For centuries, copper and copper alloys such as brass and bronze have appeared on all types of structures, from family homes to the most prestigious institutions, universities, cathedrals, and museums. Although these metals have a well-established history of aesthetic appeal, excellent workability, superior durability, and inherent sustainability, construction teams should consider a number of design factors to ensure the success of their projects.
3131 CBR residence in Washington, D.C., by David Jameson Architect and Metal Specialties. Photo courtesy of Paul Warchol.
Center for the Arts in Crested Butte, Colorado, by Steinberg Hart and Andrew Hadley Architect. Photo courtesy of Tom Kessler.
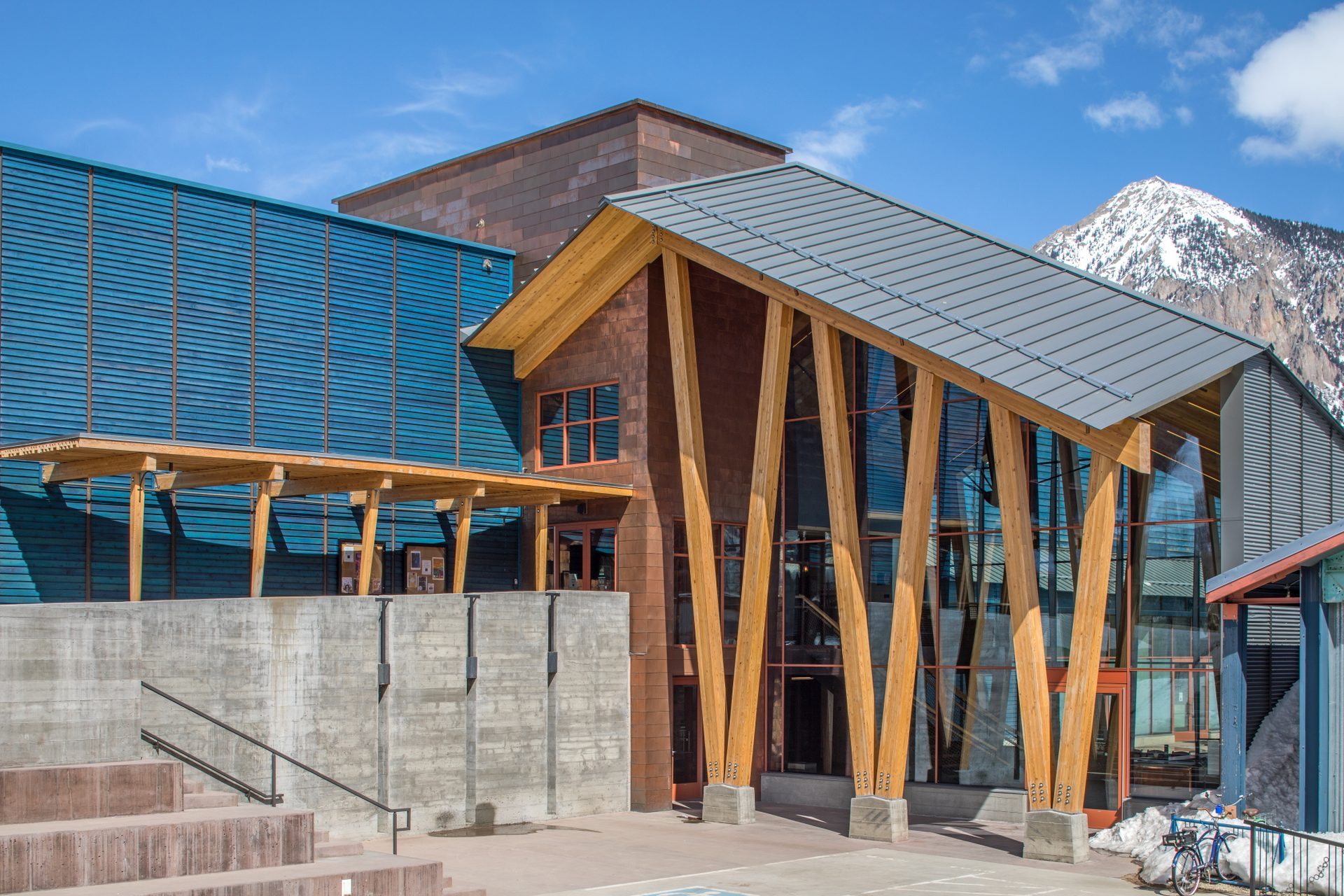
Private monument in Falls Church, Virginia, by Solís Betancourt & Sherrill and Wiemann Metalcraft. Photo courtesy of Wiemann Metalcraft.
