Building airtightness continues to grow as a design consideration or requirement in most modern building designs. However, due to the complex nature of architectural design, building components, system options, involvement of multiple trades, and the pace of modern construction, achieving airtightness in a building is often easier said than done.
Airtightness is virtually always achieved by installing some form of an Air & Vapor Barrier (AVB). An AVB is utilized to prevent moisture flow from entering the building envelope. An AVB may consist of many different products or systems, all of which have an appropriate time and place for consideration.
At RoofTech Consulting, a third-party building enclosure consulting firm with twenty-two years of experience, our team focuses on the assessment, design, testing, and forensics of commercial roofing and waterproofing. When researching an issue or possible failure, we begin by reviewing the design, details, etc. Often, we find the most common issues lie within the installation of the AVB systems rather than the design or materials.
Although the design and materials are typically not the cause of the issues we encounter, we do commonly find a lack of detailing (specifically where varying materials lap), minimal direction for testing, and poor submittals during the early stages of our investigations. Most manufacturers only provide details for their specific products, not where their products stop or meet other materials. As a result, detailing these transitions and laps becomes the design team's responsibility and, unfortunately, is often not addressed.
In those instances, we hope to find these conditions addressed in the shop drawings or submittals. Rarely do we find that the installer has provided that level of detail in their submittals. Yet, they have been approved. The design team should also provide guidance for American Architectural Manufacturers Association (AAMA) and American Society for Testing and Materials (ASTM) testing of the AVB (and possibly other systems), including which tests to perform, testing location(s), frequency, and in some cases, testing parameters. Whenever this information is missing, the project invites a high risk of installation failure before the installer ever steps foot onsite.
Each area of the building will typically involve different trades, subcontractors, and systems attempting to create a cohesive airtight environment. What makes this even trickier is the ever-evolving market of materials specified to create an airtight environment. With each system comes different materials, installation training, and compatibility concerns with other AVB components across the various installation teams. It takes extensive communication, scheduling, and mobilization to ensure all these elements work together.
All too often, the subcontractors have not bid or anticipated this level of correspondence and preinstallation involvement. All AVB installers should be aware of and share with their team’s material manufacturer training/certifications required, project schedules, sequencing, unique detailing requirements, cure times, hand-offs, testing milestones, etc.
