Photo courtesy of Seven Storm via Pexels.
According to Architecture 2030, the built environment generates 40 percent of annual global CO2 emissions with at least 13 percent stemming from construction activity and materials. Embodied carbon refers to the Greenhouse Gas (GHG) emissions from the extraction, manufacture, transport, and disposal of materials. The upfront emissions are locked in at the time of building construction, and unlike energy efficiency, cannot be changed or significantly reduced over time. Without considerable intervention, the portion of global emissions due to construction materials will continue to increase with demand for new buildings to accommodate population growth, need for replacement of aging infrastructure, and a decrease in the relative proportion of operational emissions due to an increase in renewables and energy efficient technologies.1
Figure 1: Annual Global CO2 Emissions2
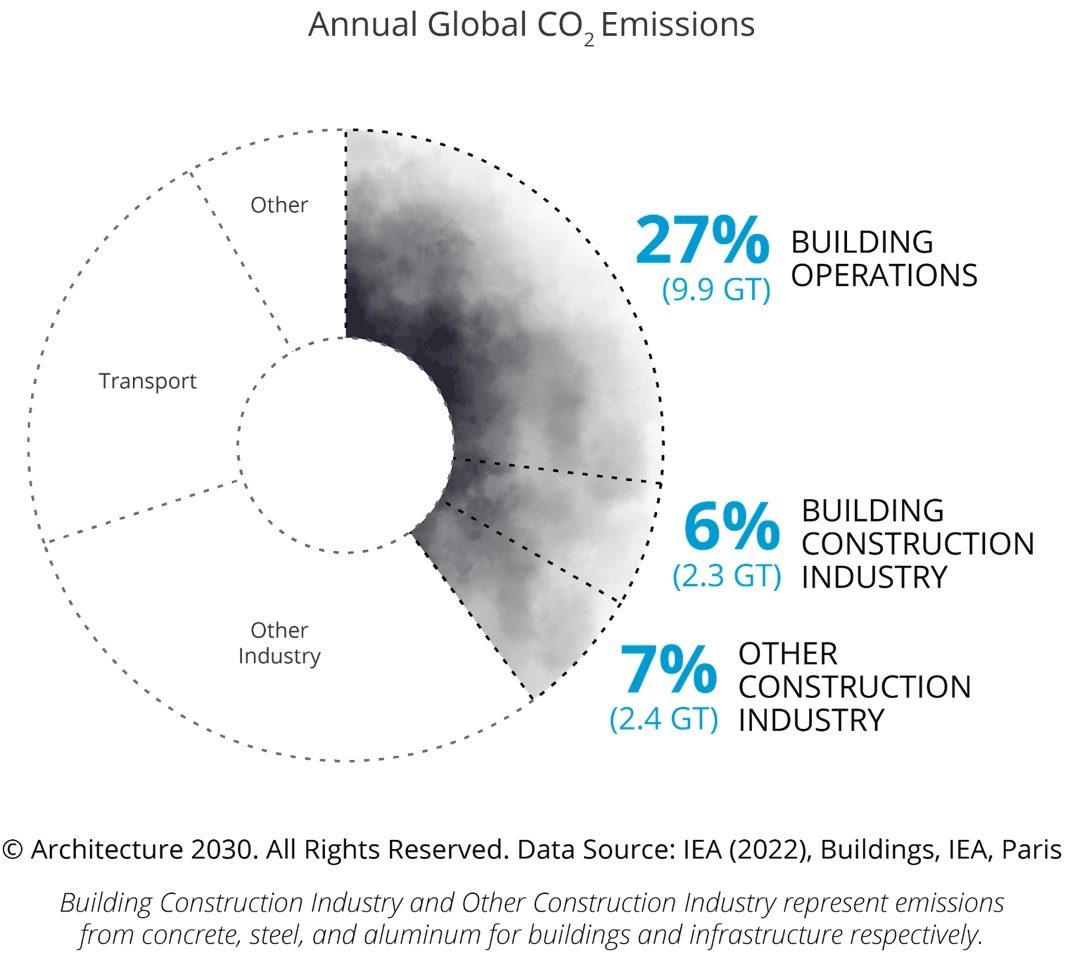
Embodied carbon can be addressed in two ways:
- Reduce material volume by incorporating efficient design solutions and reused or salvaged material.
- Install low-carbon materials by comparing and selecting products with a lower life cycle carbon footprint, as reported in Environmental Product Declarations (EPDs).
Building Enclosures
When it comes to the building enclosure, the design strategy typically centers around performance and energy efficiency rather than material impact. Enclosure specialists tend to focus on questions like; Will the building leak water?; Do the details support air barrier continuity?; Is there enough insulation and is it effective?; Can we eliminate thermal bridging?; How can we mitigate solar loading at glazing areas? But we now know that it is critical to also overlay material embodied carbon impact when developing building enclosure designs.