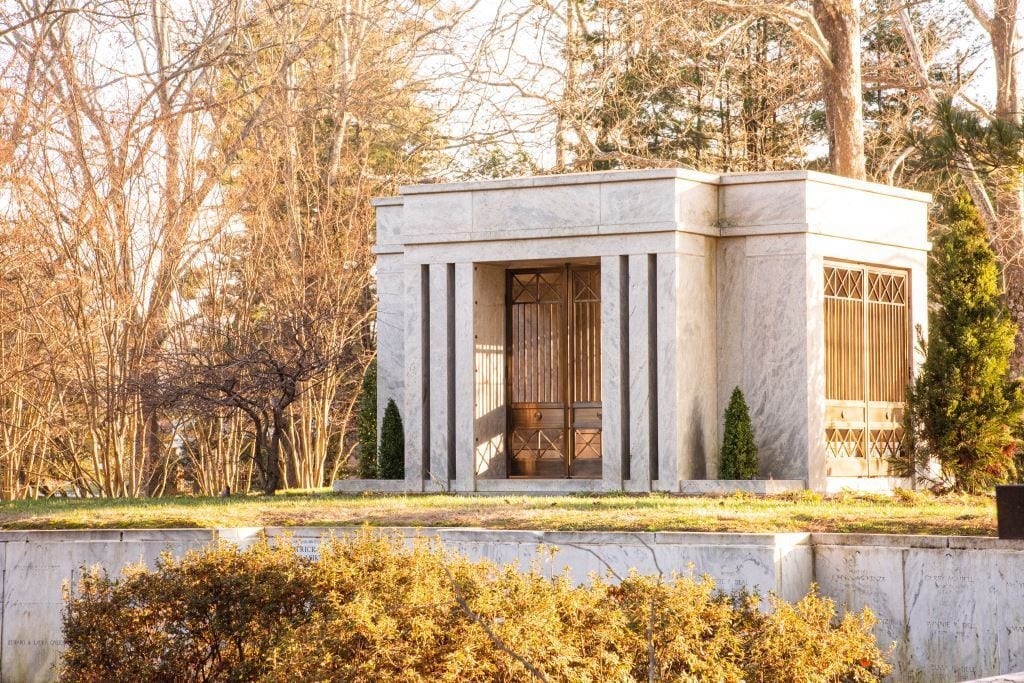
Over its 60-year history, the Copper Development Association (CDA) has developed a library of support resources for many types of copper applications including roof systems, flashing, and gutters; wall cladding; and all kinds of decorative elements. Examples include industry-standard details, testing results, and technical recommendations. CDA also supports design of other critical building systems, including piping, wiring, and HVAC components.
Based on learning from real-world installations, in this article we’d like to illuminate a few critical design considerations, including substrate selection; use of proper joining methods, flashings, solder, and sealants; natural weathering and other finishes; and staining and corrosion control and prevention. Our Copper in Architecture Handbook, available free of charge to the industry at copper.org, offers even more information.
Substrates for Copper Architectural Systems
The majority of sheet copper systems, such as roofing, flashing and wall cladding, are installed over a solid, smooth substrate capable of securing fasteners. Common fasteners include ring-shank copper roofing nails or stainless-steel screws. A good substrate will offer a smooth, dry surface; chemical compatibility with copper; and provision for fasteners. Substrates should provide a smooth, planar surface without protrusions, such as nail heads, washers, or other imperfections.