It is recommended to require the design team, project managers, and field staff from the various installers who constructed the mock-up to be present during all mock-up testing. This keeps all parties aware of detailing performance, detailing variances, and phasing requirements that can be implemented during final construction. All photos courtesy of RoofTech Consulting.
The above image shows a sacrificial sheet atop the leading edge of below-grade waterproofing installed to avoid fish mouths while awaiting backfill and protection during backfill. The installer learned this technique on a previous project and retained it as a best practice for future installations. Allowing the team to share these types of practices is highly recommended.
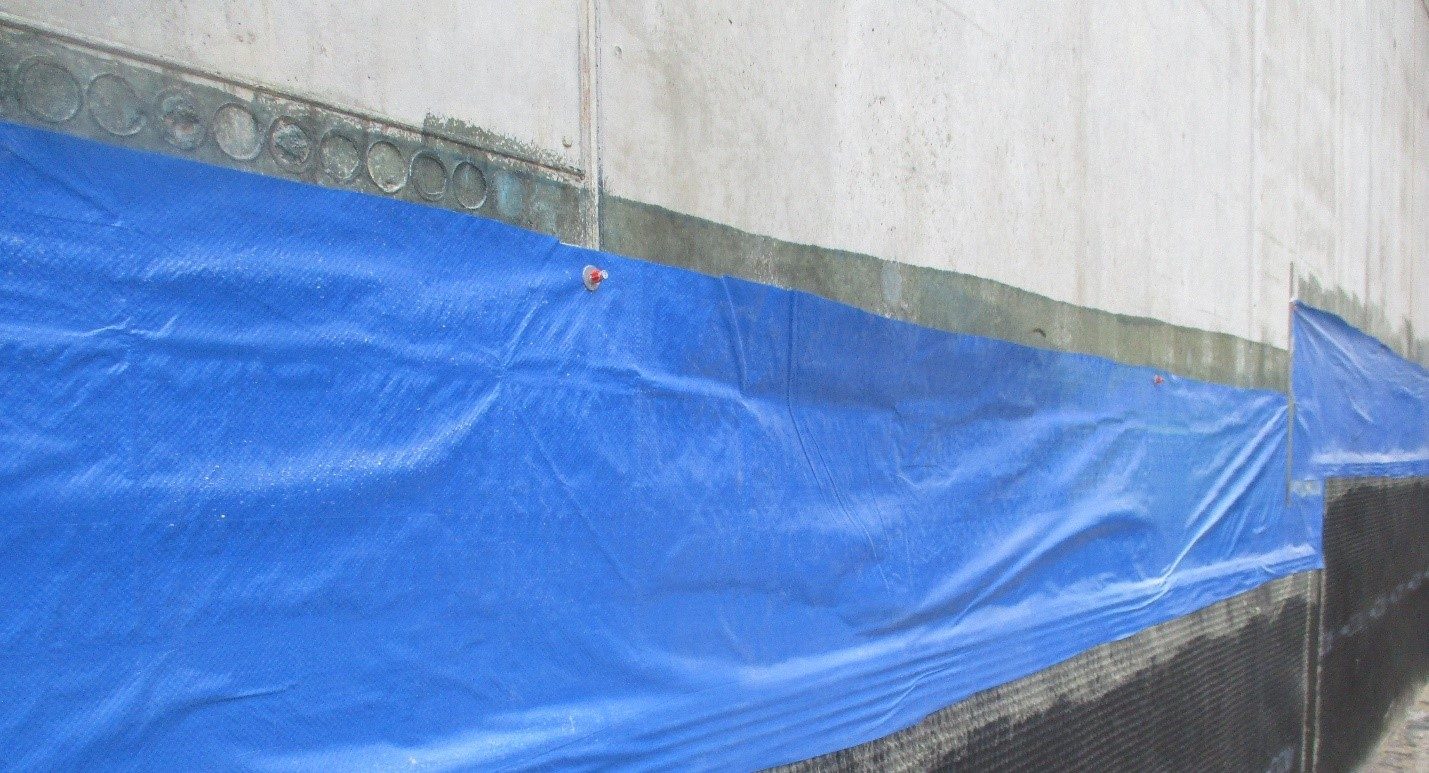
The Installation Phase
At this point, assuming the design & submittals are sufficient, and the installer has been appropriately involved in the preinstallation process, we reach the installation phase. Each AVB has its own set of complications, depending on the area of the building enclosure in which it is installed. Let’s follow the typical cadence of a new construction build by beginning with the “blindside” or below-grade AVB, which includes below slab and vertical walls below-grade. The below-slab AVB commonly consists of different materials than the vertical walls below-grade. This is where the installation commonly encounters its introduction into multiple installers, sequencing, and differing materials.
Below-slab installations encounter a large amount of traffic and risk during concrete forming and pouring. The vertical below-grade AVB installations will often face issues with overexposure of the materials while awaiting backfill, sagging, and “fish mouths” along the leading edge while they await lapping by other above-grade AVB materials. Although most of these issues can be identified during installation quality assurance inspections and testing, unaddressed issues may not become apparent for many years. Attempting to identify these areas of failure and complete long-term remediation years later can be extremely difficult, intrusive, and sometimes impossible, based on the grounds and conditions surrounding the finished build.
Commonly, the second phase of AVB installation, above-grade vertical walls, extends to the roof elevation. During vertical above-grade wall AVB installations, installers will encounter varying materials required based on the finish components needed to meet the designer’s vision. Issues are often found at punched openings, such as windows and doors, where correct detailing was not installed. This is more common when installers use commodity-type sheet AVB systems that often require multiple tapes, flashing, materials, etc. Penetrations, clips, brick ties, and other similar components are commonly installed to the wall’s surface after the AVB contractor has completed their scope and is offsite. Too often, these areas (where they disrupt the AVB) are never properly sealed/detailed.
Engaging a qualified representative to perform quality assurance (QA) during installation ensures the materials and detailing are installed as designed, including lessons learned during mock-up testing.