While a more significant portion of embodied carbon comes from a building’s structure, enclosure materials do influence embodied carbon goals. This means that selecting and designing for low-carbon enclosure materials is important for reducing the overall embodied carbon impact of the building. It is important to note that using heavier enclosure assemblies may require additional structural support, increasing the embodied carbon associated with the building structure. However, the building structure was excluded from this analysis to isolate the impact of the enclosure components, specifically exterior wall assemblies.
This article examines common facade-insulation combinations to help understand how enclosure material selection affects embodied carbon.
Comparing and Selecting Materials Based on Embodied Carbon
Materials can be compared and selected using product-specific Environmental Product Declarations (EPDs). EPDs are transparency documents that report the environmental impact of materials throughout their life-cycle, typically from the extraction of the raw materials through manufacturing which is deemed upfront carbon emissions. Materials can be compared based on their global warming potential (GWP), or embodied carbon, as long as they fall within the same Product Category Rule (PCR) which is the “recipe” manufacturers must follow when developing their EPDs.
Embodied carbon can be measured by multiplying the GWP of the material, as reported in product-specific EPDs, by the quantity of material used. The embodied carbon impact of multiple designs can be evaluated by completing this process for all materials included in the project or wall type. This analysis is also the foundation of a Whole Building Life Cycle Assessment (WBLCA).
Multiple tools exist to aid the building industry in evaluating the embodied carbon of materials. One example is Building Transparency’s Embodied Carbon in Construction (EC3) Tool, which provides a database of EPDs that can be used to compare the upfront embodied carbon of building materials. The tool can also be used to measure the total embodied carbon impact of a building by adding material quantities. Another tool, Payette’s Kaleidoscope, focuses specifically on the embodied carbon of elements within the enclosure, flooring, ceilings, and partitions.
Embodied Carbon Impact of Common Facade-Insulation Combinations
The following explores the estimated range in upfront embodied carbon impact of common facade-insulation combinations throughout the lifespan of a building. In this comparative analysis, brick, metal panel, and precast facade materials are paired with various insulation options. Extruded polystyrene foam (XPS), mineral wool, and closed cell spray polyurethane foam (ccSPF) are included. XPS and ccSPF were analyzed with both hydrofluorocarbon HFC and hydrofluoroolefin (HFO) blowing agents. HFC based foam insulations are the traditional option, while foam insulations with HFO blowing agents have been developed more recently and have zero Ozone Depletion Potential (ODP) and low Global Warming Portiantal (GWP).
Wall assemblies were evaluated using One Click LCA, a well-known LCA software across the industry internationally. The following assumptions and considerations were incorporated into the analysis to ensure results could be compared:
- Industry-wide Environmental Product Declarations (EPDs) were used where available, capturing the average impact of materials across different manufacturers
- A 100-yr building lifespan was used for all enclosure designs, normalizing durability.
- Insulation thicknesses for each product type were calculated based on a consistent R-value of R-15 c.i.
- Typical concrete was assumed for the precast panels; low embodied carbon concrete measures are not represtend.
The box plot below (Figure 2) summarizes the range in impact of the facade-insulation combination analyzed and the matrix (Table 1) shows an estimated embodied carbon intensity of kgCO2e/m2. Wall assemblies highlighted in green have a relatively low embodied carbon and increase in intensity to those highlighted in red. Brick with HFO ccSPF results in the lowest impact, ranging up to Precast with HFC XPS as the highest impact.