Project: Dawson College in Montréal, Quebec, by TLA Architectes and Toitures Trois Étoiles. Photo courtesy of Marco Mandato and Kevin Angers.
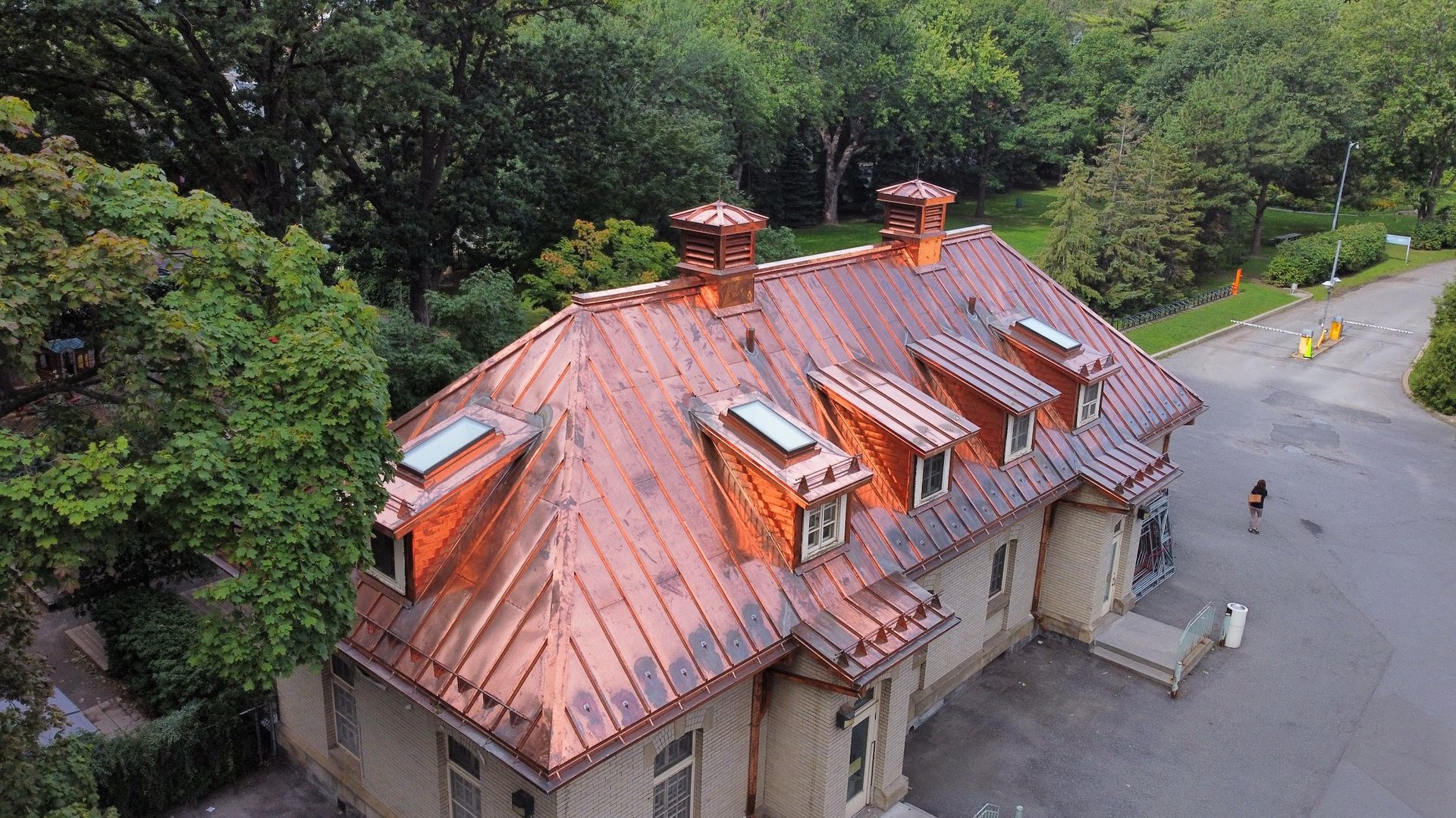
The most common substrate is wood, often 1/2" or 3/4" plywood. Allow wood to weather for a few days after installation to settle fully into place. During this period, installers need to ensure it is protected from rain, allowing it to conform to local atmospheric temperatures and moisture levels. If considering fire-retardant-treated (FRT) plywood and lumber, make sure to check with the lumber provider to insure FRT chemicals are non-corrosive to metals in the system.
