Concrete is the most widely used construction material in the world. And precast concrete wall panels have been used for decades as a practical solution for exterior walls for a wide variety of end-uses.
As the building industry looks for way to reduce greenhouse gas emissions, it is crucial to find ways to reduce the carbon footprint of precast concrete wall panels without losing the performance characteristics that make them a valuable option for the building team.
All building products have two central components of their carbon footprint: embodied carbon and operational carbon. Embodied carbon refers to the carbon footprint of building materials during their lifecycle. According to Architecture 2030, embodied carbon will be responsible for almost half of total new construction emissions between now and 2050. Operational carbon emissions refer to the energy used in building operations. These emissions can be reduced through energy efficiency and the use of renewable energy.
Sandy High School in Sandy, Ore. Photo courtesy of Josh Partee.
Decarbonizing Cement
CO2 is released at two points during cement production. Roughly 40 percent of the CO2 generated is from the burning of fossil fuels in the manufacturing process. The remaining 60 percent is from naturally occurring chemical reactions during processing. The proportion of ingredients in a concrete mixture can significantly influence its carbon impact. Cement is only one component of concrete. On average, it represents 12 percent of concrete’s weight but 90 percent of its carbon.
Companies have several options for decarbonizing cement. About 20 percent of the reduction will come from improved operational measures such as energy efficiency. The rest of the reductions will come from technological innovation.
The Portland Cement Association (PCA) has created a roadmap to become carbon neutral across the cement and concrete value chain by 2050. The PCA recognizes the important role of the industry to further reduce greenhouse gas emissions and creating sustainable building solutions given the significant role of cement in society and anticipated infrastructure development. The roadmap outlines ways to reduce carbon throughout the phases of the built environment: production at cement plant, construction, and everyday infrastructure use.
A Lower-Carbon Precast Wall Panel
Strategies exist for creating precast walls that are lighter, stronger and thinner, which require less energy and embodied carbon in manufacturing, then deliver energy savings once a building is commissioned. There are three areas to consider:
Product: how can we design and engineer the product with less cement and embedded carbon?
Process: how is the product manufactured? How can we reduce the carbon footprint of production? How does installation compare to other products, and how can we lower the environmental impact further?
Performance: how can the product reduce energy consumption in the element and final assembly?
Technologies to reduce the carbon footprint of cement are promising but are still in development. At this time, the most pragmatic, cost-effective way to reduce the embedded carbon in concrete is to simply use less cement.
One option is to replace some of the cement with supplementary cementitious materials (SCMs). SCMs are usually a byproduct of industrial processes and are often disposed of in landfills. But they show cementitious properties when mixed with water or water and other compounds.
Fly ash is the most commonly used SCM in concrete. It’s a residue left from burning coal in electric power generating plants. This SCM improves concrete’s workability, pumpability, cohesiveness, finish, ultimate strength, and durability. Slag cement is made from ground granulated blast furnace slag (GGBFS) finely ground to become a hydraulic cement. Silica fume is a byproduct of producing silicon metal or ferrosilicon alloys. It’s often used to manufacture high-strength concrete. Because all these SCMs involve reusing a waste material, their availability varies by region.
Image courtesy of AltusGroup.