Figure 2: Embodied Carbon Range (kg CO2e/m2) of Common Exterior Wall Constructions
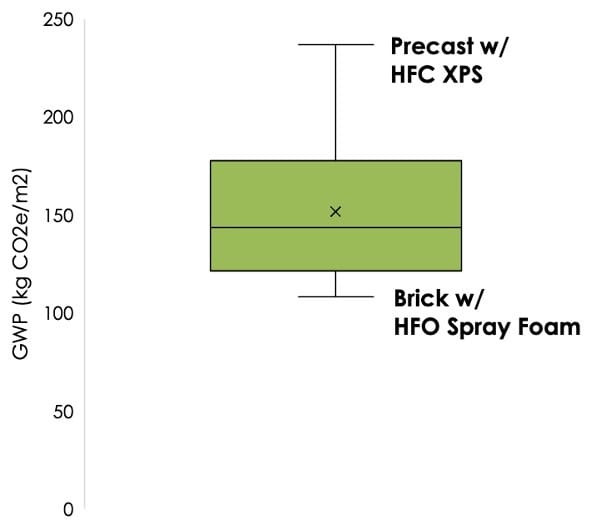
Table 1: Embodied Carbon Intensity—Facade & Insulation Materials (kgCO2e/m2)
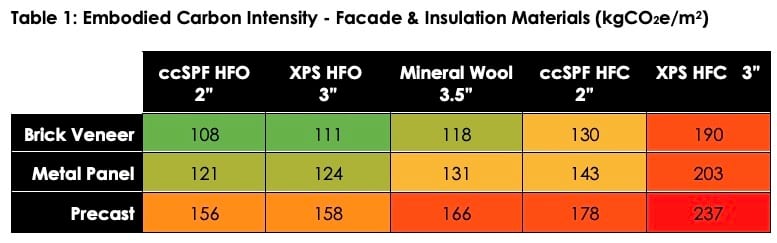
The above matrix provides a rudimentary guide for comparing the embodied carbon impact of common facade-insulation combinations, as there is uncertainty and variability in the data available. For instance, the use of industry-wide EPDs increases the uncertainty of data related to manufacturer, product, and supply chain impacts. Additionally, variability exists between unique products of the same type, which can be seen in the box plot below (Figure 3) which illustrates the embodied carbon range of mineral wool board products in Building Transparency’s EC3 tool database.
Figure 3: Embodied Carbon Range (kgCO2e per 1 ft2 RSI) of Mineral Wool Board
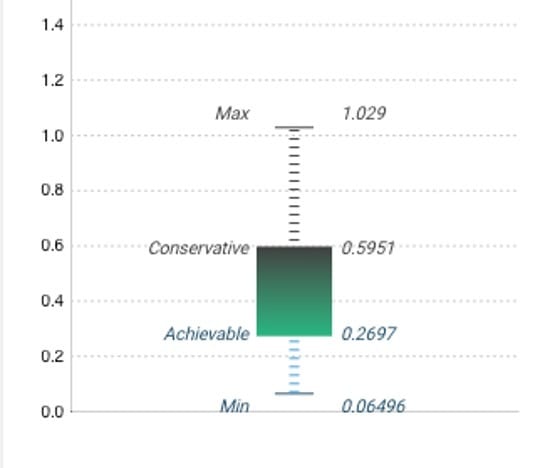
Embodied Carbon as a Decision Point
Embodied carbon can (and should) be evaluated alongside aesthetic, performance, and cost. We can do this by layering embodied carbon into the larger decision tree when comparing materials, assemblies, and whole project designs. And, because nothing exists in a vacuum, traditional considerations relative to lifespan, weight, cost, and construction impact directly relate to and influence embodied carbon.
Lifespan and durability: The lifespan and durability of a product or assembly impact embodied carbon because of replacement frequency. For example, precast panels are considered to be more durable with a much longer lifespan than metal panels. Although the metal panels generally have a lower embodied carbon, the impact of replacement could negate this. Consider the scenario where the building lifespan is only 50 years vs. 100 years due to material choice that is less durable. The embodied carbon impact could be more than doubled, if the building is demolished and replaced in the same 100 year timeframe. The image below (Figure 4) highlights the need for resilience and how critical it is to design and build durable, long-lasting construction.
Figure 4: High-rise building in New York City
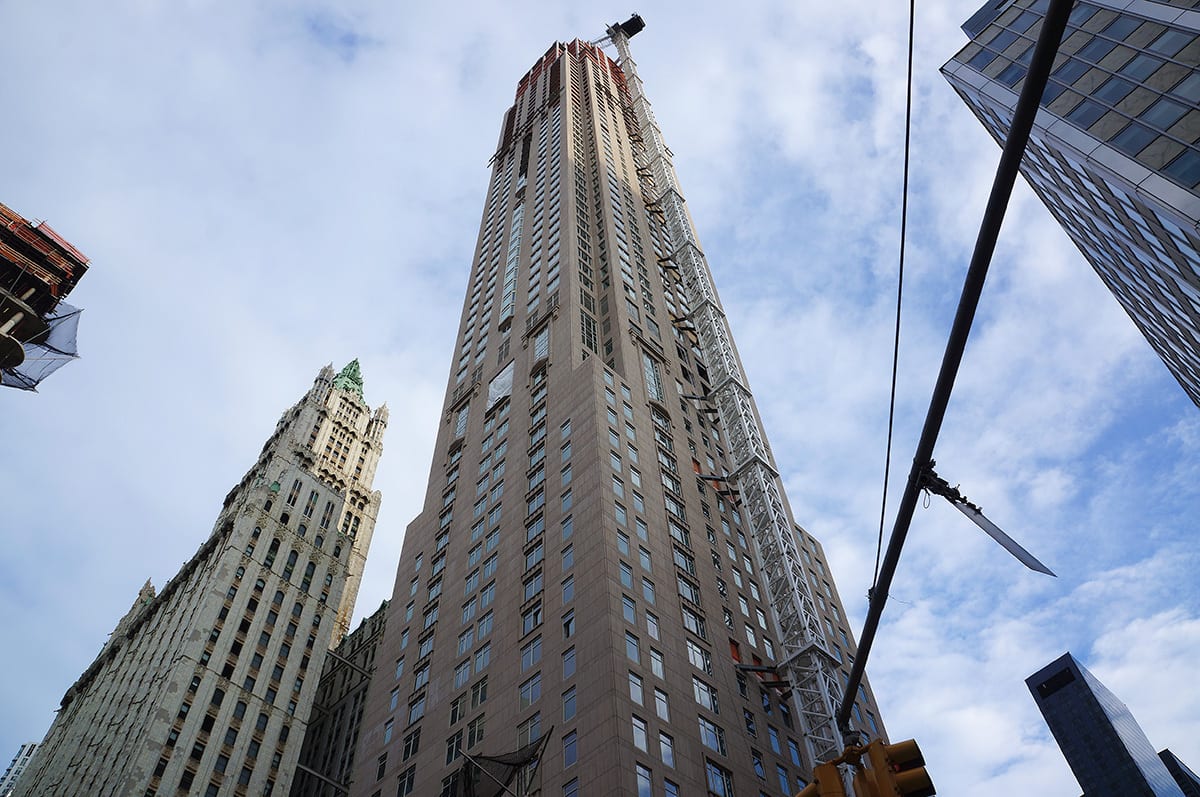
Weight: Conversely, the use of lightweight enclosure materials tends to reduce the amount of material required, and therefore the embodied carbon impact of a building. This is sometimes at odds with durability and may require unique engineering solutions that maintain both durability and low embodied carbon. For example, precast panels are a heavy material that may require more underlying support/structure than a lighter material. Exploring opportunities to reduce overall weight and support material could decrease the embodied carbon of both the structure and enclosure and therefore should not be overlooked.