Other materials used as substrates for copper include concrete, metal decking with insulation, brick, masonry units, terra cotta, and stucco. The guidelines discussed here apply to these materials as well.
An approved underlayment, commonly saturated felt, must be applied to the substrate. This material will cushion the copper sheets, provide temporary water protection during installation, and absorb incidental condensation. Placing a sheet of rosin-sized building paper between the copper and the underlayment will prevent bonding between the two surfaces that might otherwise restrict thermal movement of the copper.
Joints, Flashings, Solder and Sealants
Many common sheet-metal joints used with copper rely on its exceptional combination of malleability and strength. These include double-lock seams and flat seams. Other types of expansion-joint seams can be designed to allow for thermal movement of the sheet metal or movement of the building structure.
Martin County Courthouse renovation in Fairmont, Minnesota, by ISG and Renaissance Historic Exteriors. Photo courtesy of ISG.
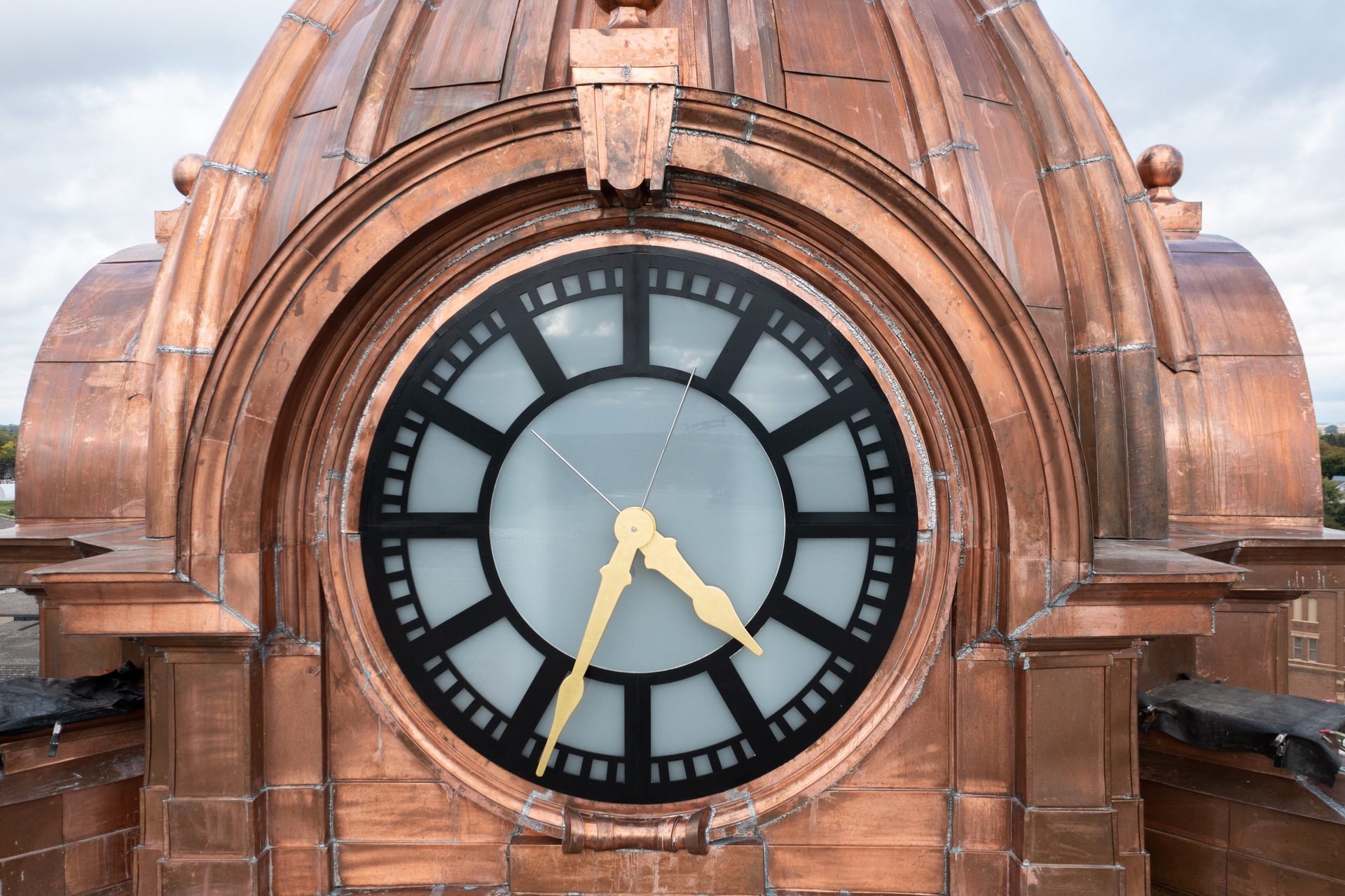
Traditionally, many copper seams rely on solder to ensure water tightness and provide strength. Properly soldered seams and joints should last the life of the copper and be considered as permanent. Acceptable solders include 50-50 tin-lead or lead-free tin-based alloys. It’s important for workers to utilize proper tools, such as soldering coppers, and incorporate procedures like pre-tinned seams, when joining copper elements. Many design professionals find that checking sample soldered joints both before and during construction can help preclude problems. American Welding Society (AWS) standard B2.3/2.3M “AWS B.2.3:2018 - Specification for Soldering Procedure and Performance Qualification Testing” can help increase confidence in selected seams. To limit stress fractures, teams should avoid continuous long runs of soldered seams.
In the weathering process, teams should be aware that solder turns from a shiny to a dull tone. In some cases, exposed solder in the finished joints can be minimized with the use of blind soldering, a technique in which solder is applied to the back or concealed edge of copper surfaces.