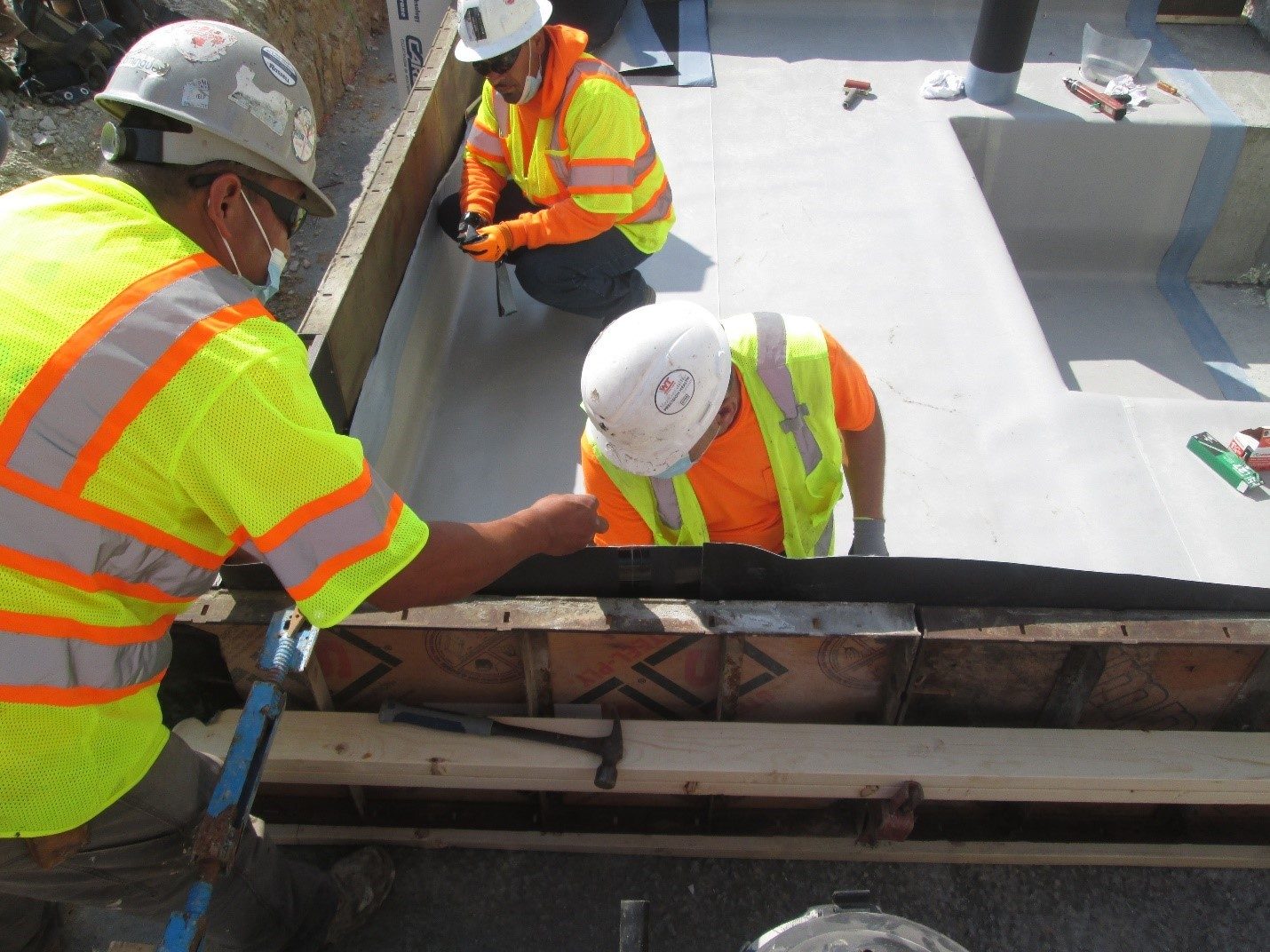
Investigating the Enclosure
During many of our investigations of the building enclosure, we find that the AVB installer was unaware that their installation had been affected by other trades, nor were they ever contacted to return for repairs or to detail areas of later work. Like below-grade and blind-side issues, most of these issues can be identified during installation quality assurance inspections and testing. Still, they likely will not become apparent for many years if not addressed initially. Once the building is cladded, interior finishes are installed, and the building is occupied, it becomes very disruptive for investigation and remediation, often requiring interior finishes and exterior cladding(s) to be removed.
The roof is often one of the final building components to receive AVB consideration. Most roof AVB installations rely on adhered sheet materials. For these installations, contractors often don’t utilize standard watertight/airtight detailing. The AVB is commonly installed more like a “temporary” roof than an airtight barrier. Too often, the roof AVB is also “self-terminated” when the AVB reaches a vertical transition or wall scenario without mechanical termination or proper lapping. Although most material manufacturers don’t require a mechanical termination of their products in these areas, it is an agreed-upon best practice. As this AVB is usually the last to be installed and at the highest elevation, it should almost always lap over any other AVB materials, especially atop parapet walls.
Now, let’s review some best practices to avoid these most common failures on future projects. With so many components, installation methods, materials, and points of error, it is crucial to involve a building enclosure consultant or expert from the project’s inception. From the initial design, subsequent submittal review, preinstallation meetings, mock-up review, quality assurance, and testing, their presence will significantly reduce the risk that the building envelope faces premature failure. A liaison overseeing all aspects of the project will provide a seamless line of communication between all parties and compatible installation throughout.