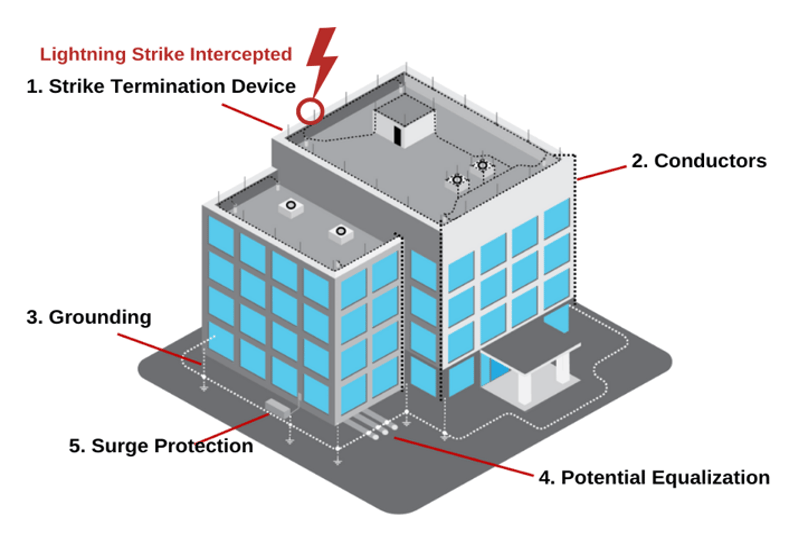
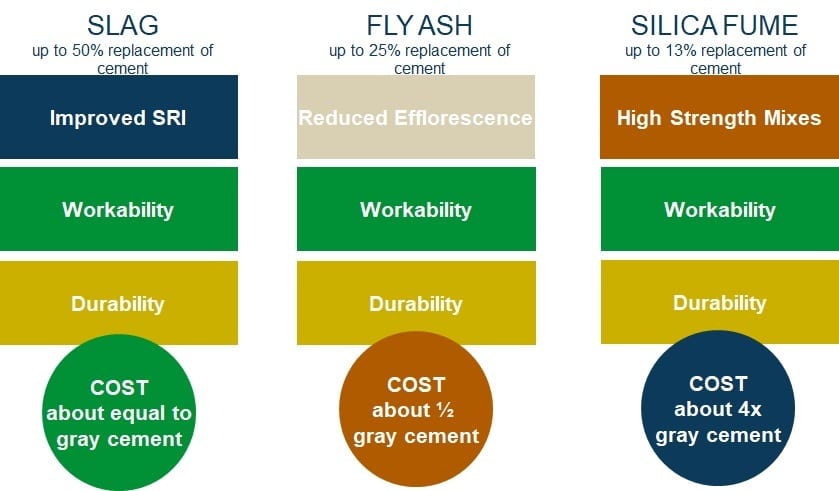
Aggregate selection is another way to reduce embedded carbon in the concrete mix design. Hard, clean and strong aggregates can be used to reduce the amount of cement required to achieve the necessary strength. Weak or lightweight aggregates usually need more cement in the mix. Soft, porous aggregates can result in weaker concrete with low wear resistance and thus have a shorter lifespan. The need for strong aggregates to reduce the cement quality and manufacture concrete highly resistant to abrasion with a longer lifespan is one reason why precast concrete is preferable to ready-mix concrete.
The carbon footprint of precast panels can be reduced through energy-efficient manufacturing and installation. Fabrication can be done in a factory dedicated to high-quality wall panels in mass quantities. Manufacturing in batches uses less energy versus onsite production. Some manufacturers use renewable energy including solar energy. Precast manufactures typically use local materials and manage water usage.
Manufacturing lighter precast panels means less fuel is needed to transport them. The speed of installing the panels is important for reducing carbon and minimizing site disturbance. Precast manufacturers can also install windows into the building envelope to eliminate additional handling and materials systems for the onsite trades.
Reduced-Carbon Wall Design
To reiterate the important point above, the most cost-effective way to reduce the carbon footprint of concrete is to use less cement. One way of doing this is by using a precast sandwich wall system. Instead of using a 7-inch solid concrete wall, one could specify a 2″ x 3″ x 2″ structural wall, which would replace three inches of concrete with three inches of insulation. This replacement will reduce the amount of cement and concrete by about 40 percent.
Image courtesy of AltusGroup.
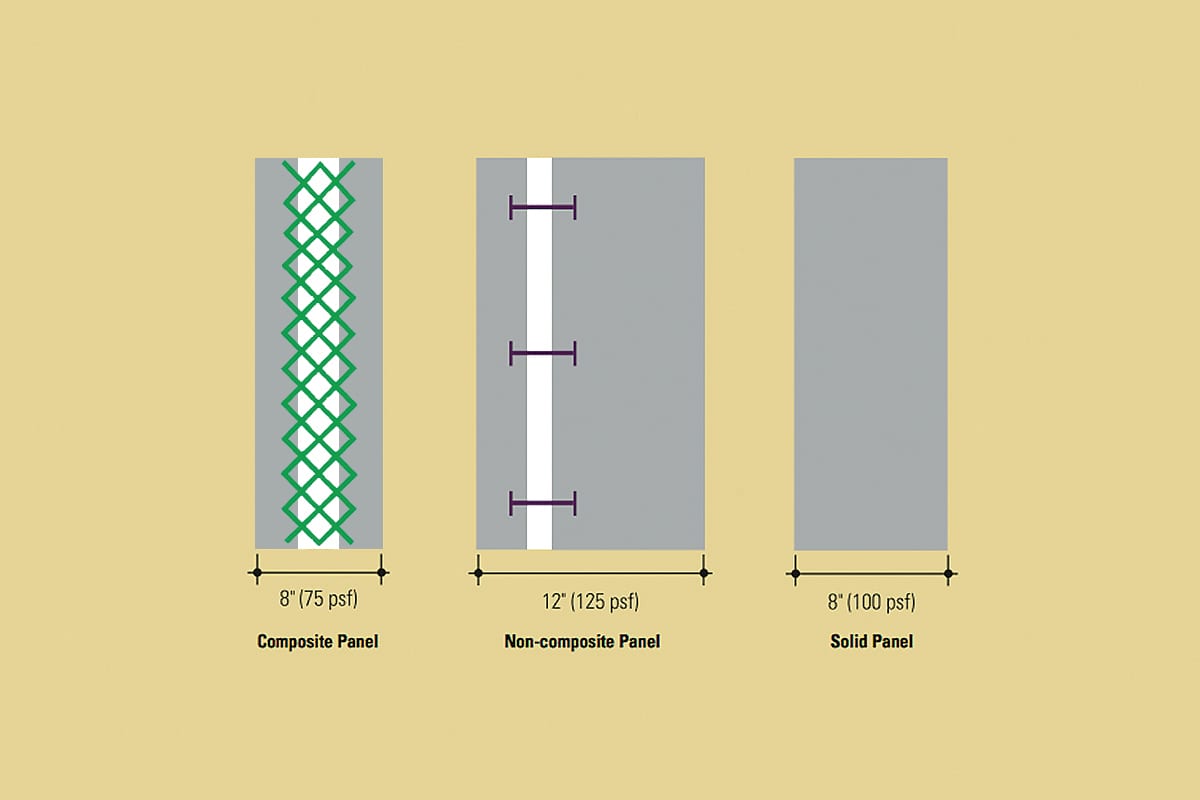
The key is composite performance enabled by the shear connectors that connect the interior and exterior wythes of concrete. Connectors such as carbon fiber grid can enable full composite action with each wythe working together to take the load. Sandwich walls with composite action perform comparably to a solid concrete panel or a non-composite panel that requires a thicker wythe to be fully load-bearing with a sacrificial exterior wythe.
The result is a precast wall panel significantly less concrete and a lower carbon footprint. Another example: a 3″ x 2″ x 3″ panel versus a standard 8-inch solid panel with a similar strength performance results in a 25 percent reduction in cement and concrete by replacing 2 inches of concrete with insulation.