If additional structural strength is not required, sealant may be used as an alternative to solder. Sealant-filled joints have been used successfully within the seams of standing-seam and batten-seam roofing where roof slopes are less than three inches per foot. Sealants can also be used in joints that are primarily designed to accommodate thermal movement of the copper. All sealants should be tested and designated by the manufacturer as compatible for use with copper. Many elastomeric polyurethane, silicone, butyl, polysulfide, or other inorganic or rubber-based sealants have shown acceptable performance. By contrast, acrylic, neoprene, and nitrile-based sealants have been observed to actively corrode copper and are not recommended.
Understanding Patination and Managing Weathering, Staining, and Other Issues
Chemical reactions are responsible for corrosion, staining, and even the green patina that develops on copper surfaces over time. The oxidation process that gives copper its characteristic green patina is a result of exposure to an acidic atmosphere. When weak sulfuric/sulfurous acidic moisture (commonly present in rainfall) contacts exposed copper surfaces, it reacts with the copper to form copper sulfate. The acid is neutralized during the reaction with the copper. This copper sulfate patina eventually covers the surface and adheres tightly to it, providing a protective layer against further weathering. The process may occur more quickly in metropolitan, marine, and industrial areas where higher concentrations of acids occur.
Gould Memorial Library renovation in the Bronx, New York, by Beyer Blinder Belle Architects and Planners, Nicholson & Galloway, and Heather + Little. Photo courtesy of Elizabeth Leidel.

The pictured example shows the difference between green copper installed early in the building’s life as compared to the muted brown color of copper installed more recently. The accompanying chart illustrates typical progression as the metal oxidizes.
Copper weathering color chart by Copper Development Association.
