Opting for StoTherm® ci with StoCast Wood verses fiber cement, West Lake Commons Retail Center was drawn to its lightweight, flexible nature, and comprehensive high-performance system. StoCast Wood additionally provides a broader spectrum of stain options, allowing for both single and dual-tone depth of color. All photos courtesy of Sto Corp.
Location, location, location. Pleasing aesthetics for the exterior of any building are often tied to where that building is located. For example, in the Northeast, brick and wood are more desirable and therefore more prevalent as the go-to material for a building’s facade. In the Southwest, architects and building owners often rely on plaster to deliver traditional looks. The common denominator for today’s design is that one type of material is no longer good enough. Combining multiple aesthetics into the design of a building is the standard rather than the exception. Because the days of monolithic design are long gone, architects are pushing the limits seeking to integrate materials for a modern, sophisticated look.
At the same time, no designer can afford to sacrifice performance for a look that will turn heads. Ever-evolving, stricter building codes and heightened expectations from building owners and occupants demand the right balance between beauty, comfort, and durability.
How can designers, specifiers, and contractors capitalize on the growing trend of multiple aesthetic looks for a building’s exterior while also ensuring the building enclosure can withstand the forces of nature?
The connective tissue that helps solve the equation lies beneath what the eye can see. It is a singular, cohesive building envelope that relies on continuous exterior insulation. Employing materials that work in concert with each other as a system delivers key value propositions: design freedom, long-term performance, comfort, potential cost savings, and peace of mind.
Consider a building that may have concrete masonry units as a base, but then the sheathing transitions to glass mat gypsum or plywood sheathing on the upper levels. Specifiers can select a single fluid-applied air- and water-resistive barrier for these different substrates, which are also effective under multiple types of cladding—stucco, cement board, wood, vinyl, brick, stone, and metal panels. While the thickness of the fluid application may need to be adjusted depending upon the cladding that sits above or the substrate below, a singular product as part of a tested system ensures greater reliability and less complexity. The fluid-applied air and water-resistive barrier forms a bond with the wall sheathing and can act as a waterproof air- and water-resistive barrier when combined with joint and rough opening treatment.
When it comes to the thermal barrier, continuous insulation systems installed on the exterior of the sheathing deliver the greatest R-value and overall energy performance. The American Society of Heating, Refrigerating and Air-conditioning Engineers (ASHRAE)1 defines continuous insulation as “…insulation that is continuous across all structural members without thermal bridges other than fasteners and service openings.” Thermally insulating the exterior of the wall structure with continuous insulation wraps the building in a thick, well-insulated and protective blanket, thereby reducing thermal bridging. This keeps the wall structure warm and dry. Using continuous insulation on the outside of the wall maintains the temperature of the building wall structure above the dew point, effectively dealing with the potential for condensation caused by water vapor diffusion. For best results and virtual elimination of thermal bridging, a system in which the continuous insulation and wall cladding are adhered instead of fastened is ideal.
Advancements in material science now deliver thermal barriers for the exterior wall that provide even greater fire protection. Mineral wool insulation that is noncombustible, inorganic, and mold-retardant can resist fire and temperatures in excess of 2,000 degrees Fahrenheit. When mineral wool serves as the thermal barrier in a fully engineered wall assembly, it also allows the vapor barrier to do its job without creating additional traps for moisture in the wall cavity.
Aesthetic Options
Using a continuous exterior insulation system on the wall assembly broadens the range of possibilities for the exterior façade cladding. Architects and designers can marry the traditional looks of brick, stone, concrete, and stucco with the modern appeal of metal, wood, tile, and much more. For example, architects may choose to create the look of brick or wood over a continuous exterior insulation system by employing resin-cast shapes. Such an approach creates the time-honored look of traditional brick or wood without having construction crews lay brick and mortar or cut and ship lumber.
Architects can also achieve the look of brick, wood, concrete, stone, metal, and other materials using trowel-applied acrylic finishes or a variety of other exterior coatings. The result is a more durable surface that still delivers the desired aesthetic.
Also, certain finishes applied over the surface of the exterior cladding can dramatically improve the performance of the façade. Hydrophobic finishes repel water, keeping walls cleaner longer and providing greater protection against algae and mildew without sacrificing design possibilities. Super-hydrophobic finishes have self-cleaning capabilities with superior algae and mildew resistance.