Another way to reduce the amount of concrete—and therefore the amount of cement—is through non-corrosive face reinforcing. The American Concrete Institute (ACI) requires a minimum cover for steel reinforcing. But with a composite reinforcement, the concrete cover used to protect wire mesh from corrosion can be reduced by up to 60 percent. While there are many factors that go into determining the depth of an exterior concrete wythe, the use of non-corrosive reinforcements are an option worth considering.
Still another possibility for reducing cement is to use thin-precast technologies in a rainscreen configuration to achieve precast aesthetics without the same depth of concrete. They include ultra-high performance concrete (UHPC) in a solid or sandwich design. Non-corrosive stainless steel prestressing can also be used to create thin concrete rainscreen panels. Because they function as rainscreens and not rain barriers, they have other considerations such as panel size, joints, tolerance, and fasteners. Various fastener systems can be used to achieve a specific aesthetic look, whether it be mechanically fastened or through hidden fastening systems.
The choice of insulation is important, too. When selecting insulation, consider the operational performance (thermal performance, climatic requirements, air leakage rates, moisture resistance), which should be balanced with the targets for reducing embodied carbon. Additional considerations include any environmental requirements set by the states. Expanded polystyrene (EPS) and graphitized foam systems have significant amounts of recycled material in their foam. Extruded polystyrene (XPS) has a higher embedded carbon impact but provides about 25 percent more R-value per inch than EPS and offers other benefits.
Further embedded carbon reductions are possible with the finish. There are many alternatives to embedded extracted stone with precast concrete depending on the degree of blast sandblast and the possibility of using acid-etched concrete. There are also numerous alternatives to sandblasting technology being investigated and developed. The ability to embed thin brick into precast can provide an alternative delivery system to conventional building methods that require full-depth brick.
Globe Life Field, in Arlington, Texas, began serving as the home of the Texas Rangers in 2020. The stadium is a prime example of how to reduce the carbon footprint of exterior finishes by using innovative precast techniques rather than extracting rock. Photo courtesy of Jacia Phillips.
