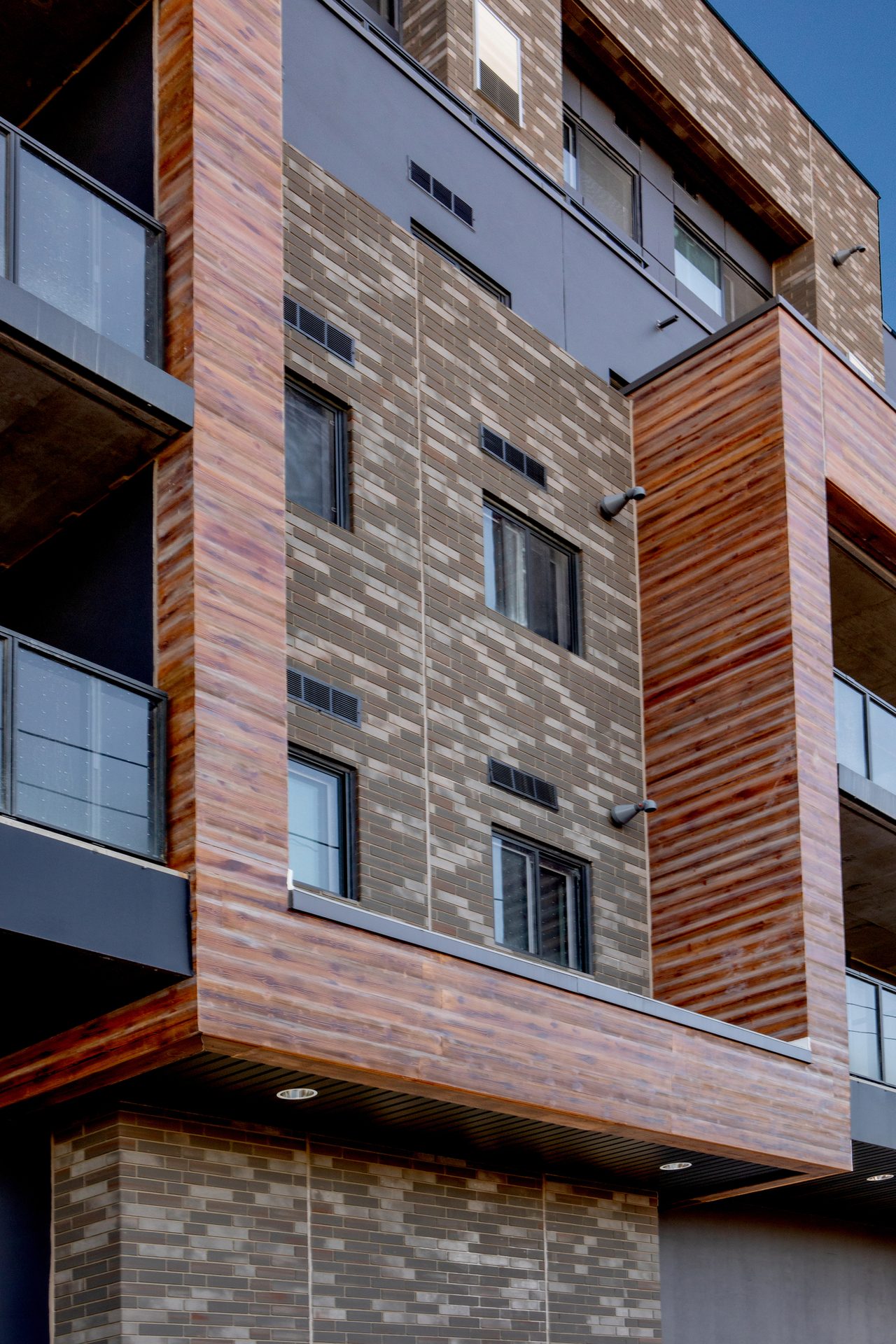
B-Line Condominiums
The Design is in the Details
For architects, detailing becomes much easier when working with one vendor for cladding materials. According to NYC-based architecture firm, k–da, “If you have not been through a design process, you may not have heard of the concept of architectural detailing, yet it may be the most crucial part of a design.”
Technical detailing pertains to planning for the performance of a structure and the assembly of its components. Highlighting the importance of detailing for facades, k–da cites, “all the drawings and specifications that work to keep water out are examples of technical detailing.”
When architects choose one manufacturer for cladding on a single building, the detailing process becomes much simpler. That is because the system behind the aesthetic components is the same (or very similar) regardless of which cladding materials are selected.