The combination of StoVentec® Glass and StoVentec® Render Rainscreen® delivered a striking visual effect, utilizing glass panels on the fascia and render on the soffits, seamlessly integrated into one complete system. Not only did it meet the designer's aesthetic expectations, but it also excelled in performance and durability.
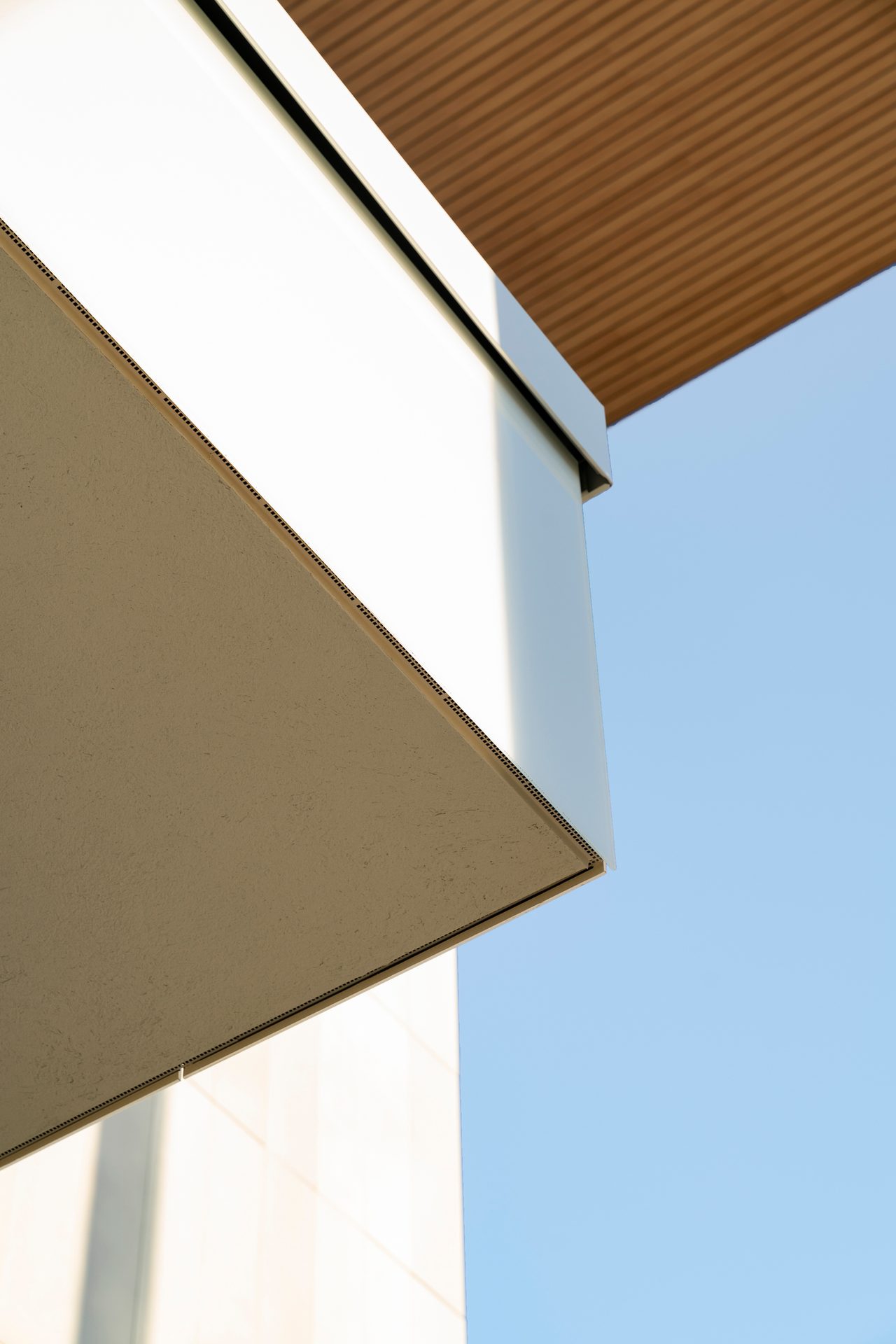
Big City Applications
Using the systems approach to the building facade produces enviable results in cities across the nation—in energy performance, in efficiency on the construction site, and in the aesthetic impact of the final product.