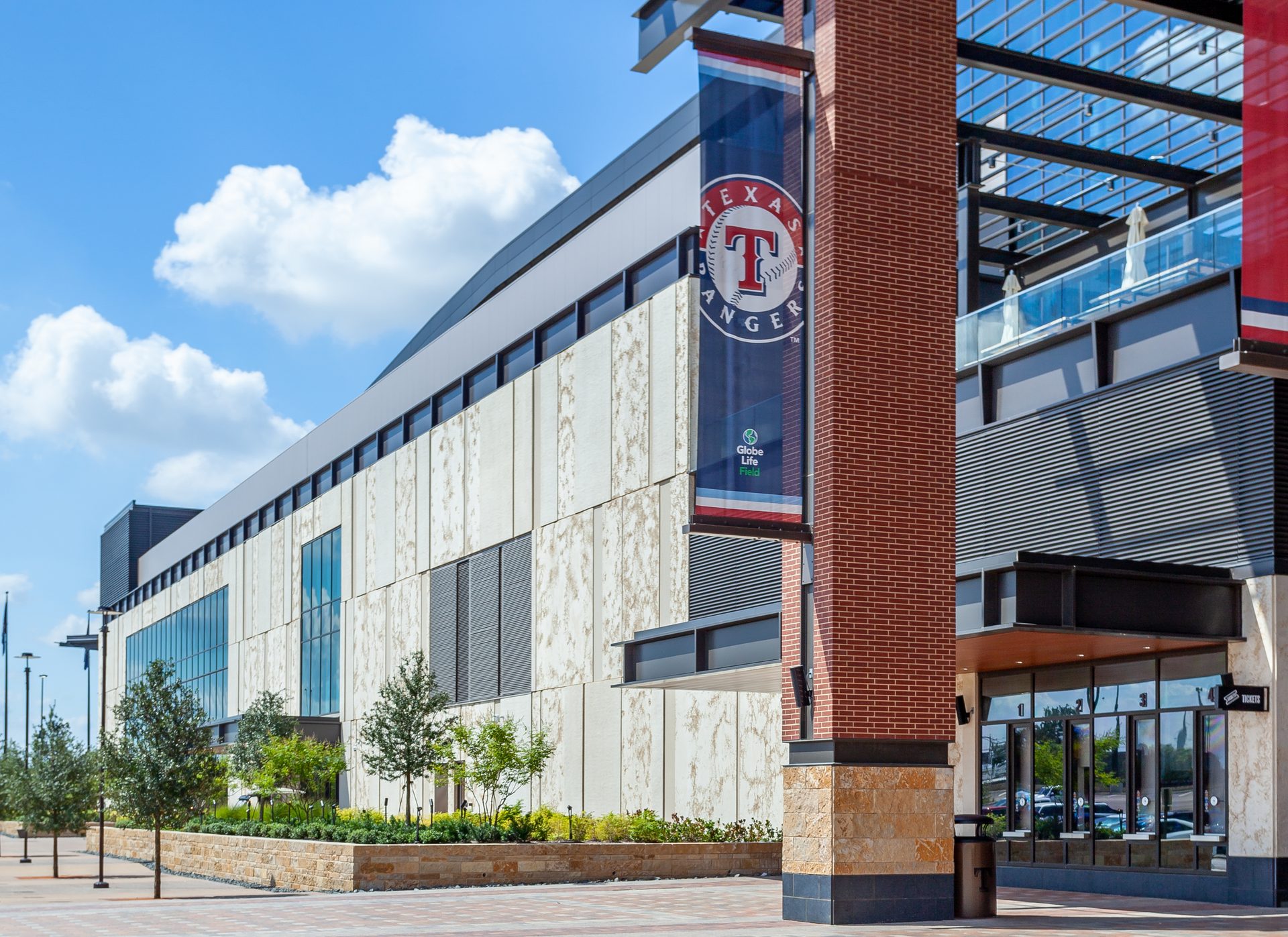
Operational Carbon Reduction
Continuous insulation in precast walls is also an important consideration reducing the operational carbon. ASHRAE 90.1 sets the minimum requirements for the energy-efficient design of buildings except for low-rise residential ones. It defines continuous insulation as “insulation that is uncompressed and continuous across all structural members without thermal bridges other than fasteners and service openings.” All precast sandwich panels with integral continuous insulation must comply with ASHRAE 90.1. These systems must use very low conductivity wythe connectors.
University Commons at Georgia State University demonstrates how continuous insulation results in lower operational carbon. The original design of the exterior walls was brick veneer backed up with six-inch metal studs, batt insulation and a drywall interior. The building team opted instead for an insulated precast system with four inches of EPS sandwiched between two 2.5-inch thick concrete wythes.