Constructability: Ease of installation can reduce waste and emissions associated with construction activity. More efficient prefabricated or modular construction often decreases embodied carbon impact by reducing installation time and minimizing material waste.
The table below (Table 2) weights these considerations for common facade types, with green considered to be low impact or better and red considered to be high impact or worst. For example, precast facades are durable and have a long lifespan (considered a “benefit”) but are often heavy (considered a “limitation”).
Table 2: Relative Impact of Different Decision Points for Common Facade Types
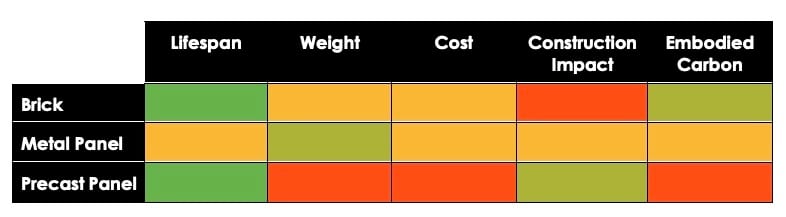
The introduction of embodied carbon in this matrix can help shape and influence the traditional benefits and limitations of each metric. Consider the following comparing options based on embodied carbon for the next project:
- Manufacturer/product-specific impact by comparing EPDs.
- Low-carbon concrete strategies for precast panels.
- XPS or ccSPF insulations with HFO blowing agent.
- Lightweight facade options, requiring less support or backing material.
- Ease of installation, decreasing construction impact and waste.
Call to Action
The most important action when it comes to embodied carbon is to start tracking it. Establishing robust targets or benchmarks for the embodied carbon attributed to construction projects is challenging due to the absence of a comprehensive data set for WBLCA models. The industry needs more data to develop a better understanding of the current impact of the building stock and to determine what steps are needed to reduce it. Manufacture recognition and understanding of EPDs and their place in the industry has increased substantially; however, EPD generation still remains relatively niche to specific product types and manufacturers. A broader request for EPDs from manufacturers will stimulate an increase in product-specific environmental impact data. This is key to conducting a Whole Building LCA which helps us better understand impact holistically. It is also necessary for the building industry to set benchmarks and make informed decisions on the construction materials that make up an increasing portion of our global carbon footprint.
References
- Embodied Carbon 101, Carbon Leadership Forum (2020): https://carbonleadershipforum.org/embodied-carbon-101/
- Architecture 2030: https://architecture2030.org/why-the-building-sector/