Take for example, 207 W. 75th Street in New York’s fashionable Upper West Side. This seven-story, seven-unit, residential building with a porcelain facade was so striking in appearance and so elegant in design until it came crumbling down. Literally. Entire sections of porcelain simply fell from the building onto the street below. This problem needed to be corrected immediately. The solution was a Level 4 Remove & Reclad to replace the crumbling porcelain with a StoTherm® ci system using Stolit® Milano ultra smooth finish to mimic the smooth appearance of tiles.
Architect Jeffrey Cole, of Jeffrey Cole Architects quickly diagnosed the issue. The porcelain on the original facade was not installed according to his detailed specifications and drawings resulting in large voids that allowed water to seep in. The mortar had so firmly adhered to the substrate that any attempt to remove it would result in tremendous damage to the building structure. So they created an entirely new, lightweight facade using an advanced building enclosure system that could deliver on the desired aesthetic option, which in this case was a porcelain tile look, while also delivering enhanced thermal performance.
West Lake Commons Lifestyle Retail Center is a mixed-use retail complex that, upon its completion, will feature a number of individual buildings dedicated to retail shopping, groceries, entertainment, and more. For its design, the building exterior needed to possess a timeless look that would offer enduring performance and a fully engineered system that encompasses all the control layers and came with a single-source warranty. That is why architects at Virgo Gambill switched their specification from fiber cement siding to StoCast Wood, resin-cast wood grain planks from Sto. In addition, StoCast Wood offered a much wider range of colors and an authentic wood appearance.
Thanks to Stolit® Milano's® ultra-smooth finish, 207 W 75th St. boasts a unique porcelain tile façade, cleverly mimicking grout lines with rendered trowel marks. The versatility of Stolit® Milano® enables various decorative options, ranging from a fine-grit texture to the industrial charm of metal panels, polished stone, and tile delivered in one complete system.
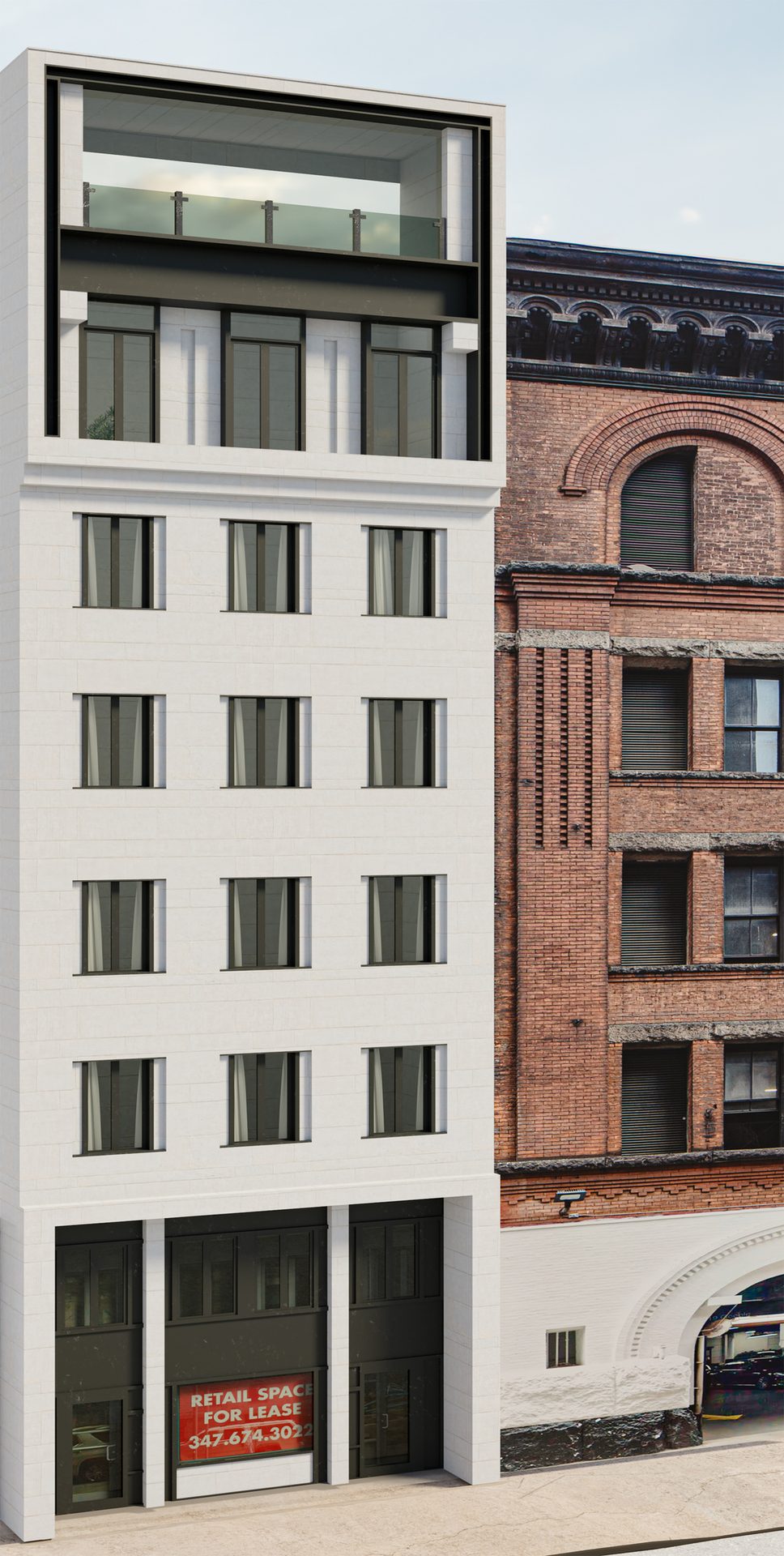
Make it Sustainable