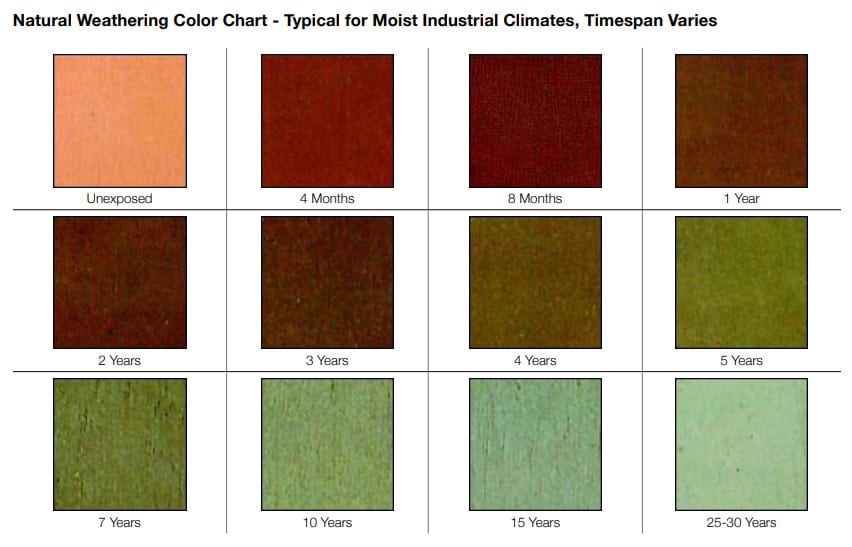
One of the most important issues concerning the use of metals is the potential for corrosive reaction between dissimilar metals, called “Galvanic Corrosion”. Every metal has a property called nobility, which measures the metal's resistance to corrosion when in contact with another metal. A greater relative difference in nobility between the two metals in contact indicates a greater corrosion potential. The table below ranks the most common metals used in construction in decreasing nobility, called the galvanic number.
Table: The Nobility of Common Metals
- Stainless steel (passive)
- Copper
- Lead
- Tin
- Stainless steel (active)
- Iron
- Steel
- Zinc
- Aluminum
When dissimilar metals come into contact with one another in the presence of an electrolyte, galvanic action may occur, resulting in deterioration of the metal with the lower galvanic number. The electrolyte may be rainwater running from one surface to another, or even moisture from the air containing enough acid to cause it to act as an electrolyte.
Burwell Center for Career Achievement in Denver, Colorado by Lake | Flato, Shears Adkins Rockmore Architects, and Roof Check.
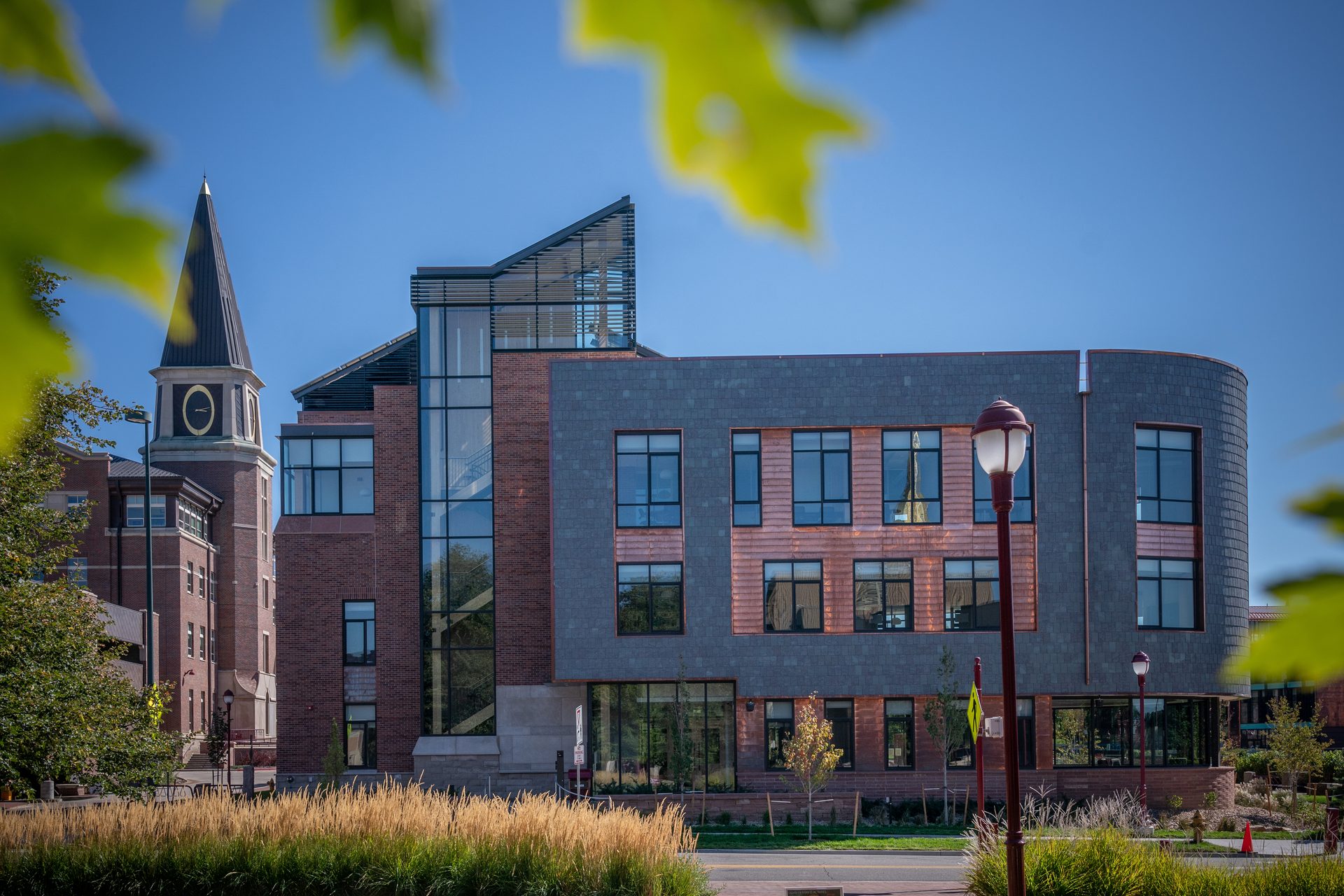
Since copper has one of the highest galvanic numbers or nobility of the active metals, it will not be harmed by contact with any of them. It may, however, cause corrosion of other metals if in direct contact or contact via ions within an electrolyte. It is not necessary to isolate copper from lead, tin, or stainless steel under most circumstances. By contrast, contact with copper by aluminum, zinc, and steel may cause concerns if they are of similar or less mass/thickness to the copper.