Based on ASHRAE 90.1 the effective R-value of the original brick, metal studs and batt insulation design was R-7.1. An improved R-value of R-12 was achieved using the precast wall panels. The increased R-value enabled the university to specify a less substantial heating and cooling system, saving $700,000 and enabling a significant reduction in operational carbon over decades of use compared to the original system.
GSU Courtyard at University Commons. Photo courtesy of Metromont.
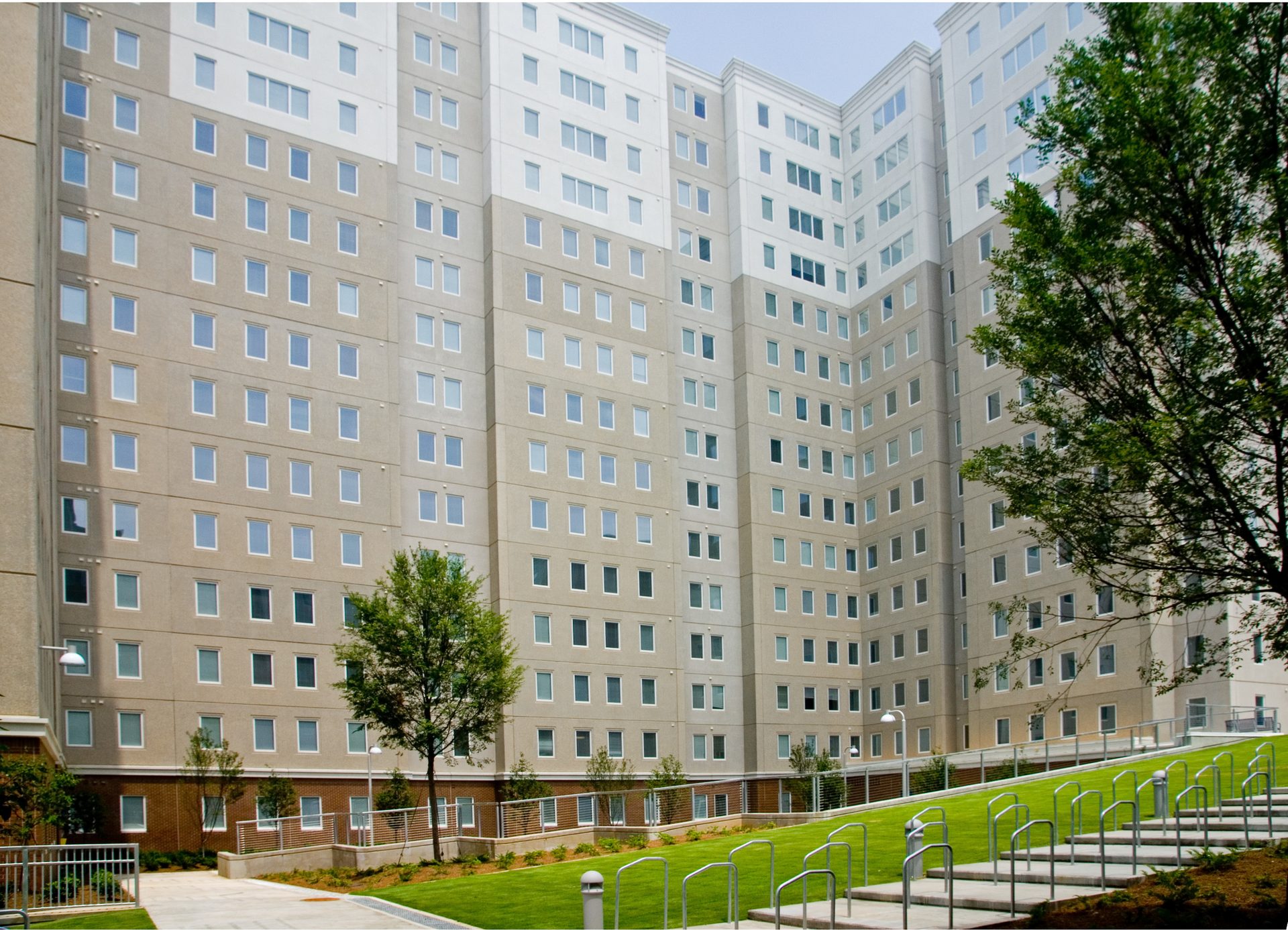