Achieving sustainability goals has become an integral part of any conversation that involves a construction project. Engineered building enclosure systems that utilize continuous exterior insulation provide several key advantages when it comes to greater sustainability.
Lighter-weight cladding (think resin-cast brick versus traditional brick) allows for lower deflection criteria and offers weight relief. This means the building requires fewer structural components, decreasing the amount of concrete or steel required in a building. That can translate into cost savings and reduced embodied carbon for the building.
Construction projects also reduce their carbon footprint when they opt to ship lighter-weight cladding. Consider the savings of shipping traditional cubes of bricks versus boxes of resin-cast brick or pails of acrylic finish for exterior wall surfaces. It takes the equivalent of 15 trucks of traditional bricks to carry the same square footage as one truck of resin-cast bricks.
Then comes the lower operational carbon footprint generated over the lifetime of a structure. Engineered building enclosure systems with continuous exterior insulation produce a building that requires much less energy for heating and cooling than uninsulated brick, stucco, or metal panels. Moreover, cladding systems with exterior insulation use much less energy over the full life cycle of the building. This is driven by two key factors: Continuous exterior insulation delivers a higher total R-value, and it proves to be far more efficient than cavity wall insulation.
The National Institute of Standards and Technology (NIST), part of the U.S. Department of Commerce, develops testing, measurement and reference materials needed to ensure the quality of energy-related products and services. In NIST’s “Investigation of the Impact of Commercial Building Envelope Airtightness on HVAC Energy Use”2 prepared for the U.S. Department of Energy, recognized leaders investigated the impact of envelope air tightness on energy consumption in a typical commercial building. The study found that using an air barrier can achieve energy cost savings of up to 36 percent.
In addition, heavier cladding systems create more solid waste, both in production and at the end of their life.
Kalamazoo Justice Center sought a visually appealing solution to seamlessly extend the aesthetic of its modern glass curtainwall.