One solution is to prevent such direct contact with the use of separating materials, such as specific paints or gaskets. If paints or coatings are used for isolation, they must be compatible with both metals. Bituminous or zinc chromate primers can be used between copper and aluminum. To separate copper from iron and other ferrous materials, one can use red lead primer in addition to bituminous or zinc chromate primers.
Taping or gasketing with nonabsorptive materials or sealants also can effectively separate metals. In areas with severe exposure, lead or similar gasketing materials should be used, except between copper and aluminum. Regardless of the method used to separate the metals, one must prevent wash from copper surfaces from draining onto exposed aluminum or light gauge steel. Moisture in contact with copper surfaces tends to pick up small quantities of copper salts. Traces of copper salts in the wash could accelerate corrosion of metals with a lower nobility.
Similarly, designs should limit exposure of reactive materials immediately downstream from copper wash, such as marble or limestone. Such materials may absorb or react with the salts, staining them a greenish tint. The condition does not occur with heavy rains or similar rapid run-off since the dwell time of the moisture on the copper is short and it picks up very little copper salt. To reduce staining and mitigate its visual impact, implement one of these solutions:
Design systems that collect run-off in gutters and direct it into downspouts.
Specify drip edges to a minimum of one inch, helping reduce the amount of copper-laden moisture that comes into contact with material below.
Coat adjacent surfaces of porous material with a clear silicone sealant, minimizing the amount of moisture they will absorb.