To use a hypothetical example, designers of a high-end multifamily residential building in a populous metropolitan area are able to specify a rainscreen, EIFs, and brick veneer all on a single building. Because materials are coming from the same vendor, the control layers behind each cladding component remain in synch and compatible. This eases designing, detailing, and installation, and most importantly, it helps to deliver reliable long-term building performance.
The Liability Question
The age-old challenge when there is a hiccup in a building’s performance: who is to blame?
Building enclosure technology is the best it has ever been. However, construction requires the ultimate collaboration, where many different trades and building materials and systems must function as one. As it relates to the building enclosure specifically, architects and owners can ease their liability concerns by choosing one cladding provider. This way, if any issues arise and need to be addressed after the initial installation, they know who to call. There is no back-and-forth dialog between different trades and various cladding vendors. Choosing one supplier for the cladding and integrated control layers provides a single source for warranties, technical service claims, and overall project oversight and support.
Avoiding a Not-So-Smooth Transition
When two different cladding materials from two different manufacturers are specified for the same project, at some point, the two materials must join on the face of the building. Which party is responsible for ensuring those materials and their control layers will actually work together for the life of the building?
Vendor A points to Vendor B. Vendor B points to Vendor A.
Architects and the eventual installers need to consider transition materials between claddings, and it is often difficult to determine what materials will work in harmony.
What is at risk? Moisture intrusion.
Unwanted moisture penetration can begin at a tiny spot on the building, and this small intrusion can evolve into a major problem for the structure and its components. Choosing a single manufacturer can help avoid this, and it also eliminates the finger pointing between vendors.