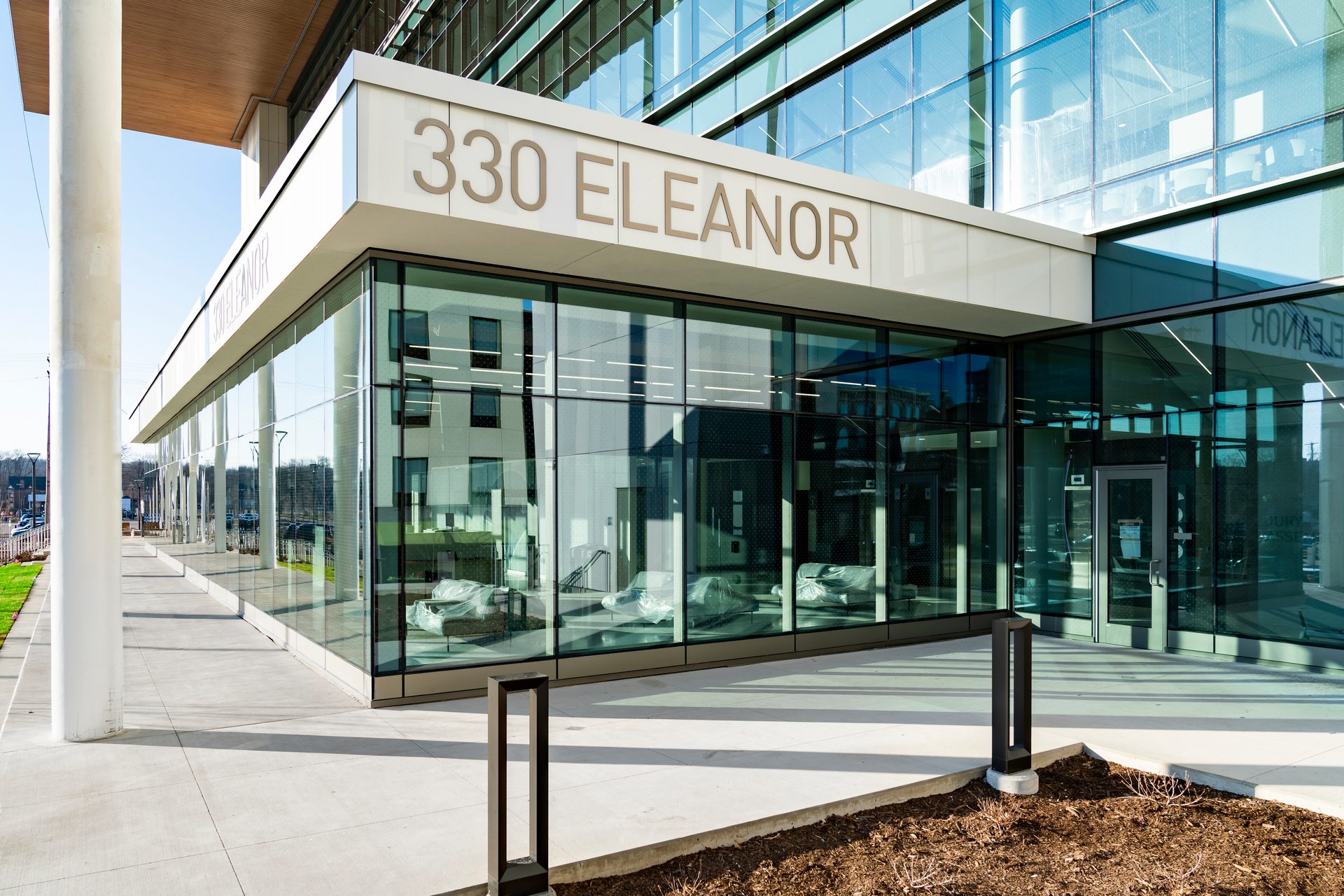
Engineered Building Enclosures
With engineered building enclosure systems, the value proposition on the construction site is also clear and unmistakable: Crews install one single building enclosure behind the facade. This means no issues with transitions between insulation and materials. The single barrier system is put in place by one installer, simplifying the production schedule and eliminating complications that can arise from using a collection of components. Using one installer for all components can also translate into fewer errors and faster delivery of the finished product.
Engineered building enclosure systems integrate continuous insulation, an air and moisture barrier, a drainage plane, and a variety of textured finish options to create sustainable, high-performance wall cladding. The system improves indoor comfort and air quality while maintaining curb appeal and lowering life-cycle costs.
Additionally, the system approach reduces the complexity when it comes to compliance. Contractors and builders can rely on testing the system rather than performing viability testing on individual components. This more readily ensures the safety of the building and its occupants, delivering peace of mind to all stakeholders in the value chain. From NFPA 285 fire testing to hurricane and wind impact tests, the system components are designed to work together for the optimal building envelope.
Building a facade with multiple aesthetic elements is the new standard. That vision is made easier with continuous exterior insulation systems. Architects can stretch their imagination, incorporating a wide palette of colors and textures to set the building apart while delivering a high-performing structure that meets or exceeds today’s building codes.
By reducing both the number of trades and suppliers involved in the sourcing and installation of materials, managers on a construction project can lower their budgets using continuous insulation systems, thereby achieving cost savings and greater efficiencies. That can lead to collapsed timelines, meaning a project can be delivered faster. Moreover, the potential for energy and cost savings improves the bottom line for all stakeholders and can help meet sustainability targets.