Studio Building renovation in Portland, Oregon, by Hennebery Eddy Architects and Harder Mechanical Contractors. Photo courtesy of Harder Mechanical Contractors.
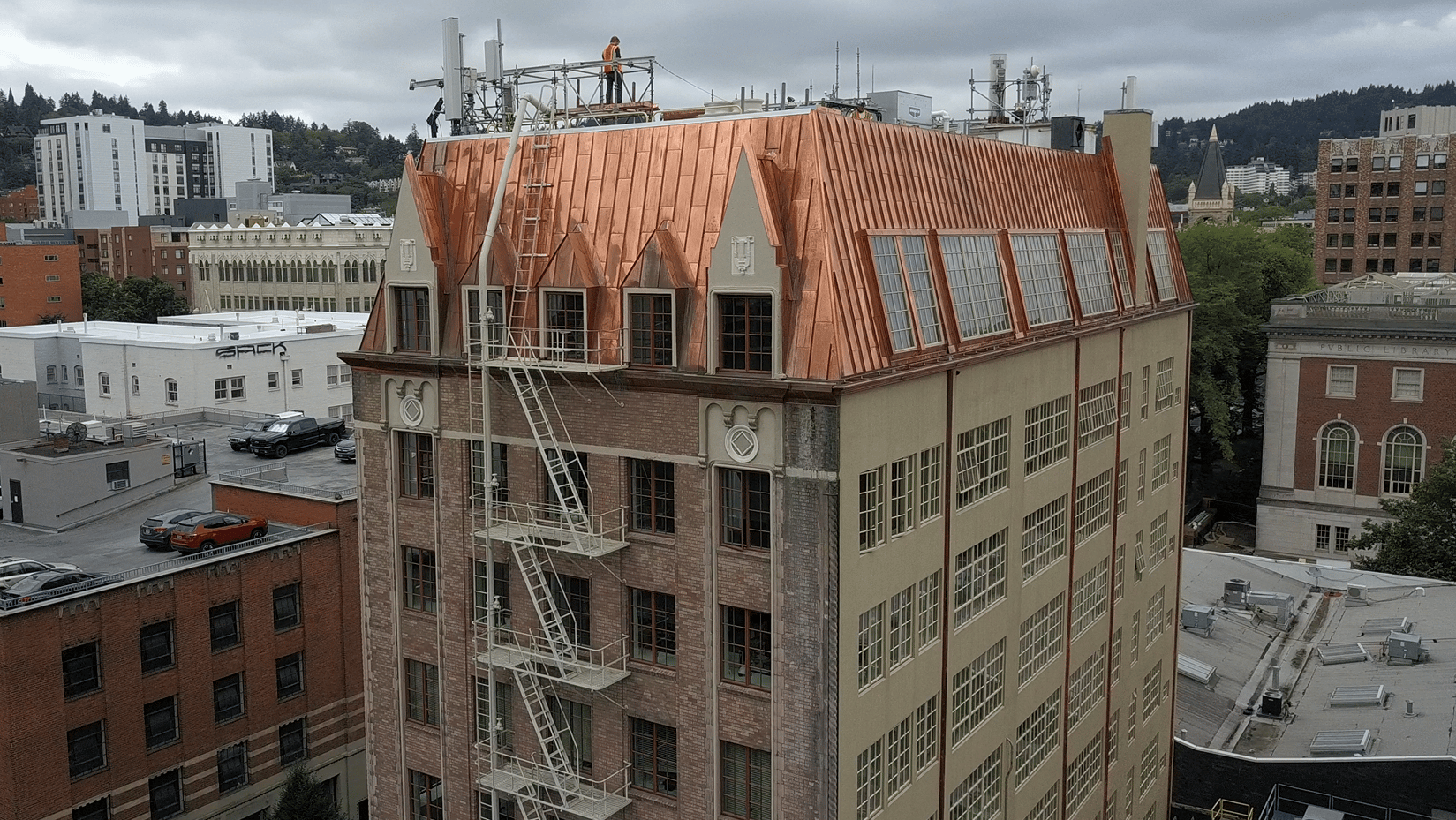