From the beginning of an architectural concept, an architect should conduct The Pen Test. With this exercise, a designer can draw a line on the surfaces of a wall, following the air and water-resistive barrier across the entire structure without a break. If there is a break, or the architect has to lift their pen, then there is a patch for water to enter. When architects choose a single manufacturer, they ace The Pen Test.
In addition to decreasing the risk of moisture intrusion, a single manufacturer gives valuable peace of mind that all components work together.
333 Grand Street in the Liberty Harbor area of Jersey City, New Jersey uses multiple StoSignature™ finishes to create a vibrate facade while providing occupant comfort and indoor air quality with an energy-efficient system designed for form and function.
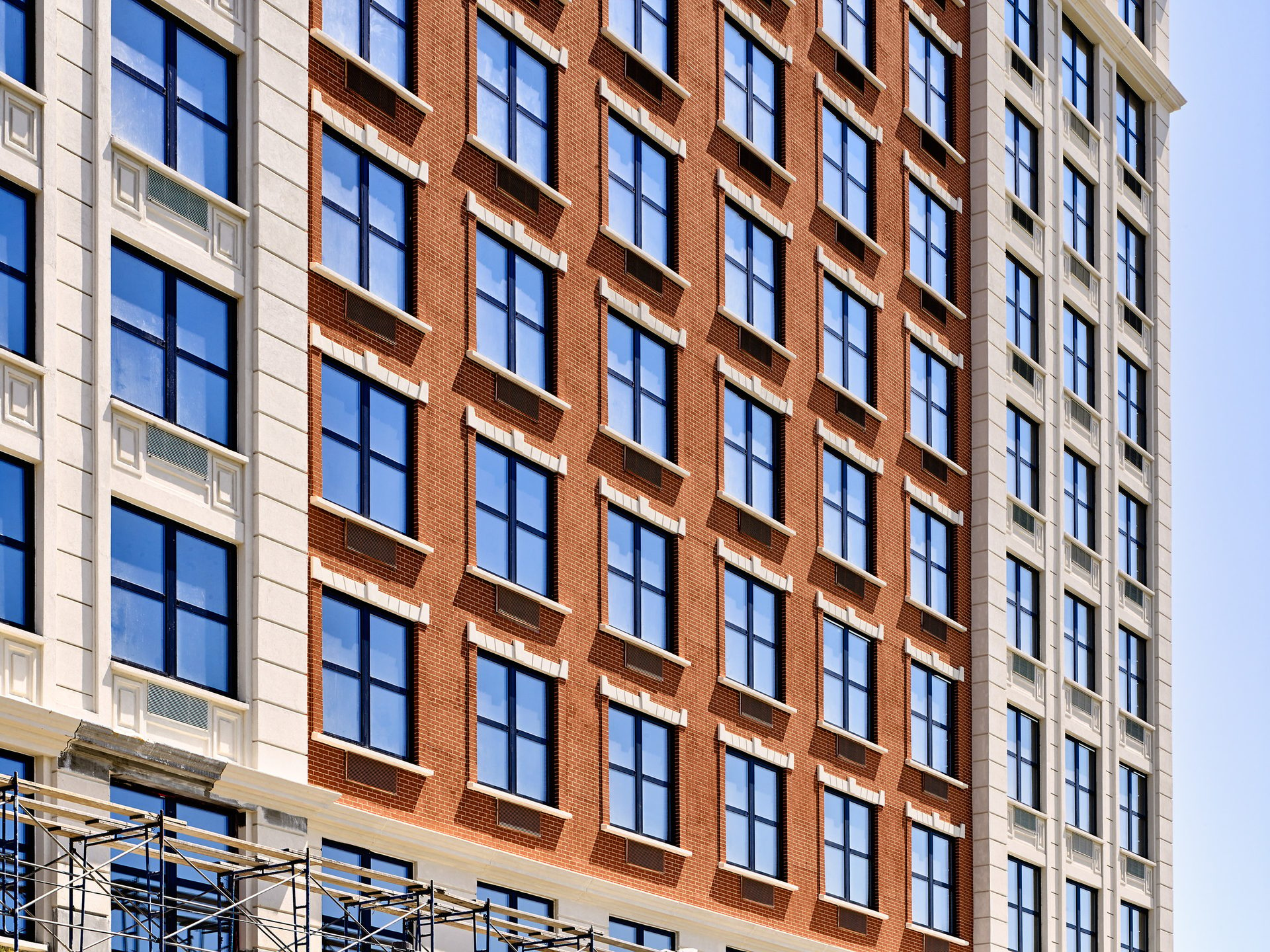
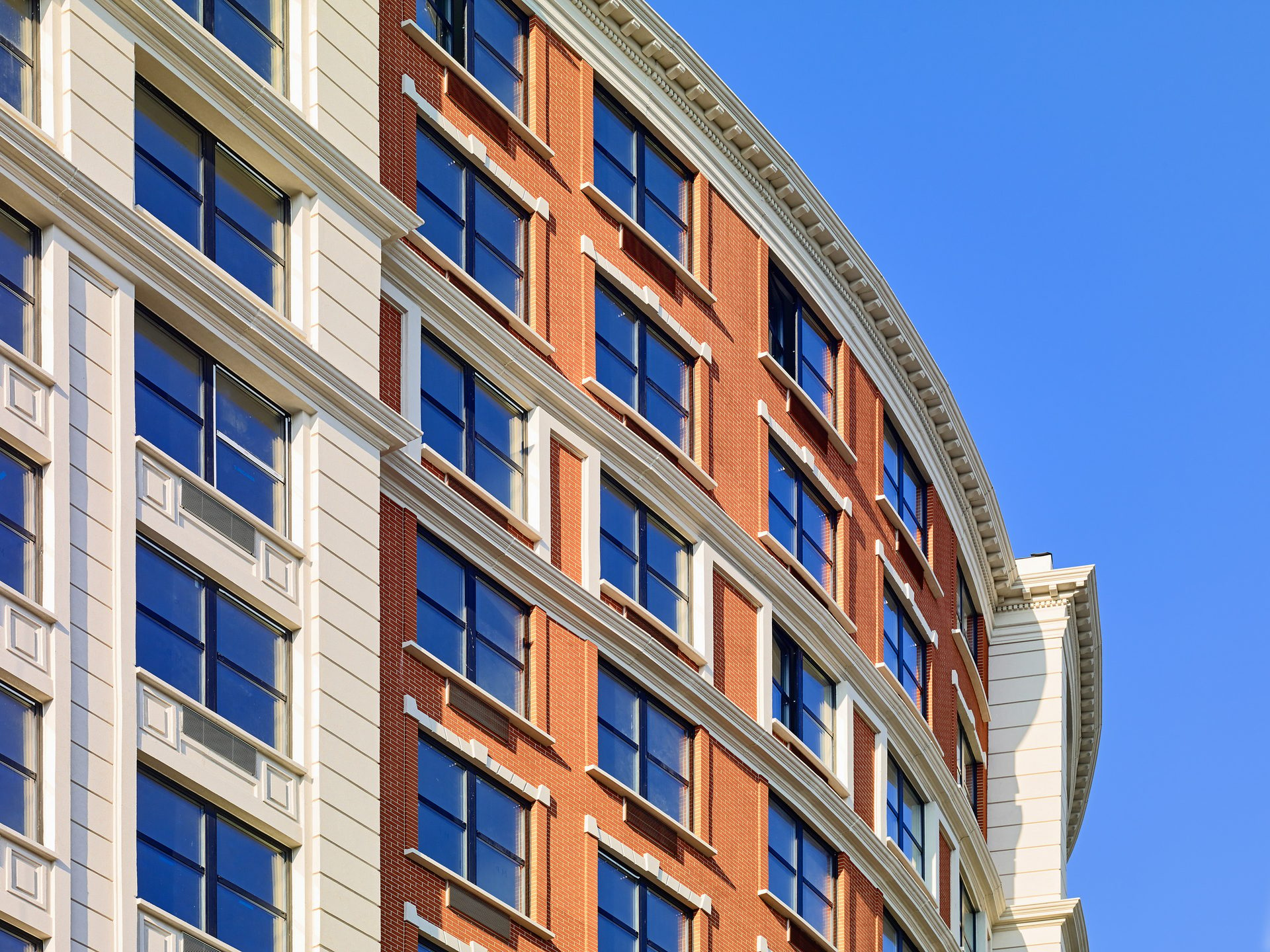
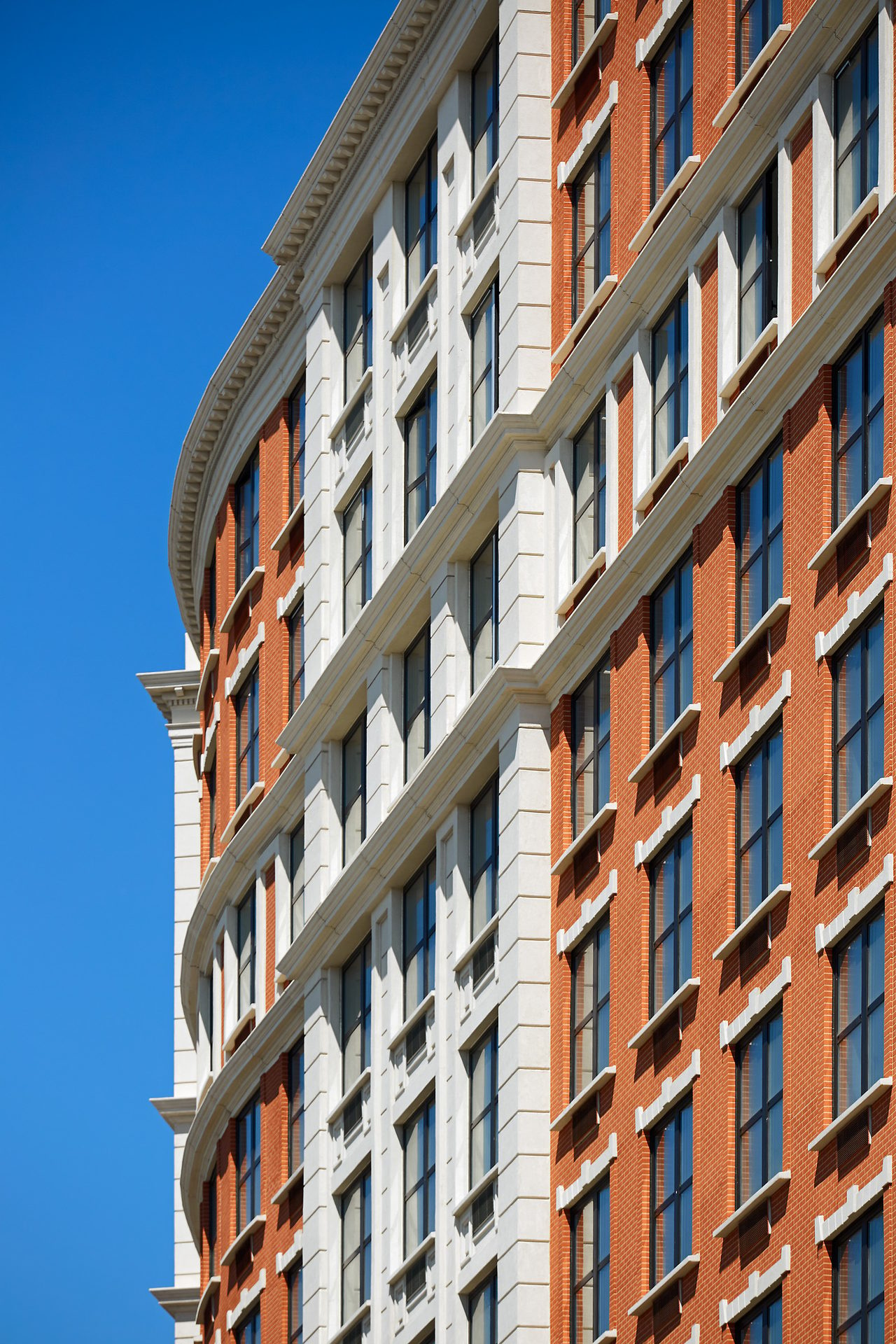