A building’s cladding is not a system in and of itself. While the exterior cladding is critical to both the design and functionality of the building, it is only one component of the building envelope.
With Sto’s variety of performative aesthetics, the designer of Parkview Senior Living was able to create a mixed aesthetic including StoCast Brick and StoCast Wood, and a textured finish with one fully engineered system.
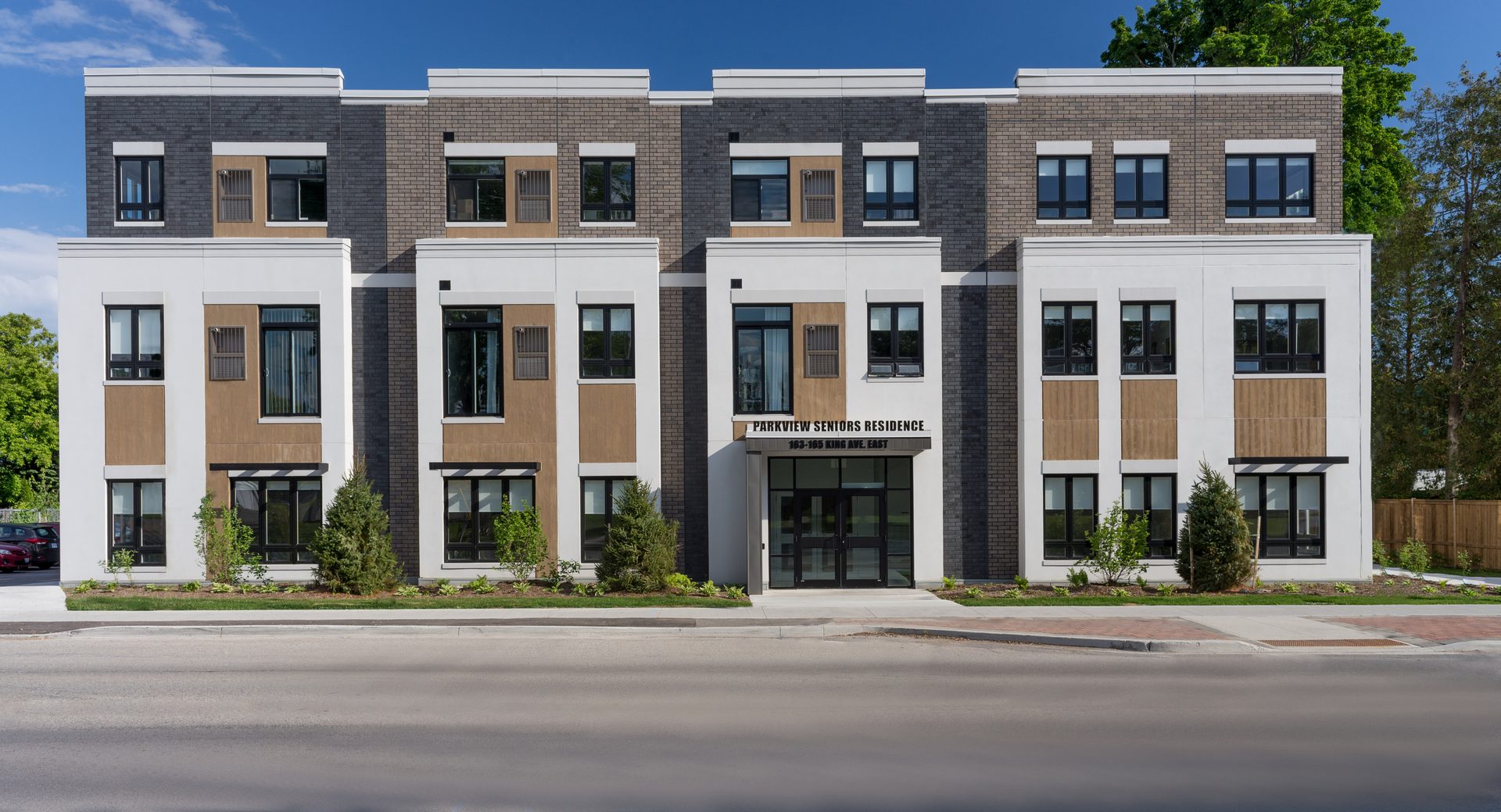