During our investigations, we frequently find that the installers have been underutilized in the preinstall phases of the project, which compounds and snowballs through installation. Best results can be achieved by creating a communicative environment where installers understand preinstallation expectations, mock-up requirements, work area sequencing, etc. Once these meetings begin, all parties should review schedules, hand-offs, detailing, best practices, completion schedules, and testing requirements/needs.
This image shows remedial work to correct a failed rooftop AVB. Although mechanical termination and shingle lapping are not always required by AVB manufacturers, it is recommended on all rooftop installations. This is another example of a lesson learned by the designer and installer that can be utilized on future projects.
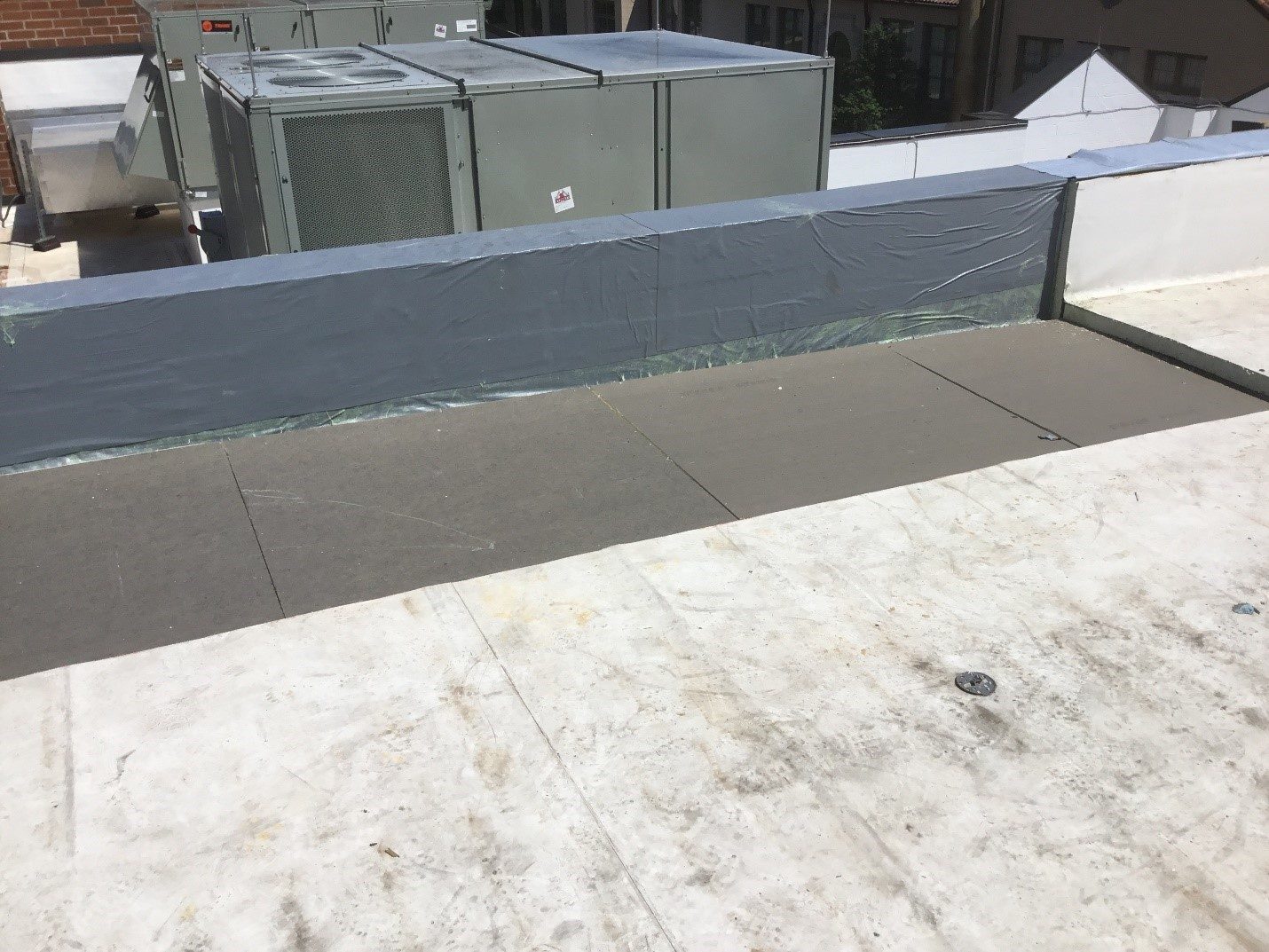